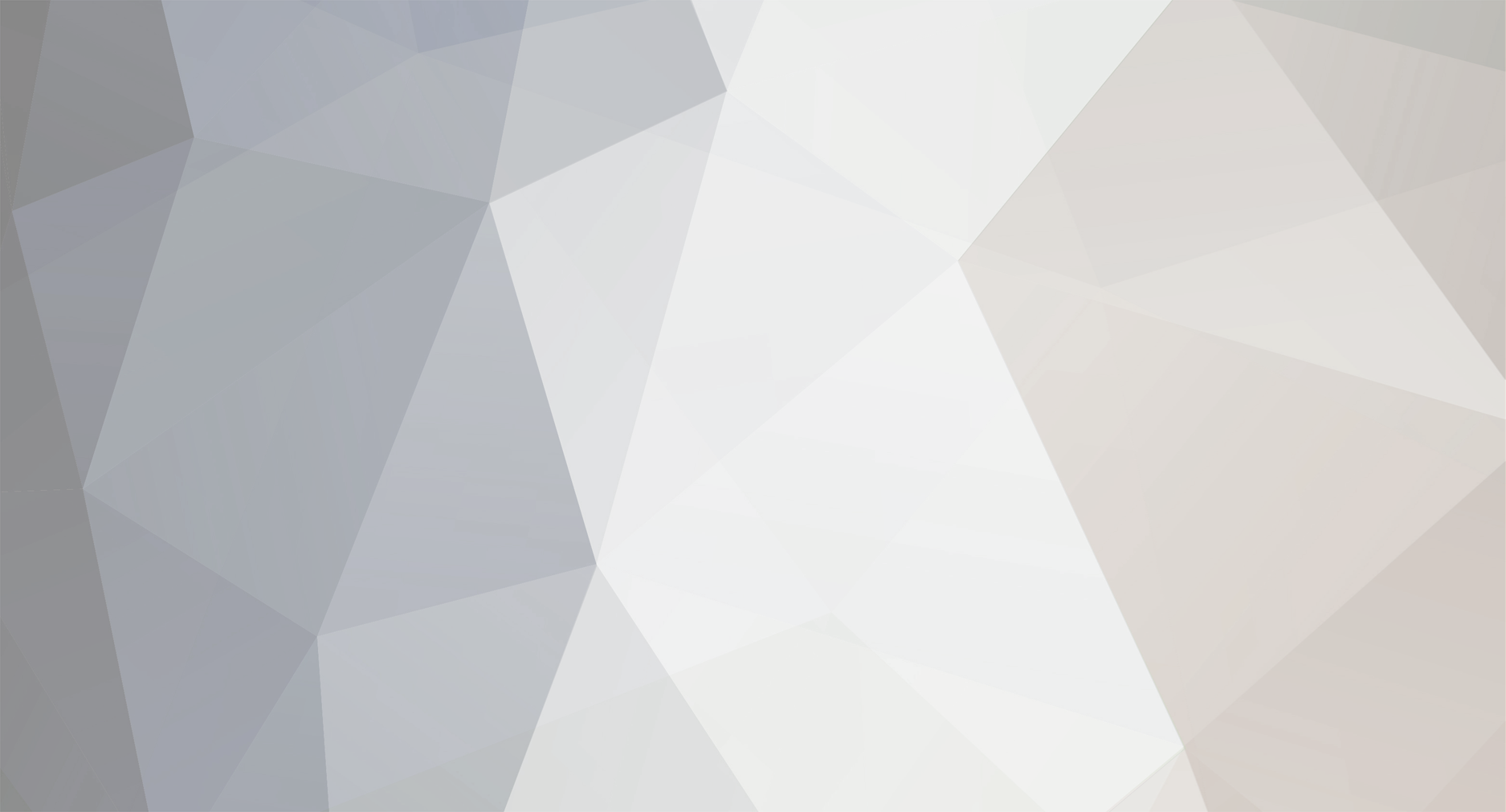
Gregg MacPherson
Premium Member-
Posts
2,628 -
Joined
-
Last visited
Everything posted by Gregg MacPherson
-
Eclair Flea Market
Gregg MacPherson replied to Gregg MacPherson's topic in Marketplace Listings Under $200 / €200
FS: Eclair NPR Super 16mm Camera Package. See Samuel Adeiza's post May 16, 2020 in Cine Marketplace https://cinematography.com/index.php?/forums/topic/83794-fs-eclair-npr-super-16mm-camera-package/ Still for sale SOLD SOLD SOLD SOLD SOLD SOLD SOLD SOLD SOLD SOLD SOLD -
Just to be clear, I never got a sense of reluctance from Paul. I think he likes ACLs and likes working on them. But he works for VP, and they make more money selling and servicing Arri/Aaton, so he has to follow that theme.
-
Hey Raymond, You bring up some important ideas and things to clarify... Many, maybe most of these camera techs are busy and keeping up with correspondence takes time. So I think we need to be patient and strateigic in how we try to communicate with them. Be imediately clear on what you want from them. Limit the number of emails or calls, be super organized, write well, be breif unless they invite detail. And then, as Heikki says, there's timing and luck.... And then, Gregg says, our own particular experience may be misinterpreted as a general principal.... The DU-ALL info I just took from their website. I think, just like Paul at Visual Products (VP), parts could cause serious delay in an overhaul that brought up some repairs. Raymond, if you know or find out the name(s) of the tech(s) at DU-ALL actually doing the work on Eclairs can you let us know, we will update our list. There's only one guy in the states that we know works on the ACL motor electronics, Andrew at AZSpectrum. If DU-ALL used to service motors this would be useful to know. Paul at VP confirmed on 25th/March/2022 that "Both (he) and Andrzej at AZ-Spectrum will work on Eclair bits up to & including conversions however (it will) always come behind equipment sales and can unfortunately sit on the shelf for months before completion." I pasted a summary here...scroll about half way down... https://cinematography.com/index.php?/forums/topic/87469-technicians-who-service-eclair-acls/page/2/#comments It's perplexing how DU-ALL might be unaware of Paul at VP. Maybe Heikki's right again...competitive feelings or giggery pokery between repair houses. Ditto for the Bernie thing. I've had chats with a client of plural techs who extoled one and derided another, then a kind of reverse story from someone else. The parts drawings are super useful for camera service techs. There are links to them in one of the pinned threads on the Eclair sub-form. DU-AlL will have them, unless they don't need them. Point him to the link. Gregg.
-
Eclair NPR newbie questions (with pictures!)
Gregg MacPherson replied to Duncan Brown's topic in Eclair
Hey Duncan. I had you pegged as prob'ly NSFRTFM. The rounded corners frame looks like the TV safe area, the area assumed to be received on the goggle box. Visual products have a nice picture with definitions... - projected area - transmitted area - "safe TV action" area on the receiving TV. https://visualproducts.com/equipment-for-sale/s16-16mm-cameras/ scroll down... It's a big crop to TV safe, especially when you think of the lower resolution film stock back in the day. - -
I don't have the electronics knowledge to enjoy Duncan's free fall down the rabbit hole...I can remember how to spell Kirchoff (no, he cant). Great photos D, very trippy... This issue about which motors are/are not crystal controlled at non sound speeds came up in messages recently. I did notice this in the French ACL 1.5 user manual, which shows the MIVAR motor, with mirror parking icon, exposed inching knob without a protective ring shape around it. "Motor: 12 volts multiduty type, brushless, Hall effect, 6 crystal controlled speeds 8, 12, 24, 25 50, 75 frames per second. Automatic stop in viewing position..." Heikki, was crystal control at all speeds not extant before MIVAR? Was there a definitive source on that point? Duncan, is "Hall effect" just referring to the physics used for motor position sensing? Don't distract yourself with a lengthly answer. Cheers.
-
Eclair ACL English 400'magazines (two).
Gregg MacPherson replied to Gregg MacPherson's topic in Cine Marketplace
I haven't personally seen it done. That idea came from Bruce at Arranda so I gave it some credibility. Even so, it seems a better idea to use converted mags. There are still contact surfaces in a converted mag, but at least all that reasonably can be modified is done..Heikki's example is an interesting one... What did you break on your mag? Can you just get it fixed at DU-ALL..? I don't know why it would run more quiet after S16 mod...Any ideas anyone? Cheers. -
Eclair Flea Market
Gregg MacPherson replied to Gregg MacPherson's topic in Marketplace Listings Under $200 / €200
Hopefully, if someone is hoarding the Arts Media parts, they did not also get the IP, copyrights. Even if they did, there are probably more willing lawyers in Paris, Texas than Paris, France (hyperbole..). Speaking of copyright, I panicked when I realized I had just pasted a bunch of links with formatting from Cameras Eclair, so wrote a nice email to Erkan Umut, asking about it. Got an even nicer email back..."..No worries, all copyleft..." Laughter. -
Eclair Flea Market
Gregg MacPherson replied to Gregg MacPherson's topic in Marketplace Listings Under $200 / €200
Thanks Ruben, I missed that. I made a correction to my post. Figuring out some editing and formatting quirks. I'm quite interested in that casting process so I'll enquire about it. The Flea Market seems a good place to notify about these items. Selling small runs to replace very rare old parts, I don't know if Tim Tyler would consider you in the commercial category. You could ask him. I would have added small pics of those items but ran out of time. Gregg. -
Eclair Flea Market
Gregg MacPherson replied to Gregg MacPherson's topic in Marketplace Listings Under $200 / €200
A couple of useful items on eBay Eclair ACL Magazine Throat Cover. ...USD50....made out of flexible polyurethane casting resin Eclair ACL 1.5 & 2 camera aperture and gate protection plate. (3D printed)...USD25 Eclair ACL. Body and Angenieux viewfinder caps. (1 of each...USD40 -
Eclair Flea Market
Gregg MacPherson replied to Gregg MacPherson's topic in Marketplace Listings Under $200 / €200
Eclair ACL English 400'magazines USD300 each. Shipping one to US...USD75, to UK/Europe...USD67 Two English 400'magazines. Cosmetically a bit scruffy. Fully disassembled, cleaned and lubed except for feed and take up spindles. New drive sprocket bearings and rubber take up tyres. No plastic pressure plate covers. This is the mag that Eclair designed for the ACL I, which had the small Tomson motor. This camera/motor/mag combination is designed to not overload. I shot a lot of film this exact way in the 80s. The mag draws less amps than the french mag. I tested the current draw after the lube and it was on par with a 200' mag English 400' mags run fine on any ACL...(more info, and details on the overhaul in the listing on cinemarketplace) https://cinematography.com/index.php?/forums/topic/91105-eclair-acl-english-400magazines-two/ Learn more about English 400' mags here... https://cinematography.com/index.php?/forums/topic/91664-english-acl-400-mags-facts-and-myths/ SOLD SOLD SOLD SOLD SOLD SOLD SOLD SOLD SOLD SOLD SOLD These mags were bought on eBay by Chapin in Hawaii. Sounds like he has an ACL I that he loans out to students and new people, so they went to a good home. Hope he may join the forum. He also has an ACL II. -
Eclair Flea Market
Gregg MacPherson replied to Gregg MacPherson's topic in Marketplace Listings Under $200 / €200
ACL II Factory Top Handle What can I say...it's not red. Can't see the front pin in the photo, it's slightly shorter, but it's there. USD70, and counting down maybe. Shipping don't know yet, just ask. -
Eclair Flea Market Concepts Looking at the high volume of traffic on Cine Marketplace sub-forum, noticing how quickly items disappear downstream... I thought we could have a single Flea Market thread on Eclair, where sellers make a post (reply) rather than a thread for each item. One could also advertise like normal on the Marketplace and have links connecting Flea Market and Marketplace, both ways. I don't think this qualifies as "double posting". Google search engine yields links to the Marketplace, ranked at or near the top of the page, but not Flea Market, however the later can still be valuable. Having an Eclair Flea Market will give us a historical summary of Eclair stuff being sold, and help retain contacts. Any thoughts? Let us know...Maybe I just give it a whirl...
-
Useful links for Eclair NPR, Cameflex, etc...(not ACL) Having trouble with the formatting but will figure it out. Custom crystal motors for Cameflex https://cinematography.com/index.php?/forums/topic/83517-custom-crystal-motors-for-cameflex/ Eclair Flea Market https://cinematography.com/index.php?/forums/topic/91893-eclair-flea-market/ Changing the shutter angle on an Eclair NPR... https://cinematography.com/index.php?/forums/topic/91141-changing-the-shutter-angle-on-an-eclair-npr/ Please suggest other links in your replies below, discuss, debate. I will copy useful links to the list above. Hopefully, replies keep on topic, but human nature is what it is ? Gregg Eclair Moderator. PM: top right of page Email: viz(at)xtra.co.nz Telefunk: sixtyfour274 377 086
-
Hi Erkan,
I pasted a link on the cinematography.com forum to the Cameras Eclair website, and the links to the ACL manuals and parts lists. See here.. https://cinematography.com/index.php?/forums/topic/91878-useful-links-for-eclair-acl-from-elsewhere/
OK..? If you have any comments or concerns re copyright please reply with a short explanation. We can always find another way. The documents themselves are commonly thought of as in the public domain. I didn't check yet who rented the server space where they sit, maybe you guys.
Keep up the good work for Eclair cameras.This message was also put in the contact/comments on Cameras Eclair.
Gregg.
PS. We may have one or two differences in our technical opinions about ACL I, the small motors, the French vs English 400' magazines. Enjoy this https://cinematography.com/index.php?/forums/topic/91664-english-acl-400-mags-facts-and-myths/ -
This is the earlier 19mm rod version with a machined casting for the base. I thought it would be useful to have 19mm rods to allow stronger, stiffer support for large telephoto lenses, and a very stiff, steady platform to experiment with in camera mattes. And use the rod mount base to allow integrated handles, shoulder pad and battery mounting. Having continuous rods to the rear increases the overall strength. You might see that there is a small conflict with the connector protruding from the base, affecting the rod if it is continuous to the rear as shown. Offsetting the rod position a couple of mm would help, but is unappealing. Rods going only forward is possible if the rod mount is a bit longer. Other workarounds are possible. It should be possible to make the base with a flat plate and some Chinese 19mm rod clamps. Gregg
-
Useful links for Eclair ACL on the forum List of Technicians Who Service ACLs, including potential ones https://cinematography.com/index.php?/forums/topic/87469-technicians-who-service-eclair-acls/page/5/#comment-559268 Eclair Flea Market https://cinematography.com/index.php?/forums/topic/91893-eclair-flea-market/ Boris Belay on Eclair ACL History https://cinematography.com/index.php?/forums/topic/35774-eclair-acl-historyinfo-needed-for-website/ Notes for the new ACL User https://cinematography.com/index.php?/topic/100221-notes-for-the-new-acl-user/ Useful links for Eclair ACL...from elsewhere User manuals and spare parts drawings/docs They are listed on the Cameras Eclair website. Links, with notes on sources, are pasted below. https://eclaircameras.wordpress.com/downloads/ British-made ACL manual [Courtesy of Eric Bickernicks] British-made ACL Parts Catalogue [Courtesy of Nicolas Rey] French-made ACL manual [Courtesy of Rick Lieberman] French-made ACL manual (in French & English language) [Courtesy of Nicolas Rey] French-made ACL spare parts catalogue [Courtesy of Nicolas Rey] French-made ACL LEMO plug connections diagram [Courtesy of Nicolas Rey] French-made ACL hand drawings [Courtesy of Nicolas Rey] SAY YES 2 ANALOG website by Erkan Umut (Istanbul, Turkey) has lots of useful info on ACLs. https://sayyes2analog.wordpress.com/2015/01/23/eclair-acl/ Please suggest other links in your replies below, discuss, debate. I will copy useful links to the list above. Hopefully, replies keep on topic, but human nature is what it is ? Gregg Eclair Moderator. PM: top right of page Email: viz(at)xtra.co.nz Telefunk: sixtyfour274 377 086
-
Save other interesting links to the Eclair forum As well as the short lists of links in the two pinned topics above, we can save links here to anything interesting. I didn't yet search back very far. Make suggestions and I can add to or edit the list below. new ALCS crystal sync motor for Eclair ACL https://cinematography.com/index.php?/forums/topic/93357-new-alcs-crystal-sync-motor-for-eclair-acl/ NPR crystal motor by ALCS (Aapo may make a new Xtal NPR motor) https://cinematography.com/index.php?/forums/topic/99577-new-eclair-npr-crystal-motor-by-alcs/#comment-580428 Everything you always wanted to know about the MIMUL motor* (*but were afraid to ask) https://cinematography.com/index.php?/forums/topic/91841-everything-you-always-wanted-to-know-about-the-mimul-motor-but-were-afraid-to-ask/ke a new Xtal ke Eclair ACL, sintered bronze bushes lubrication.... https://cinematography.com/index.php?/forums/topic/91741-eclair-acl-sintered-bronze-bushes-lubrication/ English ACL 400' mags. Facts and Myths...(includes some info on servicing) https://cinematography.com/index.php?/forums/topic/91664-english-acl-400-mags-facts-and-myths/ ACL viewfinder - improving hand held ergonomics https://cinematography.com/index.php?/forums/topic/98112-acl-viewfinder-improving-hand-held-ergonomics/ Ideas for ACL integrated rod base, handle mounts, battery mount, shoulder pad mount. https://cinematography.com/index.php?/forums/topic/91574-ideas-for-acl-integrated-rod-base-handle-mounts-battery-mount-shoulder-pad-mount/ Gregg.
-
Potential Camera Techs for ACL Graham Jones...Lemac, Sydney was on the original potentials list but was taken off... I emailed Graham and he replied that he did not service or repair ACL. The last one he saw was 20 years ago. He had no parts or drawings. I offered him the parts drawings (of course)? Gregg.
-
Technicians who service Eclair ACLs...Summary. Short List of Camera Techs for ACL Criteria.... - Expertise as camera techs with Arri/Aaton etc, CLA, repair/rebuild, collimation. - Have some expertise/experience with ACLs. - Confirmed they will accept work on ACLs. UK and Europe Les Bosher ..South Wales, UK. S16 ACL conversions, servicing, custom rod sets, accessories, PL/TS-1 mount adapters for ACL, custom lens mounts. Les' S16 ACL conversions have less features/elements, no ground glass re-etch, but are cheaper. A small boutique business, he and his son. Be patient with contact and turnaround time. Excellent design and machine shop skills on the parts I have seen (Gregg). USA Visual Products...Ohio Paul Scaglione....(drops in to the forum occasionally) S16 ACL conversions, servicing, rebuilds. Paul's S16 conversions are fully featured, including re-etched S16 ground glass. VP is a well established business with a volume of Arri/Aaton work taking priority. Talk or PM with Paul. Be patient on the turnaround time, especially if the job needs a ground glass re-etch (piece work by SHURCO). Alan Gordon Enterprises...LA They used to advertise expertise in ACL and parts. The website advertises service for all film cameras. If someone is in LA can they clarify this. Get the names of any techs there who've worked on ACL. Du-All Camera...NY Service/overhaul of ACL. Website gives good detail on all the cameras they service, including NPR, and prices. Australasia Dom Jaeger...now working as a lens technician at Panavision Melbourne..(a regular on the forum) His expertise is in Arriflex, Movicam and Bolex, but he has worked on many other cameras over the years, including a few Aatons and Eclairs. Things like flange depth, ground glass focus, checking general function and fault-finding mechanical issues, he can help. If we can find good service documents he might consider overhauls, noise reduction, electrical faults (Gregg thinks). I think Dom is quite busy at Panavision, but likes to help, and loves the film cameras. List of Potential Camera Techs for ACL These guys have skills but may not tick all the boxes, or may need further research, or just encouragement. Feel free to do that and report back so we can update. Try not to over tax their patience, especially if they are on the fence, undecided. UK and Europe (potentials) Thanks Heikki, most of these are your discoveries... Simon Wyss...Switzerland...(regular on the forum) Experienced and adaptable with lots of different cameras. Interested in working on ACLs (not on S16 converted ones), but hasn't much familiarity yet. Has repaired an ACL motor but I don't know the details. Boris Belay...Brussels, Belgium...(occasionally on the forum) A real expert on Eclair who has serviced his own ACLs and (I think), also his friends cameras. I don't know if he has professional experience or if he will accept ACL service jobs... Christophe Goulard...Paris. Involved with Re-Voir and L'Abominables. He serviced the ACL 1.5 recently advertised by Steven Jackson on the forum. Heikki reports that he has previously made replacement electronics for the ACL motor. He does not have a formal business, or means of easy contact, so some care is needed in the research. Someone who lives near Paris perhaps, who can make contact personally. Daniil Nevskij...Sweden/Finland Heikki.."(He) modifies Arriflex cameras to 2-perf and services a range of Arriflex cameras for rental houses has told to me that he has previous experience with ACLs (and owns one) but that he doesn't like them because they are "too French". No idea, if he can be asked to service them. Anyway, he's a real wizard. Was previously located in Russia, but now in the Sweden-Finland -axis." https://instagram.com/kamera_doctor?igshid=YmMyMTA2M2Y= Georg Bogner...Germany Heikki..."I asked him about servicing my mags in 2020 and he told me doesn't work on them anymore due to retirement. Germany." http://cameraservice-bogner.de/ Retired guys should not be written off... they sometimes will do it, and their overheads are low... Duncan's Russian ACL motor expert (sorry, I lost the name) Duncan found this chap. He's previously made all new electronics for the latest model ACL motor. Nothing about that on his web pages, just lots of other film camera motor mods. I don't know how well set up he is to take jobs or enquiries. English skills unknown. Google translate worked for me on his web pages. Excuse the nude picture in the top left. Duncan thought there might be a restriction on access to this page, but it opened for me.. http://pouch.narod.ru/ USA (potentials) Conci Nelson... Heikki..."Conci is not a full time technician but has been trained by Bernie (S16 Inc) and is very good with rebuilding ACL magazines" Evan Ferrario ...LA Heikki..."Evan is not a full time technician but does maintenance on the side" Tony...AWcinema....LA?..not sure He posted some ACL camera body tear down videos on Youtube. I didn't agree with everything he said, but he's a very interesting and accessible guy..This contact data may be out of date...323-717-5775 or e mail...at awphoto67@yahoo.com There were originally 3 videos that covered the opening, movement block removal and shutter replacement. On short notice I just found these. So rummage, find and report back please for the update. https://www.youtube.com/watch?v=lgxtOkldh9M https://www.youtube.com/watch?v=an2E3eHYrMs I think I tracked Tony down later, he might have been a drone operator/service specialist. Last point re finding technicians.. Please help find technicians familiar with ACL. You can PM me or Heikki if you need to. You have to keep an open mind. Opportunities come up....for example...maybe five years ago, there were two really skilled techs at Panavision Auckland who might have started looking at ACLs if they had the right nudge. I don't think they are still at Auckland. There was also a tech there who was familiar with repair on ACL electronics... Re updates and errors Please post updates and errors on this thread for now. I will set up a pinned thread, as a directory, with links pointing to useful info like this list. Contact me also by PM and email/phone. Cheers, Gregg. Email: viz(at)xtra.co.nz Telefunk: sixtyfour274 377 086
-
Tim made me a moderator in the Eclair sub-forum so it should be possible to correct errors in the techs list and make it easy to find.... I planed to make one or more pinned threads that will serve only as directories, containing links to important info on other threads. Or potentially, links to important info external to the forum. Those pinned "directories" could be open or locked (I don't know it all yet). If open, people could include additional links in the content of subsequent posts. They would need to be fairly disciplined about what they add, or we will loose the simplicity I'm hoping for. Any suggestions on these ideas? Gregg. Email: viz(at)xtra.co.nz Telefunk: sixtyfour274 377 086 PS: I can edit any posts from this point on, but the corrections to the techs list I may have to do by replicating it, editing that, and hiding the old version. So don't be alarmed if that disappears
-
I thought I would work on the tech list while I had a moment, post it as a loud update on Heikki's existing thread, then figure out the pinning etc later. Probably we need a pinned thread that we use just to list a directory of important threads. That pinned thread needs to be updatable, perhaps just by fresh posts, but that may need to be done by a moderator etc. I may ask Tim Tyler.
-
Any chance you can measure the thickness of the TS-1 flange, the flat part where the mounting screws go. I know the outer thread is raised and I think the C mount may be deeper than the thickness. I don't know what your machine shop skills are like (measurement). If you need suggestions let me know. Then we would have a better start point for guessing about material to machine away. Accurate drawings I believe are the key with projects like this. Then guesswork is almost gone. Gregg.
-
That's an interesting mixed metaphor. Both rocket building techs and surgeons have an obsession with cleanliness, wear protective clothes, and masks I think.
-
How far are the Micro 4/3 lenses protruding behind their mount flange. The pics online look like there's no protrusion. What might be useful,' to consider mods to ACL, would be 3 view dwgs or solid model showing gate, body, TS-1 flange with C mount and mirror. Let's talk about that on the Eclair sub-forum.....