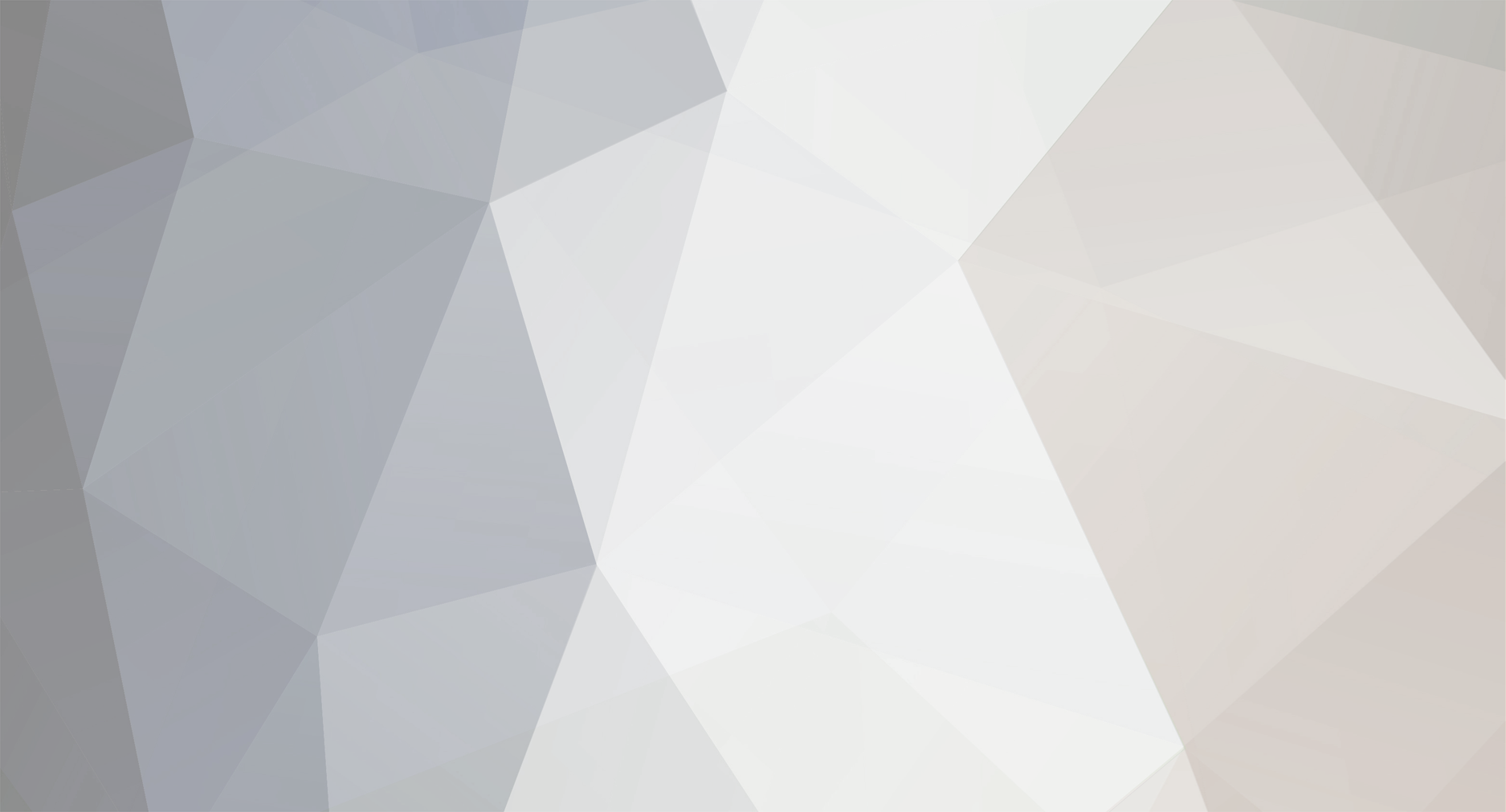
Gregg MacPherson
Premium Member-
Posts
2,640 -
Joined
-
Last visited
Everything posted by Gregg MacPherson
-
Spectra are really inexpensive on their rate card/website. Was 13 cents/foot for 16/35 colour neg. I'm guessing they don't move much when negotiating for a feature. Is there any downside to using them? I think they batch process but that might be for stock other than colour neg. Looks like a great place for indies/microbudget folk committed to film. In New Zealand we had two labs at NZ 45 cents/foot (US 34 cents/foot). One just closed. LA looks good. I talked to an indian film maker the other day and tried to find out how to guage costs in India. Very difficult for a white European to get a straight answer. Normally someone inserts themselves between you and the labs and negotiates a good rate for a commission. I can't help wondering, if you turned up at the labs looking like a veteran hippie Euro-expat holding an Arri ST what rate you might get. Gregg.
-
I don't have experience with NPR mags. I have been fixing some old ACL mags but they are not the same. You may get lucky and someone has seen and fixed this on NPR mags before. If it is the mag. There are some things you can do however to help logically deduce what the problem is. Load some clean camera stock and try to replicate the scratches. This confirms that they were in fact made in the camera. If you run with the mag doors off you may even be able to see where the scratches happen. Maybe it even happens at low speed. Assuming you replicated the scratches. Do all your magazines give the same scratches? If not then it's a problem with that particular mag. I'm guessing that you have carefully checked that you are loading your mags correctly? Loop sizes? You haven't got the thread path wrong so the film is rubbing on something? Are all the rollers moving freely? Check the ones in the light trap. If you have rollers set at an angle check those are free. Just saw a video of an NPR running with the doors off. I would do what I could to see where the scratches happen. For example, can you end your thread path just after the feed side drive sprocket, let the film just fall out of the magazine from there. What about ending the thread path as you exit the light trap, could you gently pull it through with your fingers? Ideas like that. Cheers, Gregg
-
When the potter is first introducing himself to camera the lines (scratches) are quite curved and sometimes there are dashed or brocken lines that are almost constant rather than changing frame to frame. Wierd. Can you see the scratches easily on the film? Are they on the emulsion side? Have you tried running some clean film with the take up door off - trying to see where the scratch starts? I liked the look and documentary tone of this little film. I liked the deep blacks and the modeling. Can we see a high resolution version somewhere? What stock was this? If you need a cheap heavy head there have been O'Connor 50s on eBay. Cheers, Gregg.
-
I found Tony's videos quite interesting and useful also. But I sympathise with Boris and Jean-Louis. Tony comes across on the video as sort of too relaxed. I diddn't agree with all that Tony said, but I still found it useful, if that makes sense. Re precautions when working on the mechanism plate, TI thought Tony had put some screws back into it so that he could rest the plate on the screws. Something that needs to happen, maybe we need a separate named thread for it. Workshop manuals and service manuals for ACL I and II need to get in the public domain. The number of experienced ACL camera techs is diminishing, but there are lots of skilled camera techs who know Arri, Aaton, Panavision ... ACLs are quite simple cameras (so I'm told) and if some documentation was available some of these guys would happily service them. So we need to find and make public domain the service docs. Also, I think camera owners need to document the service record of their gear. What was done, and by who. Cheers, Gregg.
-
Hey Daniel, My rotation to lock is about from 12 noon 'till 1 oclock if it's lucky. Maybe 20 degrees. I think there may be a bur on the edge of the chanel that the little Arri B wing fits into. Cheers, Gregg.
-
Find a skilled technician who knows those cameras well and make friends with them directly. I would start by finding out who did the work at/for Ice and see if they are still interested. If you can have always the same good technician you will save money on servicing. Opinins on the forum will vary on what the servicing requirements and costs are. I read somewhere that every 5 years the scintered aluminum bearings should be re impregnated with oil using vacum method. I talked to a tech in Australia recently who services a lot of Aatons and (he said) there are LTRs that have never had that bearing treatment in their whole life and are still going no problem. Cheers, Gregg.
-
I'm familiar with the ACL to Arri bayonet (TS/Arri-B) lens mounts. I have the type that I see in the manuals. The lens turns a few degrees untill the positive lock engages. It has a release button. I just bought another mount cheap on ebay. Turns out it is an ACL to Cameflex mount with an Arri-b adaptor fitted to the Cameflex port (TS/CA-1/Arri-B). The Arri adaptor feels like it doesn't want to move. If this mount is used I think one might just check the flange focal distance and leave it alone. This Arri adaptor has no positive lock mehanism. The lens is turned maybe only a couple of degrees till it's wedged in tight. Feels like it should turn more. Does anyone use one of these adaptors? How many degrees roughly do your lenses turn before they feel tight? Cheers, Gregg.
-
Zeiss MK II distagons - loose focus ring
Gregg MacPherson replied to Gregg MacPherson's topic in Lenses & Lens Accessories
I took the lenses to Stephen Spooner at Panavision in Auckland for a quick lookover. I described in an earlier post a small ampont of "backlash" in the focus ring of the 12mm. He showed me that the whole front of the lens has a mall amount of movement. He prescribed a re gtease and maybe the internal sliders need some fixing. Maybe a couple of hours work so not major. We put all the lenses on the projector and they all looked really sharp and had accurate focus marks, except the 12mm lens. All except the 12mm could show a clean 200 line pairs/mm. I think the 12mm was about 140 lp/mm, the 200 lp/mm block didn't look as crisp. Then in a few seconds the machine told us the shim thickness needed to correct the 12mm at a distance of 4', 8/1000mm. Way cool. Interesting and fun. Cheers, Gregg. -
Zeiss MK II distagons - loose focus ring
Gregg MacPherson replied to Gregg MacPherson's topic in Lenses & Lens Accessories
Thanks Tom, I was going to cheap nail polish for that. Smells like old school nitrocelulose laquer. -
Zeiss MK II distagons - loose focus ring
Gregg MacPherson replied to Gregg MacPherson's topic in Lenses & Lens Accessories
I didn't do that yet. If the "holes" are about 2mm diameter then what I saw on the 25mm could make sense. The screws were sitting loosly in the holes and became progressively constrained as they were screwed in. They actually were sitting about 2 or 3 turns loose. Thanks, Gregg. -
Zeiss MK II distagons - loose focus ring
Gregg MacPherson replied to Gregg MacPherson's topic in Lenses & Lens Accessories
Hey Dom, Thanks. The 25mm with the wiggly focus ring is all fixed. The scews were very loose. I tried to screw them all in roughly the same amount. The tightening torque I did wwas very light, just a light feel on my finger tips with a 10mm diameter handle on the screwdriver. The 12mm does in fact have some rotational movement of the front of the lens relative to the mount. It is so small I'm not sure I can see it, but you can feel it easily with your finger tips. So that one may need the doctor. Cheers, Gregg. -
I'm looking at some (S16) Zeiss MK II distagons. Ex German TV, quite cheap, optically quite clean and looking good through the viewfinder and hitting the focus marks. But on a couple of them there is some mechanical wear or loosness in the focus ring or what I assume are cams inside. I will show them to a good lens tech in a few days, but I'm really curious to get some ideas about it. The 12mm has what feels to the fingers like a fraction of a mm backlash in the focus ring. The little thud that you feel at either end of this is quite distict. The grease is fairly viscous so it's hard to tell if there is inertia involved or not. Like maybe something heavy is being rotated over that fraction of a degree. The 25mm has what feels like a very loose focus ring. If you look at the edge of the focus ring you see almost a mmm of completely free backlash in the focus movement (about 3/4 of a degree). You can wiggle the focus ring about the vertical and horizontal axis so you see over a mm of movement at the edge (a bit over a degree) Both these lenses look fine through the viewfinder while working the focus ring. You could actually use them just like that. Any thoughts? Dom? Cheers, Gregg.
-
I had talked to Stephen before about servicing ACLs. He would have a go as a home job but was unfamiliar with them. I looked around for some service docs that wouyld help but didn't yet find any, just some parts drawings. From experience with other cameras I think he could guess generic lubricants for the different parts of the magazines. I was just a bit shy of ringing up the Panavisiuon techs too often every time I was stuck. On my third magazine I am a bit faster, but it is still a lot of work to do a full dissassembly and lube. I realize now that my service guy from the 1980s never used to do all of this every time. Thinking of easily availablr generic lubricants. The synthetic grease that my service tech used in the camera body in 1995 looks and feels just like the TF2 Lithium Grease from the local bike shop. Cheers, Gregg
-
Hey Tony, There is someone selling photocopies of them on eBay http://global.ebay.com/Arri-Arriflex-IIB-IIC-Factory-Repair-Manual/200400688386/item maybe someone on the forum has a scanned copy they can send for free. Cheers, Gregg
-
The back story or motivation for this post is the three English Eclair ACL 400' mags that I had sitting here, unusable due to needing service. I don't know anyone left in NZ who knows how to survice them , so, with some research and care I decided to service them myself. I had the parts diagram but not the service manual. All went really well, except that I don't know what are appropriate lubricants for diffent parts. I saw a post by Chuck Colburn where he stated the lubricants they used on all the cameras they serviced. looked like this: Losoid. -33B for movement gearing, Arri phenolic pull down claws, most lens rotating and sliuding surfaces. -BBR-1 for ball bearings, fibre gearing. - #70 for areas needing heavier lube. I think those are all greases. A good start, but not easy to find. So my question is, are there generic, readily available lubricants that will serve? Cheers, Gregg
-
Pretty cool thing to do, but quite bulky eh. There was a guy in Canada who recently sold a really nice ACL kit who had made a video tap with that idea, but I think it was a small camera. I lost the reference. I have an AZ Spectrum B&W unit that I could only test recently as I didn't have a monitor. I ended up buying a Transvideo 5" monitor recently so I could test it. The image wasn't very bright, but it may be the monitor. Unfortunately testing an NTSC-only monitore down here in Neuvel Zealandia is less easy. Maybe I'll try borrowing a decent monitor and report back. I asked Andrew at AZ Spectrum what monitor I should use and he basically said anything. But I'm wondering what people use. These systems are needed for basic framing, so the image needs high brightness and contrast. For those wanting to build their own system there have been some used video taps sold cheap on eBay recently that one could adapt. Cheers, Gregg
-
Who sells Kinoptik lenses
Gregg MacPherson replied to Gregg MacPherson's topic in Lenses & Lens Accessories
Thanks Bernie, I saw their website and all the lenses they still stock. But nobody answered my emaid. I'll brush up on my high school French and phone them. In the meantime I decided to sell my nice Kinoptik 9mm T1.7. Cheers, Gregg. -
Does anyone know who sells Kinoptik lenses? I emailed Kinoptik (in English - je ne parle Fracais mais un petite) and got no reply. I find nothing on the web. I have an almost new Kinoptic Grand Angle 9mm T1.7. Beautful modern lens with integral focus and aperture gears. I was deciding wether to try adding to that but Kinoptic are quite rare. Cheers, Gregg.
-
I came back to this servicing problem again. I have three English 400' mags sitting around here. All need servicing and feel too stiff when you manually turn the drive sprocket. I removed the front of the mag with its pressure plate to get a better look. I removed the plate holding the two "guide shoes", the asemblies that sit around the drive sprocket. Also removed the take up arm assembly and its spring system on the feed side. I could now see the toothed belt connecting the drive sprocket spindle to the take up arm drive spindle. It was obvious from the belt behaviour that the friction was in the take up arm spindle. The grease for the plain bronz bearing surface in that gear was old and quite dry. The drive sprocket bearing felt free and smooth. I think (guess) that has the same bearing idea as a French one and will have a single ball bearing with a light press fit in the drive sprocket hub. I have a new French one and the drive sprocket hub, which is the bearing housing, I can pull off the bearing and spindle after removing a grub screw. This English one I couldn't pull off. So there is no need to remove the brass gear from the drive sprocket assembly on the feed side. The assembly is designed to be taken apart from the take up side, IMHO. I decided to service everything else if possible. The rubber take up drive wheels I had a local small manufacturer make some for about $1 each. Testing I did a while ago on that looked good. If it pans out I'll forward info on dimensions and materials. As I have no drawings/parts list for these magazines I have to guess that the magazine oblique drive shaft has ball bearings like the drawings for the French mag, but I can't know for sure. The shaft does feel like it has them. If they are sealed bearings I will just leave them alone. I'll report back on how it goes. Cheers, Gregg
-
I was a bit hurried and didn't explain much. Print commonly means a positive exposed from a negative. So if you shoot camera negative you can process that and then make a positive print for editing, projection. So all your processing was negative rather than reversal. You can use reversal camera stock and make a positive (reveresal) print from that also if you had some reason to. Prints for projection or editing are normally made in a contact printer. The processed negative sits in contact with the print stock as they move continuously through the machine. If your art film can have some rough edges or inconsistencies than you can improvise something for crude contact printing. An optical printer, in the siple case basically re-photographs the camera negative frame by frame. Again, if you can accept something less than the commercial lab with the results then you can improvise a DIY optical printer. It's quite a lot of work to set up for even a crude result, but if you enjoy that kind of thing it's super interesting. Cheers, Gregg.
-
Hey Antonio, An old spring wound Bolex used to be my camera of choice for this kind of thing. Can do single frame for pixilation or animation, in camera effects. Stay standard 16mm and just use the old Bolex primes. They are normally quite sharp. If you like tinkering with mechanical things it is possible to make a crude optical printer with an old projector head and a bolex. Worked for me years ago. It is also possible to set up a crude B&W contact printer. I bipacked the film in the picture gate of a flatbed editor and exposed it with a thin slit of light from my magnalight torch. Some carboard construction with that for positioning and catching stray light. Cardboard cartons covered the spools. Results were not bad. Not as consistent or predictable as a lab. Cheers, Gregg.
-
Does anyone recognize this power adaptor/charger? It's a JVC AA-C50 that I was given and might find useful if I knew what type batteries it charged, NiCd/NiMhi/LiPo ? It is a 12V, 3.5A DC power supply, 12-16V charger. Fast and trickle charge switches automatically. Connectors are XLR4. Does anyone know what type battries it can charge, .NiCd/NiMhi/LiPo ? I scoured the net for an hour and didn't find anything yet. Thanks, Gregg
-
I think english 400' mags are all right, as long as the camera and mags are not in need of service. I would get a tech to check the mag over and he could compare the current draw. I used an English ACL I with the small original motor and English 400' mags a lot. My motor looked stock. I don't think there were any changes to the electronics. I had a friend with the same configuration also. I never had any problems with the motor. It looked like it got to speed in about 2 frames with a good battery. The camera and one of the 400' mags was always well serviced. Another couple of mags were probably overdue for a lube, but showed no problems with the motor. If you aren't able to get a tech to check over the mag before you need to use it you can check a couple of things yourself. With the take up wheels working on a core the drive sprocket should feel fairly free to your fingers. It's got an inching knob you can work. Then load some scrap film and see if there is any difference in the motor behaviour compared to a 200' mag. I would test about 800' with a few stops and starts to check the start up time (sync light) and motor temperature. Any unusual motor sound or running out of sync and you stop. Cheers, Gregg
-
Thanks Stephen and Tim, I'm trying to get a comparison between the maintainence requirements of these two cameras ao I get a better feel for the viability of ownhg one to shoot occasional pet projects. I used an ACL I that I owned quite a lot in the 80s...early 90s. It had seen quite a lot of use when I got it, but had been maintained. I had it regularly serviced. The last service was a full lube for the camera, two mags and the Angeneuix 12-120 plus colimation and it was less than US$ 450. This was done after hours by a TVNZ camera tech who knew ACLs, so I think it was cheaper than if done officially. With inflation here that is US$ 972 in todays currency. I think if one can keep the maintenace cost down and the camera is in good shape when you get it then an ACL is a viable one to own to shoot low budget personal projects. I'm thinking the Aatons are more fragile and expensive to maintain. Cheers, Gregg