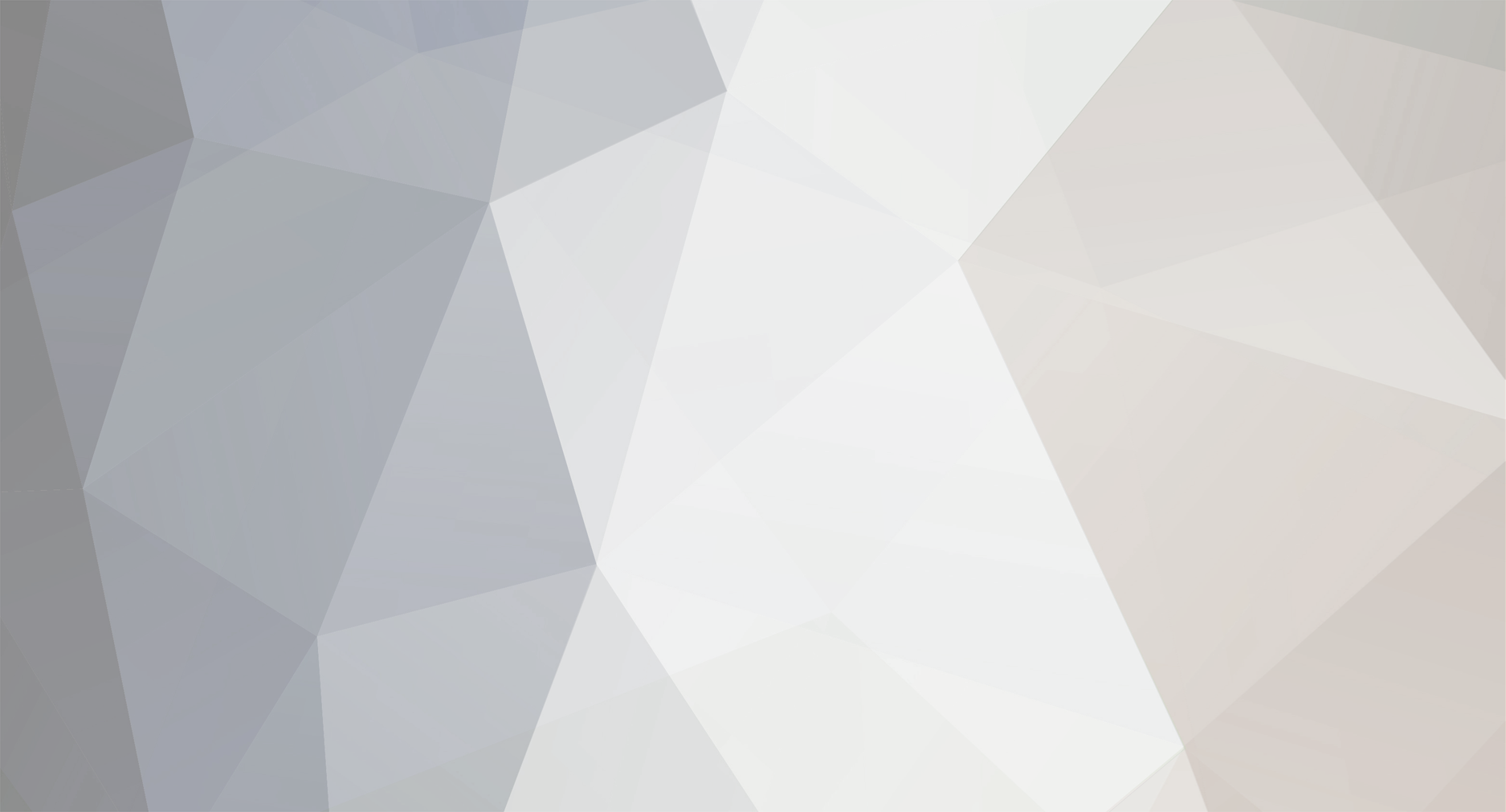
Dirk DeJonghe
-
Posts
740 -
Joined
-
Last visited
Posts posted by Dirk DeJonghe
-
-
1. process the exposed film received from camera crew.
2. make workprint (eventually transfer sound to SEPMAG)
3. edit workprint on film editing table (if all else fails on the kitchen table with scissors)
4. send edited workprint to negative cutter for conforming (reads keykode numbers on workprint and conforms negative accordingly)
5. prepare for filmgrading by noting shot changes, and discussing with DOP
6. filmgrading on Colormaster, simulating the printlook from the negative using only RGB light changes, making a list of FCC-RGB data (where the lights have to change and printing lights, eventually fades and dissolves)
7. negative laced up on printer, paper tape read in Printer Control Unit, lights out, printstock laced up and start button pushed.
8. after print run, exposed printstock is processed.
9. screen print with customer, note further grading changes required, goto step 6. and repeat.
-
1
-
-
The MTF curve takes into consideration the resolving power of the camera lens, the filmstock and also the scanner.
As a comparison, at the frequency of 20lp/mm, on 1K you will have 30% modulation response, on 2K 57% and on 4K 63%.
It is a matter of diminishing returns, there is a very noticeable improvement from 1K to 2K, from 2K to 4K it is much less.
These measurements were done on 35mm camera negative, 16mm will be more limited of course.
-
1
-
-
Because the cyan layer used to be fairly unstable and faded with age. When restoring old faded film, we have to increase the gamma of the cyan layer in order to bring the three layers more parallel, then do color correction. The current printfilms are much more stable now than they used to be before the mid 80s.
-
Will,
We have done dozens of commercials as well as sections of feature films and entire films. On one particular commercial for Vaseline, we used 500T, 200T and 50D to show different timespans, from mid 1800s to Vietnam to present day. It can be seen on vimeo:
Another one, completely on 500T to simulate a 1960s film is on Amazon Prime: Guava Island.
-
One problem with cutting the internegative is that you can only get polyester base stock. Splicing is only via ultrasonic splicers, not known for high quality splices.
The alternative is to use pull-processed and pre-flashed camera stock such as 7203 or 7213.
Note: the current 'official' internegative also benefits from preflashing and pull process.
-
There used to be an extra anti-lightpiping layer on negatives. One day Kodak told me they were no longer putting this layer in since it was only on stocks to be spooled on "daylight spools".
This was in the days of 7245.
-
We have a process called RFG. We record the digital files to 35mm camera filmstock (500T or 200T), the rescan the film back to digital DPX log files for final grading. We try to match the main primary colours but let the secondaries float.
A recent example of our work can be seen on Amazon Prime: Guava Island.
-
1
-
-
I suppose they gave you the D-Min values (perf area?) to show if and how much the filmfog has increased due to old age, radiation etc.
First to know is which filmstock and compared the values to a known fresh stock reading.
-
The problem with x-ray exposure is that it is directional. It will appear as uneven density changes mostly blue/cyan in the shadows. I have received a box of 40 100ft spools. Only the spools on the outside had a visible exposure, the x-ray had exposed the box from the short side and not penetrated more than one row.
Anyway, exposure is cumulative and each pass adds something.
-
Big difference between low-dose hand luggage and checked luggage.
Depends on how 'visible' the contents were in the scanner. If you hide the films in a lead bag, the operator will turn up the dose.
I always recommend to ship by Fedex or similar. We recently did a test with the help of Fedex and after eight passes, the increase in D-Min was less than 0.02 (densitometer tolerance). It all depends on the settings of the x-ray machine.
-
1
-
-
Ken Loach: "Sorry We Missed You " (2018, in postproduction)
-
John,
Send mail to info(at)postproduction.be
-
Two years ago we processed and scanned this Super16 Double-X short, the result had to look like a mid 1960 period.
-
We had a server failure. Will put a new website on a new server in a few days; email and telephone work normally. We have backups but they need to be transposed;
-
I have seen many rolls damaged by X-Rays. I am sure any lab can tell you horror stories.
They look like a pulsating blueish fog. We can even tell if the X-ray exposure was before or after the camera exposure by the increasing rythm of the pulsations. I have one customer with a full carton of 100ft daylight spools; the box must have passed the x-ray machine looking at the short edge. The first two rows of cans were damaged, the second one less than the first one, the X-rays did not penetrate more than two rows of cans.
The world is a changed place since the war on terror.
All I can say is that the film is most likely total loss, no easy digital fix.
-
It is on a 400" spool and is long pitch perforated; if you have a camerajam with polyester stock, you camera may be damaged.
-
1
-
-
Thanks for the referal. Our website is off-line for the moment due to a server failure, we we are doing business as usual.
-
The Minima uses the inside of the flanges to drive the take-up spool. It also pushes open the gap between the flanges once loaded. No way to run cores only or 100ft daylight spools.
-
We still do quite a bit of optical reductions. There are several reasons: the first and most common one is to make 16mm prints from digital files, we cannot record directly to 16 but we make very good quality 16mm direct reductions or via IP/DN. The other reason is to have 16mm prints from either 35mm or S16 originals for loop projection in art installations, the projector is part of the installation in full view of the public.
-
The current negative films are more easily edge-fogged during loading. There used to be an extra filter layer on the base of the 100ft spool filmstock that was removed about 15 years ago. Always load the "daylight spools" in as little light as possible.
-
This makes sense, the Takumar is a 35mm stills lens with a large exit pupil. A lot of light will hit outside of the filmgate, scattering light and bouncing off reflective surfaces.
-
You can use 100' spools on the feed side. You need to remove the core adapter using the small screwdriver that is found inside the feed side of the magazine. You will loose the mechanical footage counter. You cannot use a spool on the take-up side, only a core, so you will have to unload the exposed film in a changing bag or darkroom. Using spools on an Aaton is an emergency solution, not recommended if you can help it.
-
We have a fair number of clients from Norway for processing and printing 16mm, colour and B&W; let me know if you want to ship, customs value needs to be below 22€ to avoid delay and expenses;
-
We have several cinematographers also taking stills on 135 cartridges, Vision3 50D and 500T. We process them in ECN2, as long as the minimum charge of 55€ is covered. Some people bring in 10-15 cartridges, we process and deliver them on a roll. Many decades ago my father started a photographic stills lab, I started doing MP in 1973, processing ME4 for both 16mm and 35mm slides.
Math based film emulation. Alexa to 5219 color science
in Post Production
Posted
The link to my (temp) website is fixed. We use split screen with the original digital image and recorded negative. See my previous post.