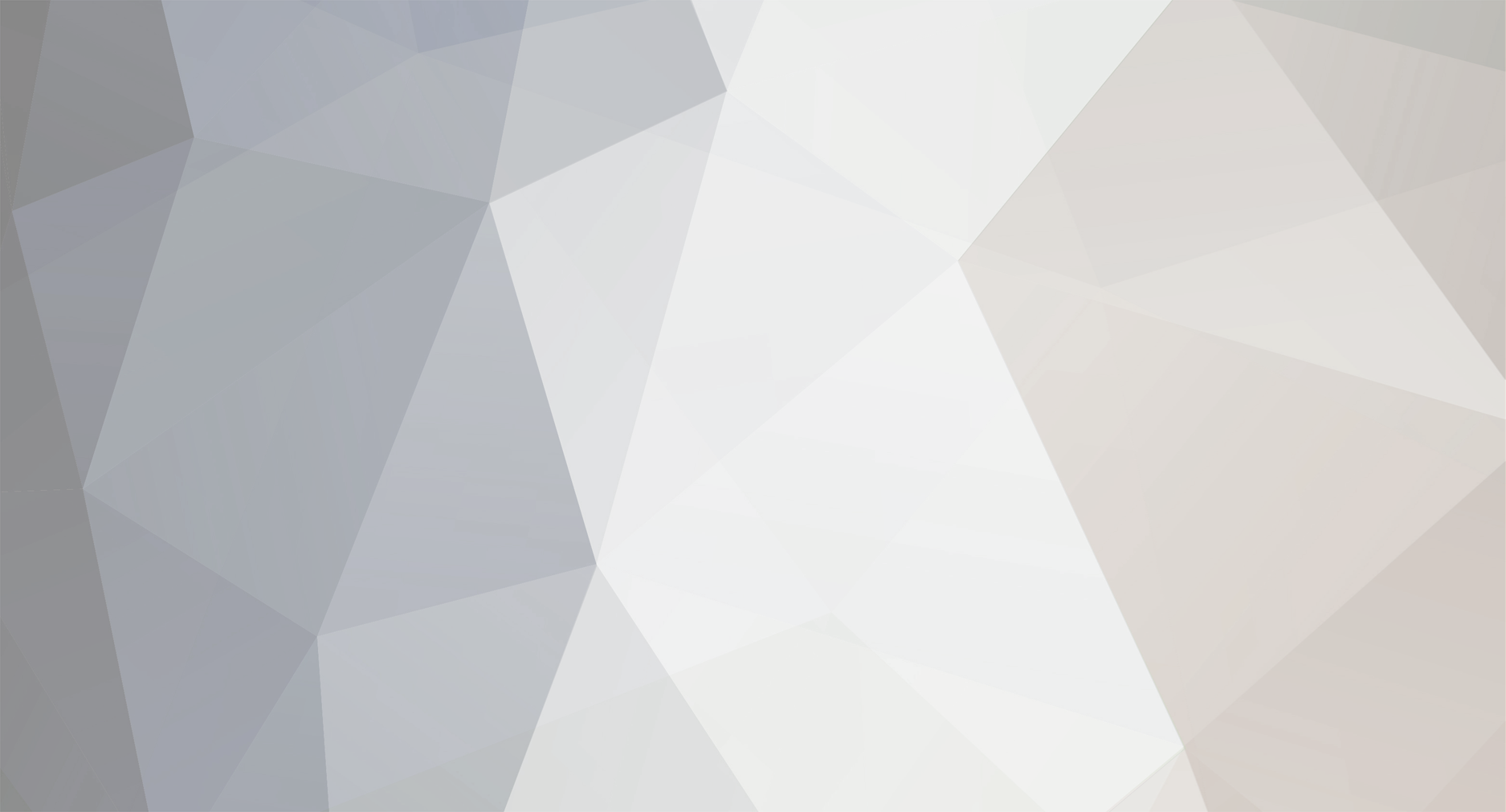
Brian Pritchard
Basic Member-
Posts
341 -
Joined
-
Last visited
Everything posted by Brian Pritchard
-
Controlling Print contrast
Brian Pritchard replied to Marc Roessler's topic in Film Stocks & Processing
Normally you would use whatever combination of time and temperature suit your processing machine so that if the machine was set up to give maxmium throughput you would need to reduce temperature. Running very slowly or very fast can affect the evenness of development. Also, of course running faster to reduce the contrast will mean that all the other stages will get less time so you might have a problem with correct fixing and washing. It is not normal to alter development times in colour print processes as you will get unwanted effects such as differantial shifts in the contrasts of the three layers giving rise to cross-overs; red highlights and cyan shadows for example. There are other ways to reduce contrast in a print such as pre-flashing the stock (this can also be used for colour print) and a stills technique called unsharp mask. You can read about this technique in any good stills photography manual. Another technique is to make a lower contrast dupe negative, and dupe positive if required. You can't use the filter system that is used in Multicontrast paper because it is coated with two emulsions with different contrasts that have different colour sensitivities. Changing the colour of the light source changes the contrast. If you alter the processing time or temperature the change will also affect the contrast and density of the sound track. The change in density will have to be compensated for during exposure. The change in contrast should not be a serious problem as far as sound quality is concerned as long as the density is right. Brian -
diff. between intermidiate neg. and pos. stocks
Brian Pritchard replied to chris hoag's topic in Film Stocks & Processing
7234 is a grey base low contrast negative stock. 7366 is a clear base positive stock. These two stocks and their polyester equivalents are designed to have an overall contrast of 1.0, approximately, so that you end up with a duplicate negative with the same gamma as the original. If you use a positive stock to make your internegative the contrast would be way too high. In fact you should really make a lower contrast negative, gamma about 0.45, when printing from a reversal original which is of projection contrast. Brian -
There are many hundreds of developers with different compositions. They will all give different results. When Black and White was king each lab had its own formulation for neg and pos baths, some labs also had a high-contrast bath for developing sound negatives. Some labs used MQ developers and some phenidone developers. There is no reason, other than persuading a lab to install a special bath, for you not to use any developer. Developing neg through a pos bath will increase the contrast, grain and speed but if that is what you want they just go ahead and do it. If you don't experiment you will never find out. If you want the very highest quality, good gradation, low grain then you correctly expose the negative and process it through a high quality bath. If you need something else then change whatever you want, but don't blame me if you get horrible results! If someone had not suggested bleach bypass then this effect would never have been seen. It is not the 'official' Kodak ECN2 process but certainly gives a different look. Brian.
-
It is perfectly true that the biggest change in Latent Image occurs immediately after exposure; it starts within seconds of exposure. The SMPTE book 'Control Techniques in Film Processing' reccomends that labs should do Latent Image Tests to see what changes occur on different stocks so that they know how long films can be kept before processing. A highly technical article 'Latent Image Stability of Film' in the SMPE Journal Volume 36 (1941) page 374 describes aging tests on various films and found that with long term storage of exposed film the negative films available at the time showed a 1/2 to 2 1/2 stop increase in speed as well as an increase in grain. It went on to say that the speed increase was mainly at low densities and at high densities there was speed regression. Films were kept up to a year. I would always recommend that films are processed as soon as possible after exposure, if this is not possible than as Charles says, they should be kept cool and dry. Brian
-
Wooda This was answered in 2007 go to this message to find the tables. http://www.cinematography.com/forum2004/in...showtopic=28046 Brian
-
Is single Perf the same is Super 16?
Brian Pritchard replied to Nick Centera's topic in Film Stocks & Processing
When 16mm was first introduced all filmstock was double perforated. It wasn't until 16mm sound was wanted that one set of prefs were removed to make way for the sound track. In 35mm the sound track occupies part of the picture area between the perfs, this would have meant an unacceptable reduction in picture area if the same method was used for 16mm, so to preserve picture size, the second set of perfs was removed. For many years both single and double perf camera originals were used and mixed. There were only a few 16mm cameras that had double perf sprockets and could only use double perf film. When 16mm film is printed, only a single set of perfs is used; double perf film can be printed onto single perf print stock and the sound track printed in the area where the second set of perfs would have been. Cutting copies are usually printed onto double perforated print stock to make it easier to run through a Steenbeck witout worrying which side the perfs are on. When most 16mm film was used for television via a telecine and an optical sound track was not required, Super 16mm was invented to give a larger picture area using the sound track area for picture. Often Super 16mm was used for blow-up to 35mm so the fact that you could not have a combined sound print from a Super 16mm original without cropping the picture, did not cause too much of a problem. Brian -
Photochemical color timing
Brian Pritchard replied to John Butler's topic in Film Stocks & Processing
Even today VCR's are not 100% accurate; invariably the grader will have to make sight corrections to produce an acceptable answer print. The first lab I worked in, Filmatic, was still sight grading colour in 1971 when we purchased our first Hasletine VCR. The grader went through the negative, grading for density, a print was made and he would then colour correct by eye. Most of our graders could get an acceptable answer print on the first attempt. We were also colour reversal grading which was all done by eye and continued to be, even after the arrival of an analyser. Today when making graded internegatives from colour prints or reversal originals I still sight grade, using filters to verify the colour correction required, even though the Kodak Analyser at the lab has the facility for positive to positive grading. Brian -
Photochemical color timing
Brian Pritchard replied to John Butler's topic in Film Stocks & Processing
I don't think you are 'spouting gibberish', John. The only way to get a 'film look' is to make a print from a negative. Whenever DI's are introduced there will be some changes to the image colour, structure and definition. Invariably some colour changes are introduced purely by the video setup method and it is unlikely that the colourist would not introduce some changes to the colour palette, one of the reasons for going through the DI route anyway. I am sure not everybody will agree but that is the way I see it. Brian -
Leader at the end of a 16 can?
Brian Pritchard replied to Nick Centera's topic in Film Stocks & Processing
What Chris says is true but I seem to remember from my days when I worked at Kodak that each roll had what was called a 'customer allowance'; that is an additional length of film that allowed for lacing up. It was also to emilinate handling marks etc on the front and end of rolls. I think that this was 10ft. It might be that this was only on film wound on camera spools. You could tell by checking the edge numbers on a roll of exposed film. I will try to rmember to do this when I am next in the lab. Brian -
Achieving infrared look for 35mm stock
Brian Pritchard replied to joaquin del paso's topic in Film Stocks & Processing
The main problem in achieving an infra-red look is that fact that panchromatic films and infra-red films see the scene differently. Panchromatic films have their sensitivity to colour adjusted so that a black and white image shows all of the colours with their 'correct' density; that is colours that are dark to the eye such as reds appear dark and colours that appear light to the eye such as yellow, appear light. Many years ago when colour was not in common use cameramen went round with a pan glass around their neck. This was a dark green filter which when you looked through it you could get an idea of how the scene would look in black and white. Infra-red stock is recording the way the scenes reflect or absorb infra-red light. For example leaves reflect infra-red strongly so that they will look white in the print. You could get something of this result by using a green filter on the camera but this would distort the rendition of other colours; reds and blues would look dark. As I mentioned the tonal reproduction would entirely depend on the infra-red reflectivity of the objects in the scene. The only slightly helpful suggestion I can make is to try various colour filters and see what the result is. Incidentally around the time of the Vietnam war Kodak produced Infra-red Ektachrome. The layer that produced the cyan dye was sensitive to infra-red. This meant that if you photographed the jungle any camouflage that was not made out of trees stood out as magenta while fabrics that were green and brown stayed their normal colour. It was used by directors who wanted psychedelic colour and produced some fantastic results. Brian -
Buying film off Ebay, risky business?
Brian Pritchard replied to Ron Flex's topic in Film Stocks & Processing
If you have no luck with Film Lab North then try Film & Photo in Acton 0208 992 0037, info@film-photo.co.uk. If you come in on a Tuesday you might be unlucky enough to meet me!!! Brian -
I would hope that the fog levels had not risen by more than 0.05, I would not use the stock if the fog levels had increased by 0.10. This assumes that you know what the fog level was when the film was put into storage. The Kodak website gives average characteristic curves for all their stocks. You could get an estimate of the rough values for fresh stock from them. Vision 2 200T stock has fog levels around R:0.15, G: 0.45 and B:0.95. You could experience problems if the cans had been opened before freezing and sealed up in high humidity. If the film is unopened it would have been sealed at the Kodak factory at the correct humidity. You must remember to allow the film to warm up before opening otherwise you will get condensation on the film. Brian
-
Soviet A2 35mm Black and White
Brian Pritchard replied to Michael Rossetti's topic in Film Stocks & Processing
There is some information at this website: http://www.geocities.com/russiancamera/sve.../svema-film.htm Any Black and White lab should be able to process it; they would have to run gamma tests to get the correct development time but that should not be a problem. Brian -
Hi James I have put the three images on a file sharing site. I have also included a positive image of the B/W lady that has been duped so many times over the years it is no longer recognisable. I make a point of photographing or scanning anything unusual in the film world as I move about. I have quite a big selection of odd colour processes, perfs and so on. these are the URLS: http://www.4shared.com/file/61582269/d7545...dy_test_BW.html http://www.4shared.com/file/61582277/29f745b5/Lady.html http://www.4shared.com/file/61582280/300bc...China_Lady.html http://www.4shared.com/file/61582281/470cfc4f/Kodak_LAD.html Brian
-
You are right Marc, all Orwo stocks do have an anti-halation undercoat, and it does serve the same purpose as the rem-jet backing used on Kodak colour and Fuji colour negative stocks. The advantage is that it does not have to be removed during processing, the disadvantage is that unlike the rem-jet backing it does not given protection against base scratching and static although this is not quite so important in B/W printing. Brian
-
Marc All prints made on an optical printer, 1:1, blow-up or reduction, have higher contrast than a contact prints. This is due to a number of factors including the fact that the light on an optical printer is more specular which produces higher contrast. Flare also comes into it. One of the advantages of working with B/W is that you can adjust the process to alter the contrast so by processing the positive faster you can lower the contrast. You can also flash the print stock; this is the way you could reduce contrast when working with colour where you cannot control the contrast with processing. Unfortunately all these things are expensive and time-consuming so labs are not too keen to do them unless you are prepared tp pay a premium. Brian
-
Actually all B/W print stocks are blue sensitive and not orthochromatic (blue and green sensitive), the only orthochromatic stocks of recent years have been sound recording films. Orwo duplicating positive is panchromatic unlike Kodak which is blue sensitive. B/W prints and colour prints made for cinema projection are normally produced to the same gamma. Problems arise when printing colour neg onto B/W pos stock because it is only blue sensitive and you are only printing the yellow layer which is the grainiest and highest contrast. Many years ago Ilford made a panchromatic print stock to avoid this problem. In those days releases were made in colour and also B/W for the cinemas that could not afford to pay for colour. Brian
-
A LAD film is a piece of correctly exposed and processed negative that is used by a laboratory to set-up their analysers and to ensure that the duplication and printing processes are correct. There are three grey patches to represent white , black and grey. The stock manufacturers publish Red, Green and Blue densities to aim for when printing. For example the figures for Agfa CP30 for the grey patch are 1.15 Red, 1.05 Green and 1.05 Blue. Kodak publish figures for LAD densities for interpositive and duplicate negative. The laboratory will adjust their printer settings so that when the LAD negative is printed it will produce an Interpositive with the correct densities and when that is printed, the duplicate negative will have the correct densities. LAD makes sure that you will get the best possible result from duplicating. It is also a great aid to setting your printer to get the right colour balance on your print stock. You make a print using the LAD negative, measure the grey patch and calculate the difference from the LAD densities and this will tell you how much to alter the trims to get the print correct. Every printer point will change the print density by 0.07. So if the Red density was 1.22 then you would have to reduce the Red light by 1 point. If my memory serves me correctly the LAD was invented by John Pytak. Brian
-
Perhaps an automatic printer was used that has integrated your negative to grey. If the picture is dominated by a yellow flower it will correct and make the colour balance bluer hence making the background blue. Brian
-
Fuji reala 500D backing removal problem
Brian Pritchard replied to Dilon de Silva's topic in Film Stocks & Processing
If the problem is non-removal of the backing then you should be able to remove any backing residue on the base side by hand cleaning with Perklone. If there is backing on the emulsion side and perklone does not remove it, then you can try removing the backing with silver polish (polish used for cleaning silverware) followed by a re-wash to get rid of the marks made by the silver polish. It is not easy to do and you have to be very careful. I did this for a 200ft roll of 35mm negative a couple of weeks ago. I would not recommend trying to soak the film in warm water and borax and then rubbing it with a cloth. You would undoubtedly damage the film and it would be almost impossible to dry the film without water marks. If you are lucky then putting the film back through the process as Dirk suggests should remove the backing; if not then try the above although you need access to a rewash process. Brian