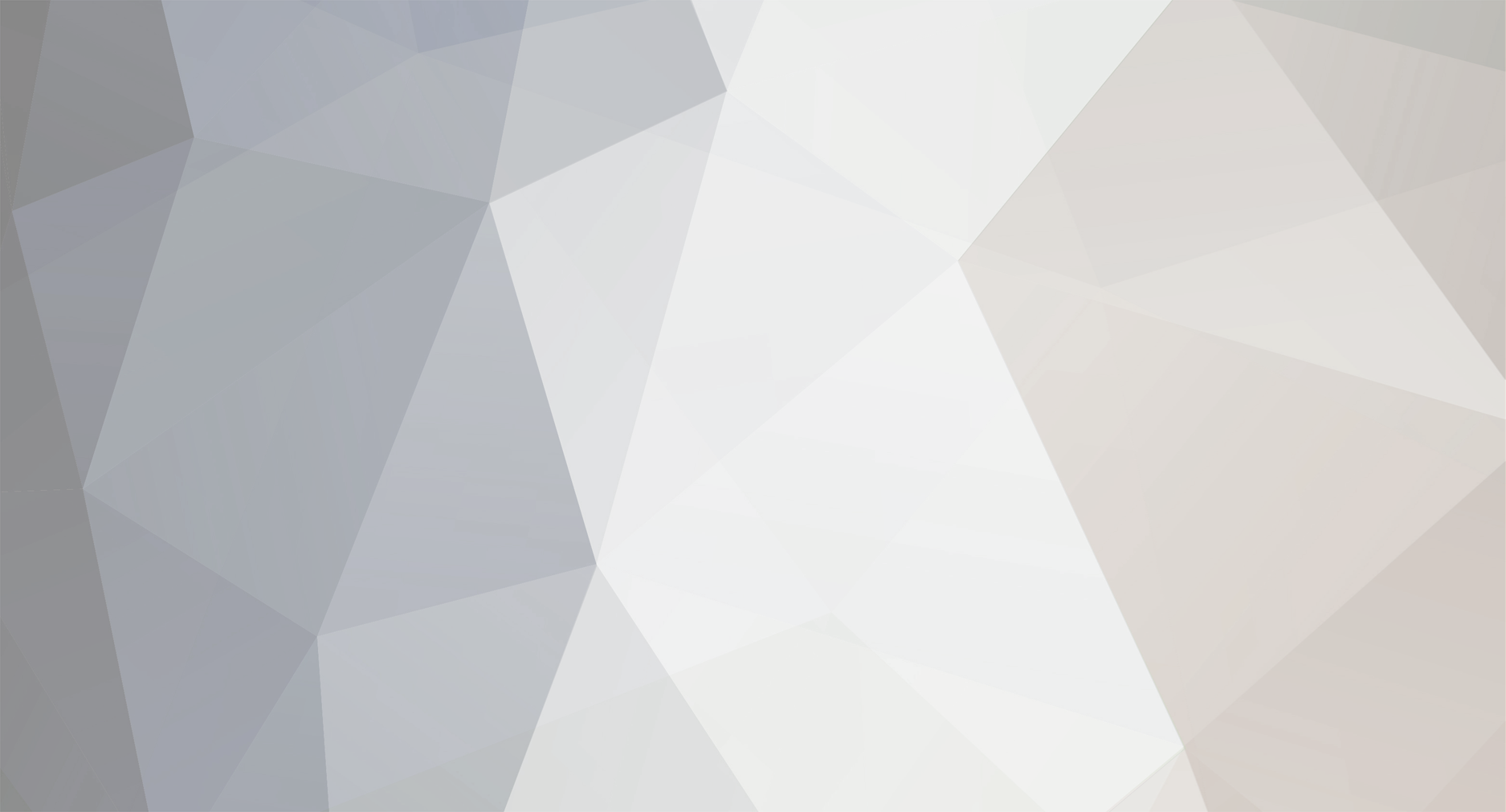
Dirk DeJonghe
Basic Member-
Posts
740 -
Joined
-
Last visited
Profile Information
-
Occupation
Industry Rep
-
Location
Kortrijk,Belgium
-
My Gear
Aaton 35-III, Aaton XTR-Plus,
-
Specialties
All film related activities; full analog film workflow color and B&W; traditional film grading and printing (16, 35mm), digital grading Baselight, digital recording and scanning, film restoration; digital archiving of film (8, 16, 35mm), video and audio. RFG digital to film to digital process.
Contact Methods
-
Website URL
https://www.postproduction.be
Recent Profile Visitors
-
Another factor to consider: the blue layer is the most grainy one of the three, but also contributes least to the image; in a tungsten film, the blue layer needs to be more sensitive because the tungsten light sources are less potent in blue energy. This makes that a daylight film (250D) is less grainy than a similar tungsten type (200T) when blue sky etc are involved. This said, (reasonable) grain is no longer considered as a defect but as a feature. We worked for a famous british director, first name Ken, who shoots on S16 because it matches his storytelling very well, if you have seen his films you will understand.
-
Goodbye remjet, hello AHU?!
Dirk DeJonghe replied to Joerg Polzfusz's topic in Film Stocks & Processing
It still remains a problem with Double-X B&W negative film, AHU would not work and the grey base is the only anti-halo protection provided. It would still be a good idea to find black chromed pressure plates instead of shiny chrome. -
Goodbye remjet, hello AHU?!
Dirk DeJonghe replied to Joerg Polzfusz's topic in Film Stocks & Processing
I ordered Super8 colour negative films today, two of the 3 stocks are now delivered with AHU, new Cat number, no choice when the old stock runs out. -
Dye Fade Tool in Diamant Restoration Suite
Dirk DeJonghe replied to Todd Ruel's topic in Post Production
We use PFClean since about 20 years or more, it has been very stable, we get good support when we need it for special cases. We run on Linux 95% and Mac 5%. -
Goodbye remjet, hello AHU?!
Dirk DeJonghe replied to Joerg Polzfusz's topic in Film Stocks & Processing
ECN2 uses CD3 developing agent, C41 uses CD4, you would get an image but it would be off colour. If the bleach bypass retains the silver in the image, then the AHU may interfere with proper scanning of the negative. -
Goodbye remjet, hello AHU?!
Dirk DeJonghe replied to Joerg Polzfusz's topic in Film Stocks & Processing
We used three 1000ft rolls of this new remjet-less emulsion about 6 months ago and had no problems in an Arri 535B. If any, it looked very clean, it was still experimental and the curves were not yet perfect. -
Restoration of 16mm Technicolor & Fujicolor Cartoons?
Dirk DeJonghe replied to Alex Landherr's topic in General Discussion
Hello, We are in Belgium and work for many international film archives. We can scan the original print with optical soundtrack, do digital restauration picture and sound, colour grading, and make a new 16mm picture and sound negative, then print to 16mm print for projection. We can also do scans from 8mm or Super8. It is hard to quote a digital restauration price without seeing the current state of the 16mm original print. -
Tyler, We had problems with Aaton XTR with 7222, it shows up as vertical stripes on panning shots over a grey wall for example; this can happen if you overexpose. The light striking the emulsion is travelling through the emulsion and getting reflected off the shiny parts of the film pressure plate and exposing the emulsion from the back a second time. Never a problem with regular rem-jet color negatives. This happened on Aaton 35 as well (5222 only). Also the Lasergraphics film recorder's pressure plate had to be blackened because the diagonal pattern would show up on direct to color positive filmouts.
-
DHL X-Rays and shipping film overseas
Dirk DeJonghe replied to Hwang Toe's topic in Film Stocks & Processing
If you look at the pulse frequency at the head of the roll and compare it to the pulse frequency at the tail, if head frequency is larger then the x-ray exposure happened before camera exposure and vice versa. Use a waveform monitor and measure peak pulse to peak pulse in frames. You can visualize this like driving a nail sideways into the roll. Here is some more information on the firebomb attack on DHL, it is blamed on the Russians, but in these times, nobody can be sure about this: Firebomb attack DHL -
DHL X-Rays and shipping film overseas
Dirk DeJonghe replied to Hwang Toe's topic in Film Stocks & Processing
Since last summer, after 2 firebomb attacks on DHL (Leipzig and Manchester) , their x-ray inspection has been increased in intensity. We had several instances of DHL x-ray damage and stopped using them except for local shipments inside the country. We can easily see if the x-ray exposure happened before of after camera exposure. We shipped via DHL Brussels to all continents, mainly Europe. For 250D and 500T we could see pulsating blues in the black levels. So far, Fedex has been fine; they allowed us to test, we asked them to put 500T through the scanner, 1x 2x 4x and 8x. Nothing could be detected. When possible we ship Fedex (road), no x-ray inspection involved. Kodak used to ship via UPS Air to us, but they had new CT scanners two years ago and now Kodak ships UPS ground. -
This document may help to get you started with Cineon Log files in Resolve: one way to do it, not the only way. CineonLog_DaVinci_2024_12.pdf
-
There was a large production planned for beginning of this year, the fresh stock was delivered by me late November directly from Kodak warehouse. However, the production is stalled and may take a long time to resume. The stock (at the old Kodak prices) is very good value and included our processing and 4K Prores4444XQ scanning. 23 rolls of 5213/400ft and 22 rolls of 5219/400ft. If interested, let me know.