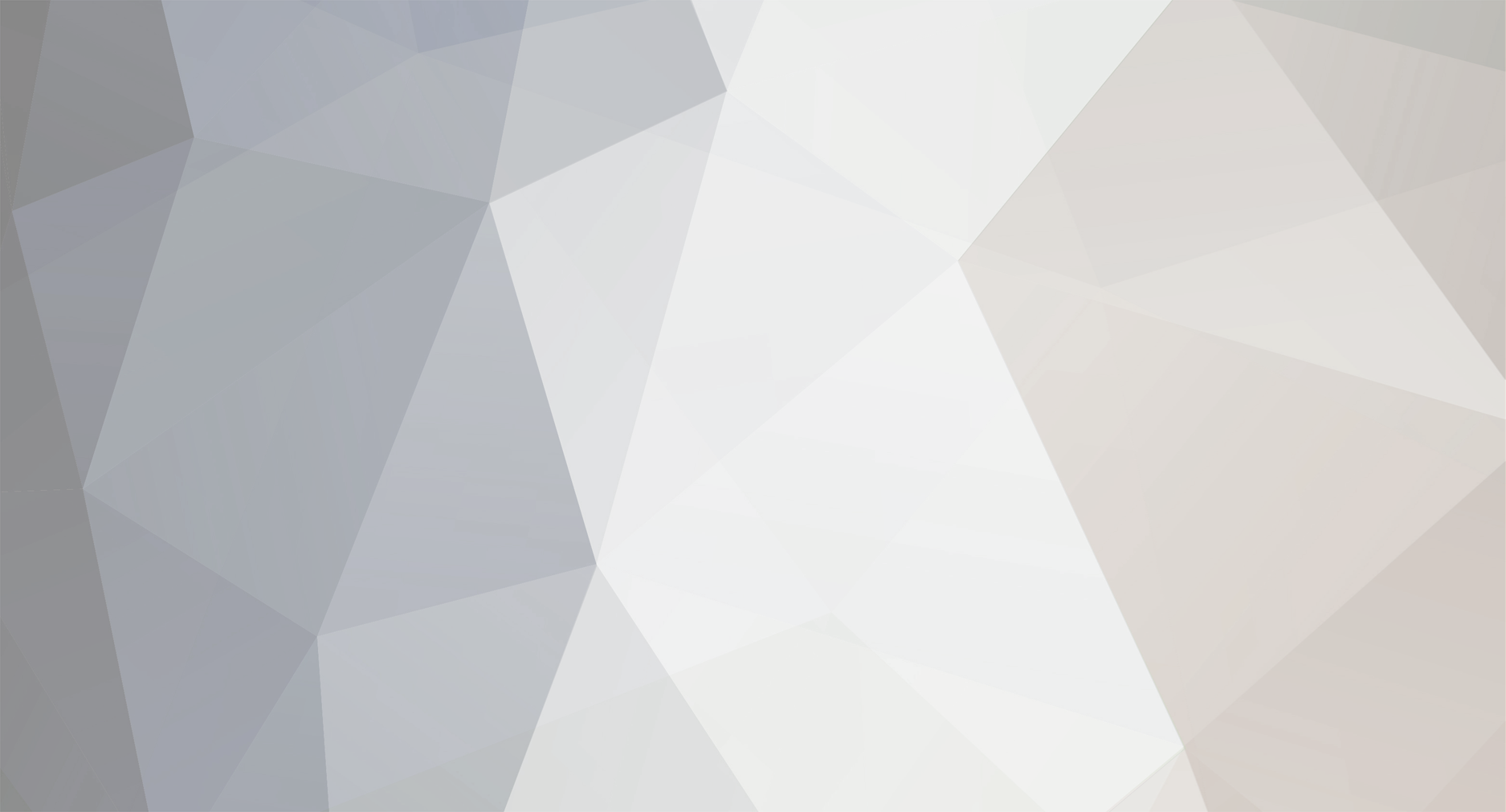
Marc Roessler
Basic Member-
Posts
283 -
Joined
-
Last visited
Profile Information
-
Occupation
Other
-
Location
Southern Germany
Recent Profile Visitors
-
Schwerthelm Ziehfreund started following Marc Roessler
-
FS: S16 Zeiss Superspeed Mk2 Set of 5
Marc Roessler replied to Marc Roessler's topic in Cine Marketplace
Reducing Price to 11.000 EUR. -
sold.
-
FS: Chrosziel Follow Focus for 15mm rods
Marc Roessler replied to Marc Roessler's topic in Cine Marketplace
sold. -
FS: S16 Zeiss Superspeed Mk2 Set of 5
Marc Roessler replied to Marc Roessler's topic in Cine Marketplace
Reducing price to 12.000 EUR. I noticed the 16mm lens has developed quite stiff focus throw (manageable, but not nice) and probably needs servicing. Oh, and, yes, Gregg is right: these are Mk III, not Mk II. -
FS: Chrosziel Follow Focus for 15mm rods
Marc Roessler replied to Marc Roessler's topic in Cine Marketplace
Reducing price to 450 EUR. -
Reducing Price to 10.000 EUR. I should point out (some sellers have asked this) that the camera hasn't been serviced for about at least 15 years. That's about how long I've owned it. It runs nicely, but for ensuring it continues to do so, I'd strongly suggest having it fully serviced, for example at cinefacilities (they seem to do great work). Since I've only used this for private projects (no company here), sale is a private sale, i.e. I can't list VAT/MWst explicitly. That's also the reason why it makes sense to have the camera sent to being serviced not by me, but by the buyer: tax reasons!
-
However, ironically, I ran into a "sticky focus" issue on another unit: on a Quartzcolor/Rank Strand Castor 2kW fresnel. There, the focus is hard to turn, it seems the grease got too gummy. The grease is a silvery/grey paste that can only be cleaned using break cleaner, not using rubbing alcohol. The grease is on the guide rails and on the pulley. Same question here: does this grease belong in this place in this unit? What grease to use to renew this?
-
Some Updates. The "corkscrew" looks fine, the grease is still smooth and does not stick. The actual problem turned out to be the slide tilting sidewards and then binding to the guide rails (top and bottom in the attached picture). In the picture, you can see the slide already is at a slight angle, not perpendicular to the guide rails. This is it enough for it to bind. I took out the (already quite clean) guide bards and slightly polished them using a cloth (there wasn't any grease grease on them). This improved things, but a slighty "bindy" feeling is still there. I'd say this unless the slide is worn in a strange but subtle way (no easy way to check...), this seems to be somewhat of a design issue. If you have Mizars with similar/without problems, let me know, would be interesting to know.
-
Hey guys, I own an older, small Quartzcolor/Ianiro/Rank Strand tungsten fresnel unit (Type "Mizar", 300 to 500 Watts). It has a little problem: the focus adjustment is jerky and tends to bind, especially once it gets hot. The focus gears seem rather crude, you can see them here in the second image (not my unit, but same model): https://www.tuttofoto.com/ianiro-minispot-mizar-500-8982645+d-37171--it.html Any suggestions how I can restore this to full working condition? I'd especially be interested in suggestions around which (high temperature) grease to use - preferrably something commonly used in the automotive sector. (Obviously, neither petroleum jelly nor WD40 are an option...) Best, Marc
-
This a somewhat film-archeological topic... Over the years, I've seen all kinds of sync ups, especially for 16mm. In their Beatles docu, the Maysles hit the microphone with a card for marking audio. In other documentaries, I've heard different electronically generated bloops, often with very noticeable warble (not sure where that came from .. the rest of the track seemed OK). Then there's this strange horn like audio mark in the casting footage for Rebel without a cause, along with a mechanical-counter-like ID screen apparently shifted in while the camera was rolling: https://www.youtube.com/watch?v=XVDzlZcQe1w I'd also be interested in hearing some details about these. But the most interesting one surely has been from Scorsese's Italianamerican (1974), right at the beginning of the film. https://www.youtube.com/watch?v=pcWUNfmf0tI A photo flash bulb and a distinctive, brief beep with sharply rising frequency (sounds like a starving oscillator). Does anyone happen to know what kind of contraption that was? Custom/home made, or was this widely used? Is there a specific reason for that style of bloop, or was that just a side effect of used oscillator?
-
Sorry, already sold.
-
FS: S16 Zeiss Superspeed Mk2 Set of 5
Marc Roessler replied to Marc Roessler's topic in Cine Marketplace
9,5 mm 12 mm 16 mm 25 mm 50 mm So, the usual S16 set, as it seems -
Available again, for now.
-
Reserved.
-
Chrosziel Follow Focus for 15mm rods. Dual sided, with extra set of white marking discs. Comes with extension lever, metal transport case, two sets of lens gears. Works fine, minimal play, less than 1mm at the outer end of the extension lever (at end of black ball) when holding the lens gears fixed. More images on request. 650 Eur