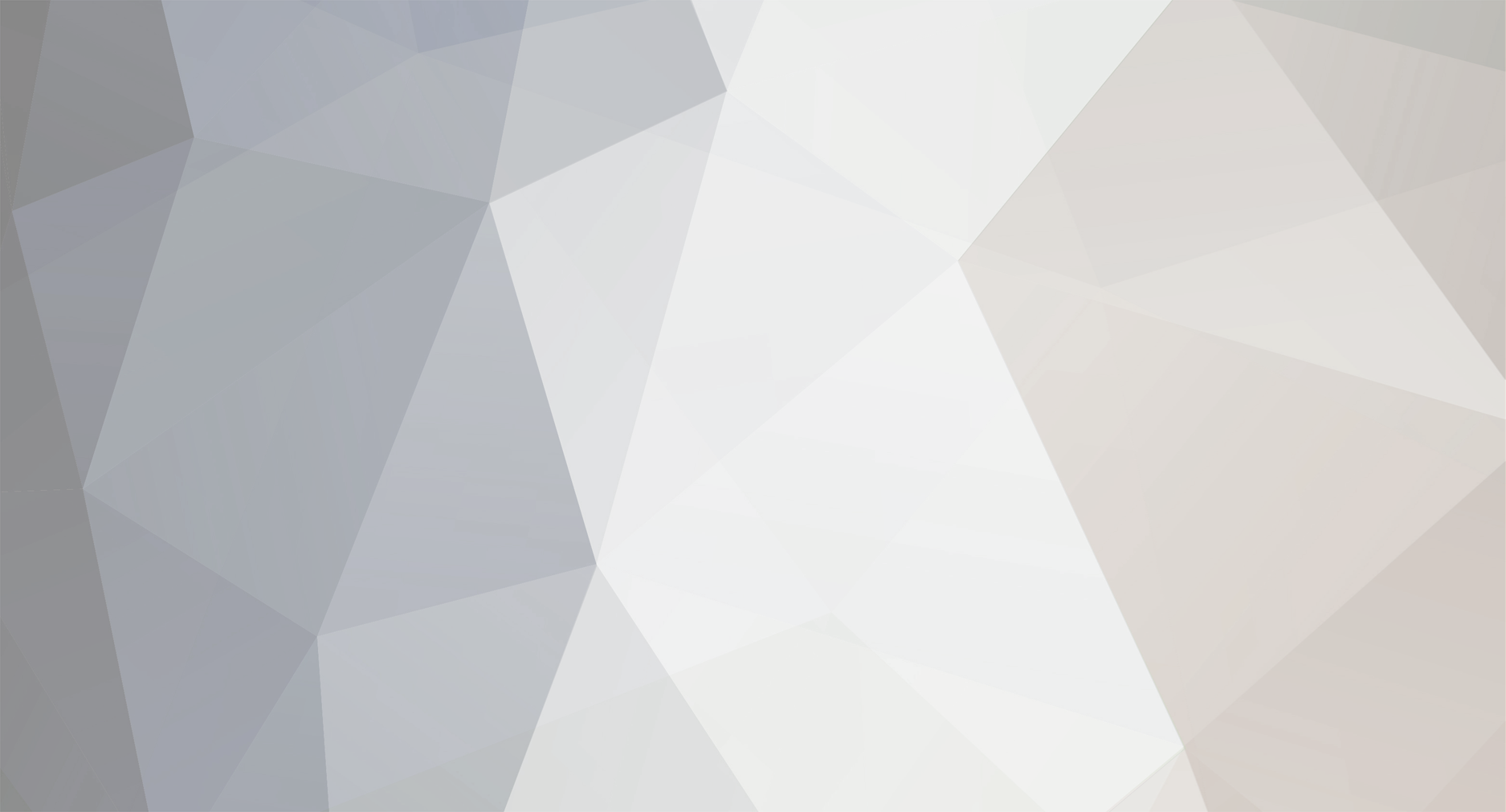
Mike Hall
Basic Member-
Posts
37 -
Joined
-
Last visited
Profile Information
-
Occupation
Gaffer
Recent Profile Visitors
1,956 profile views
-
Dana Dolly Maintenance
Mike Hall replied to Dustin Bloodgood's topic in Accessories (Deprecated SubForum)
Hi Dustin, it's Mike from the Dana Dolly. We use sealed bearings with a heavy grease that should last for a long time, so the bearings probably shouldn't need anything sprayed on them. If you want to use something, probably either a Silicone Grease (tube not spray) or 3in1 oil is best, I would stay away from drying agents like WD40 and basically, as a rule, Never use Silicone spray on dollies of any kind. Eventually it starts to give a coating on the pipe that will squeak, and that goes for dollies all the way up to Fishers. Good on stands, not on dollies. The fasteners are Stainless, Nylon, and Aluminum, so they shouldn't rust. I use Pledge spray with a rag on the rails if they get dusty (I live in Arizona, everything gets dusty). We sometimes have people that use baby powder on the wheels, and if that cakes up, I usually take all the wheels apart (bearings and spacers out) and wash them with Dawn dish wash. I hope this helps, if you do develop a squeak (like if a customer uses Silicone Spray on the wheels and it dries the bearings), you can send us the triangles and we'll take apart the wheels and replace the bearings for a charge, email us for whatever that is currently, or if you have any questions, we're happy to help. You can also use regular ABEC 7 or 9 skateboard bearings, however you'll find that they have a lot more play than the ones we have made. Thanks very much, Mike Hall www.danadolly.com- 3 replies
-
- dana dolly
- dolly
-
(and 3 more)
Tagged with:
-
I agree with the rental idea. Sometimes you get a situation where the proper equipment is just too expensive to make or buy, but for safety reasons (and to get the shot quickly) you need proper gear. First, be careful with suction cups on the fiberglass. Sometimes it's porous, and with the vibration the cups can come off. Use a little water under the suction cups (but don't use too much and get the felt wet underneath the cup). Use at least four cups for redundancy. Second, try and find a hard point on the car to go to. Not something that moves, like the front bumper, rather something to the frame. Also, remember that even at 15mph, the camera is going to experience G force pull in the opposite direction to the turn. A 10 pound camera will experience 30 pounds of pull in tight turns, so make sure the camera mount is strong side to side as well as front to back. If you still just want to make the rig yourself, in the old days we would use 2x6 wood studs to do this rig. Cut the studs so that they fit snug on the front of the cart. Leave a space for the camera plate to be screwed to the studs. Screw the plate onto the studs, then ratchet strap everything down. Make sure you put some fabric or a towel underneath the studs between the fiberglass to protect the cart. Don't use gaffers tape. Use paper tape or painting tape on the rig so you don't pull up the finish on the car. Fasten a couple of baby plates to the studs, and a pin to the camera, and use baby c stand arms to stop camera sway, like an A frame, one from each side. Hope this helps, M
-
-
You may want to look at Premier Studio Systems dollies: http://www.premierstudioequipment.com/Products/Dollies.html We own two of them, and they have held up nice. And the price - From $5000 to $27,000 for a pneumatic crab dolly - is unmatched anywhere as far as I know. I don't work for them, but we do own two of their dollies and I've been very happy with them for the past few years. Not a problem. M
-
There are a couple of kits available on Ebay, search "camera dollies". Or, just get some plywood and angle iron and skateboard wheels and make one up. If you just need 10 feet of track, consider using metal conduit instead of PVC for track. You can keep the track spaced with sandbags if needed. Is also another idea for a dolly that isn't on the ground. If you want to make your own ground dolly, here's a good instructional video: If you make a ground based dolly, you will want to use at least 85 hardness wheels, and stagger the holes a bit to make it a little smoother. There are also some good tips to making your own dolly from an old pro here: http://www.rondexter.com/ Ron Dexter ASC made some of the earliest skateboard dollies. He has a good web page of tips for the upcoming do it yourself cinematographer. He is very good at sharing his information and experience like David Mullen ASC, the two are a credit to the craft and will always be a benefit to the industry. Disclosure: I work for the company that makes the Dana Dolly, and I have made a ton of skateboard dollies over the years.
-
As a small rental house, I have mixed emotions about these: Love the price, since the units look capable, I am not concerned with their safety, however I don't think I would purchase them right now. I've just bought a couple of Sunrays, and they come with terrific customer service, and, yes, a big "made in America" flag on them. And, as far as HMI's go, they are realatively inexpensive. If the Chinese units were to catch on at a terribly lower price, I, with so many others, would have no choice but to go with the more competitive option.
-
Since St. Patty's day is opon us, and our Irish Friend has seen fit to call me out, I would like to reiterate my opinion that this is the "outside" edge of where a 12x12 can be flown safely, tabled, or with the wind, by two men. If need be, you have two qualified blokes of 200lbs or more that can handle a little wind, and a 12x12 butterfly in good condition that is tabled(or with) to the wind, I would bet a pint of guiness to all involved in the Tullamore Country Club that I could execute flying it safely and without harm in Beaufort 5 wind any butterfly that can be arranged. I would also hasten to add that there is an extreme difference in the US between "Force" five and "Beaufort" force five, and one might examine the difference before hastening to judgement. I do not know if this is the same in Ireland, however, a 12x12 in a BF 5 wind would still be the dog's bollux. I heart Ireland. Mike Hall Glendale, USA
-
I'm not exactly an expert on the subject, but I can recommend a couple of things that may be helpful from my experience: 1) - Hard light is your friend. Let the shadows be crisp, and yes, shadows occur in nature. Single source (or really good divided lights) broken up with some sort of non-discernable pattern - and fill, that's for the other guys. Let the Kodak decide how much fill there is. 2) - Shadows spark the imagination. Let the talent play into the dark...the viewer's mind will fill in the blanks with their personal worst fears. Shadows envoke a personalized experience when used correctly. 3) - Make something look "good". Some of the film has to look "normal" to standardize the experience, and so the viewer can tell when everything goes to hell. Soft lights, soft tones. 4) - Use soft sources at first, harder lights as the action builds to a climax, and break some rules when it does. Build the story visually, from a friendly look (soft) to a most disconcerting look (really hard) when all hell breaks loose. If you have diffusion on a light, or if there is a light within 25 degrees behind the camera when you are shooting your climax, there may be something out of place. 5) - If you are filming a dark scene during the day, take the light away. Negative fill is a term used for taking the daylight fill away from the talent on the non-sun side and some of the top. It can make for a very spooky look even in cloudy conditions when done right. Make everything on the "fill" side of the frame as black as possible, and play the stop a little hot to the key. Make sure to take out some of the top light from the atmosphere bounce. Just my opinion, I could be wrong.
-
I think one of the best places to find ideas for home made rigs, and basic film advice is from Ron Dexter's website: http://www.rondexter.com/ Like David Mullen here, Ron Dexter took a lot of time out to help others in the industry, and showed great selflessness and generosity throughout his career, and our industry as a whole is better of because of them.
-
A couple of things should probably govern your use of a 12x12 in wind: The competence of your crew people, especially your Key Grip. If you have a good key grip, he or she will be able to tell you if flying the 12x12 is a good idea given the conditions; that is, factoring in the shot, available manpower, equipment, time, and location constraints. Since I have read in another forum here that some grips are earning $150/day, I would hasten to add that I would take the advise of a seasoned Grip first. It's my experience that persons new to the grip field may overestimate the ability of the equipment to withstand wind. If you are in a position to estimate the safety of a 12x12 completely off the cuff, I would recommend that a wind of no more than Beaufort number 5 (Fresh breeze, wind of 19-24mph) in sailing terms be considered. At that windspeed, two grown men of 225lbs should be able to safely handle a 12x12 bagged on high rollers if it is constantly held and "with" the wind.
-
Frank, these posts all have good ideas for grips, and John Hall's post seems to me geared more toward rigging grips. In my opinion, every grip should bring to the set a tool belt with the basic tools (tape measure, gloves, leatherman, multi screwdriver, crescent, sharpie, hex set, and a small driver with 3/16" hex head in it for fittings, knife) and a cordless screw gun. Most I've worked with also bring a hand truck with the other tools and safety equipment in a toolbox so they are available to them without weighting them down. I was a key grip for some time, and I would probably take exception with the need for hammers to be carried on today's sets. Years ago we used to nail everything together; today it's mostly screws. I would much rather see someone show up with a full set of cordless tools (especially screw gun and saw),a crescent, a leatherman, and a hand truck than weighted down with a lot of tools. Just my opinion, but since we seem to be doing "more with less" these days, I would rather see a crew that has a few labor (and time) saving tools. A combination of John and Rik's posts is probably the perfect basic grip kit, with the addition of a hand truck.
-
I don't think you'll have any problem with one. However, if you are going to make a couple of these up as a kit, you will more than likely have to try several bulbs to get say, three to match closely. Most industrial bulbs are not matched for color in the mfg. process. There is the usage question: if you are just going to use this one lighting something inanimate, probably not a bad idea. However, if you are planning on taking one or more around and using them on people, then you may want to think twice. If, for whatever reason, something goes horribly wrong, and you have to tell a judge (or an insurance inspector) that you just made the light at home because it sounded like a cheap alternative to HMI's and you never thought it would blow up and harm someone, things could get expensive anyway. I think I would look for an industrial light that is meant to be transported, and go from there. More than likely if there is something that can go horribly wrong with the fixture they will either warn about it on a label, or have a way to prevent the lamp from working unsafely (like micro-switches on HMI's). Anyway, a couple of devil's advocate thoughts. "It's all fun and games 'till somebody loses an eye; then "sorry" is just not enough".
-
The farther from the element, the better. Most gels are formulated to take the heat of a fresnel. That said, an open faced light generates five times the heat (at the hot spots) of a fresnel, and you will have burn-thru. There are no gels that can surpass the heat of a bare tungsten bulb, so the rule of thumb is: the farther from the source (bulb) the better. If you must use a color very close to an open bulb, it is best to use a glass filter. Otherwise, back it off at least until it fills the barn doors.
-
American Insulated Wire makes a really good stinger, and they have 10/3 in black, outdoor, flexible when cold. thier website is: http://www.aiwc.com/ to locate a dealer near you. There is also a company that will take these stingers, and imprint your company name in them for what amounts to $6/stinger. hope this helps, Mike Hall Glendale, AZ
-
Does anyone know of a commercially available butterfly that has more transmission than a half soft frost? I'm starting to find that my HSF takes too much light off the subject for AZ daylight with HD cameras. I do not want to go with a silk or fabric, as they seem too "hard" to me, like a quarter silk or so. What I really want is something the quality of Hampshire frost. I would rather not use visqueen, although that would work. If you know of something, I would appreciate the input. I'm probably going to call Norms or Modern tomorrow and ask, and I would like a starting point. Thanks in advance, Mike Hall Glendale, AZ