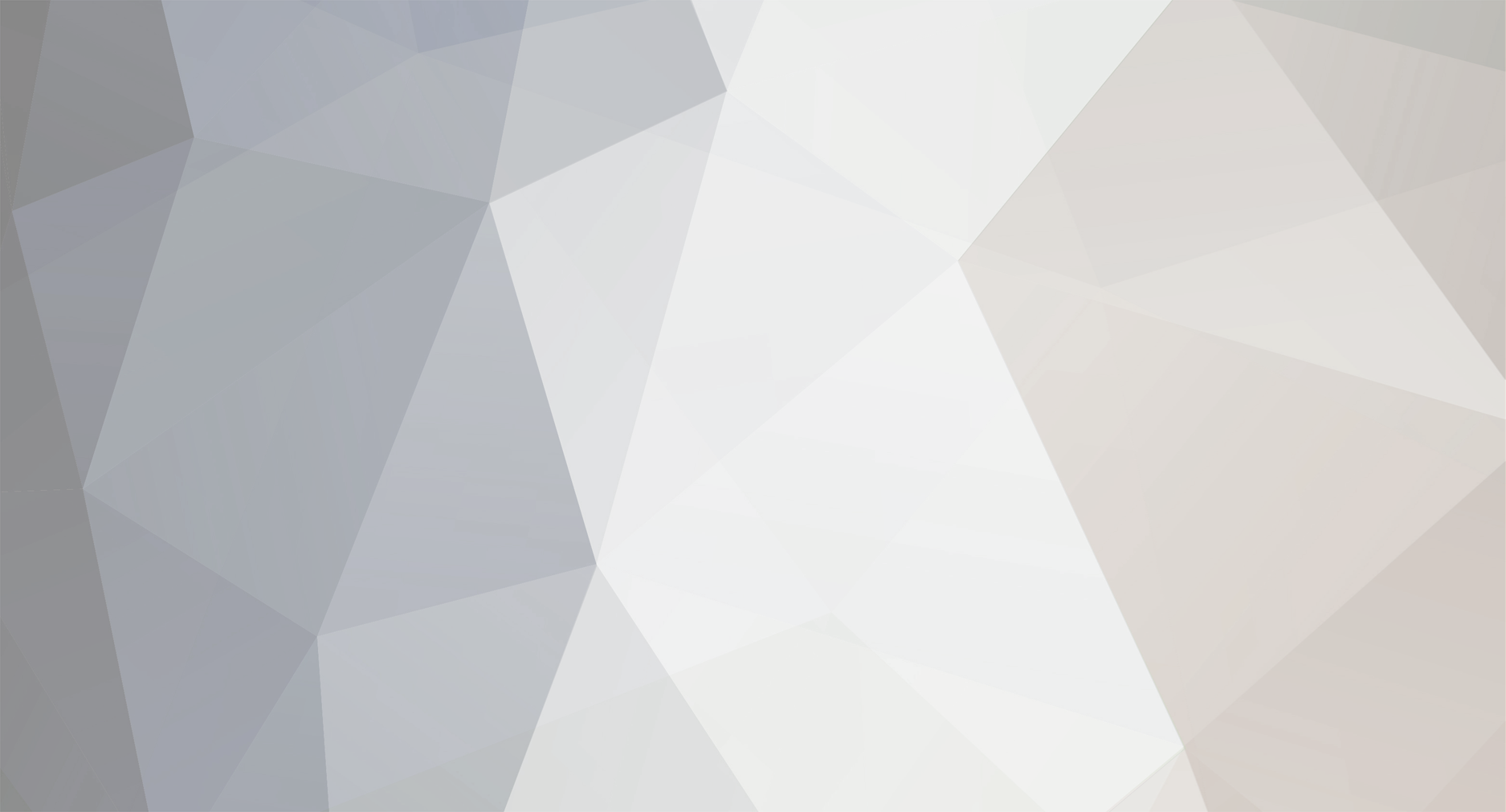
Friedemann Wachsmuth
Basic Member-
Posts
151 -
Joined
-
Last visited
About Friedemann Wachsmuth
- Birthday 06/02/1976
Profile Information
-
Occupation
Other
-
Location
Hamburg, Germany
Contact Methods
-
Website URL
http://www.filmkorn.org/
Recent Profile Visitors
The recent visitors block is disabled and is not being shown to other users.
-
A New Crystal Sync Motor for the Arri 16s
Friedemann Wachsmuth replied to Kamran Pakseresht's topic in 16mm
Amazing outcome!! Congratulations! -
Inside a 24fps Crystal Controller (Photos)
Friedemann Wachsmuth replied to Kamran Pakseresht's topic in Bolex
EDIT: After looking closer at the schematics, I think the tacho is actually sending 80 pulses per revolution — the 8493 divides that down to 10, matching the 240 Hz from the decimal divider behind the crystal. -
Inside a 24fps Crystal Controller (Photos)
Friedemann Wachsmuth replied to Kamran Pakseresht's topic in Bolex
Thanks, Thomas. So my date-guess was right (Schematics from 1972), and it is indeed dividing by 800, so the tacho seems to send 8 pulses per revolution. A very neat and pragmatic control circuit design indeed. -
Inside a 24fps Crystal Controller (Photos)
Friedemann Wachsmuth replied to Kamran Pakseresht's topic in Bolex
Ah, I see. I must have mixed you up then with someone else who insisted against using uCs an/or DDS for frequency generation a while ago. Sorry. 🙂 -
Inside a 24fps Crystal Controller (Photos)
Friedemann Wachsmuth replied to Kamran Pakseresht's topic in Bolex
For anybody interested, below is my C code (free) that configures the "Timer 1" on a AtMega328p (aka Arduino) running on at 16 MHz crystal to rather precise 9, 16 2/3, 18, 24 or 25 Hz pulse machines. The results (e.g. 24.000024 Hz) are higher precision than a normal crystal itself — if required (and you are using a temperature compensated crystal or whatever) , the small diff from actual 24 Hz can rather easily be corrected in software. bool setupTimer1forFps(byte sollFpsState) { // start with a new sync point, no need to catch up differences from before. timerFrames = 0; projectorFrames = 0; timerDivider = 0; if (sollFpsState >= 1 && sollFpsState <= 5) { Serial.print(F("New Timer FPS State: ")); Serial.println(sollFpsState); noInterrupts(); // Clear registers TCCR1A = 0; TCCR1B = 0; TCNT1 = 0; // CTC TCCR1B |= (1 << WGM12); switch (sollFpsState) { case FPS_9: OCR1A = 10100; // 198.000198000198 Hz (16000000/((10100+1)*8)), // divided by 22 is 9,000009.. Hz // TCCR1B |= (1 << CS11); // Prescaler 8 timerFactor = 22; break; case FPS_16_2_3: OCR1A = 14999; // 16 2/3 Hz (16000000/((14999+1)*64)) TCCR1B |= (1 << CS11) | (1 << CS10); // Prescaler 64 timerFactor = 1; break; case FPS_18: OCR1A = 10100; // 198.000198000198 Hz (16000000/((10100+1)*8)), // divided by 11 is 18.000018.. Hz // or 18 2/111,111 // or 2,000,000/111,111 // TCCR1B |= (1 << CS11); // Prescaler 8 timerFactor = 11; break; case FPS_24: OCR1A = 60605; // 264.000264000264 Hz (16000000/((60605+1)*1)), // divided by 11 is 24.000024.. Hz // or 24 8/333,333 // or 8,000,000 / 333,333 // TCCR1B |= (1 << CS10); // Prescaler 1 timerFactor = 11; break; case FPS_25: OCR1A = 624; // 25 Hz (16000000/((624+1)*1024)) TCCR1B |= (1 << CS12) | (1 << CS10); // Prescaler 1024 timerFactor = 1; break; default: break; } // Output Compare Match A Interrupt Enable TIMSK1 |= (1 << OCIE1A); interrupts(); } else { // invalid fps requested Serial.println(F("Invalid FPS request")); return false; } } -
Inside a 24fps Crystal Controller (Photos)
Friedemann Wachsmuth replied to Kamran Pakseresht's topic in Bolex
The date code on these chips indicates that they are probably from 1973/74. Manufacturer is National Semiconductor — the reason that you didn't find datasheets easily is that these were "military grade". NS names the 74xx series chip as 84xx if they e.g. allowed higher temperature grades. So, basically they are 7490 and 7493. Both are monolithic counters. They contain four master-slave flip-flops and additional gating to provide a divide-by-two counter (total counts up tp 10) and a three-stage binary counter (counts up to 16). As far as the PCB traces suggest, the 7490 were configured as counting to 10, so resulting in dividing the 24 kHz down to 240 Hz — as Aapo suggested. The motor probably didn't provide 10 pulses per rotation though but a power of 2 (so 2, 4, 8 or 16) — hance the xx93. What Aapo didn't mention though is that just having two frequencies is not controlling the motor speed yet. comparing the pulse count and turning it into a (non-oscillating) control voltage for the motor is the other half of the challenge. They have achieved this without any OpAmp! I am rather amused by that ancient type of crystal coming in a glass tube — especially since it seems to be bedded on some foam and mounted with a... rubberband? 🙂 This isn't quite right. You cannot only divide by powers of 2 (like 8192 or 1024) with discrete counters. With e.g. a 4017 you can also divide by 3, 4, 5, 6, 7, 8, 9 or 10 — just the duty cycle changes unless you fix it with further flip-flops. So, a 6 MHz crystal (common for USB interfaces) can provide 24 and 25 fps references, a 18 MHz crystal (typical SD-TV pixel clock) can provide 18, 24 or 25 fps references with such "old school dividers". I am glad that you finally switched to software, Aapo — are you using the 328p timer configs I shared with you back in the day? 🙂 -
A new development tank?
Friedemann Wachsmuth replied to Friedemann Wachsmuth's topic in Film Stocks & Processing
https://www.filmomat.eu/shop/manual-816mm-processing-system -
ORWO NC500 initial thoughts
Friedemann Wachsmuth replied to Tyler Purcell's topic in Film Stocks & Processing
I can't prove it but think you are on a wrong track here. ? Can't wait for your tests though! I'll shoot my two rolls next Sunday, haven't decided yet how I'll process them. I was considering ECN-2 and the getting a proper print, so that I can't really bend its curves. -
DIY - Reloadable Super-8 cartridges
Friedemann Wachsmuth replied to Thomas Larang's topic in Super-8
They always say that, even when I speak to other Germans ? Guess I should make an English version of that video, too. Too bad that currently no new Adox cartridges are being made, the tools are all still there though. -
Is there a demand for custom sync sound motors?
Friedemann Wachsmuth replied to Aapo Lettinen's topic in General Discussion
What does "ROV project" stand for? -
Is there a demand for custom sync sound motors?
Friedemann Wachsmuth replied to Aapo Lettinen's topic in General Discussion
Aapo, don't let yourself get down by this. My experience is That most people can't imagine a hypothetical product enough to get really hooked. Once you have a fully working solution, with all the kinks removed and bugs fixed, a manual, nice photos and maybe an example video, this will change. See how Kickstarter works. There is nothing but semi pro videos, mellow piano music and often pretty brilliant marketing claims. A scale of yummy pledges makes people not want to miss out. And at the end, some goon collected a lot of money, runs with it and never delivers. And you know what? Most "customers" forgot about their contribution and don't even miss their pledge. I guess that's just how capitalism works... ¯\_(ツ)_/¯ People seeing a prototype strip board with bodge wires on a messy workbench doesn't sell. It does gain interest, but not enough to make a commitment. My recommendation would be: Keep going. Don't think product. Think about what you want to achieve for yourself only. If you feel for that, share your thoughts and see what others reaction is. Feel free to ignore it. Harvest the gems that might have been brought up. Involve others only as much as you feel comfortable. Only then, when it works for you and you are 100% happy, consider making it a product. If you don't feel like productizing, you can still make it open source. That's my absolute favorite way to go. It is by far the most pleasing... for me, at least. -
Is there a demand for custom sync sound motors?
Friedemann Wachsmuth replied to Aapo Lettinen's topic in General Discussion
Huh, I feat I can't help you further w/o the actual schematics (if at all). I'd swap the cap as an almost free try (well, few cents, if you have none around) — that's low risk. BTW, when you have your Multimeter in Resistance mode, your are not "bridging" the cap. In the multimeter is a battery and you are sending a current through the test leads. That current might well also go thorugh the transistors (and whatever is connected with that cap) and hence "make it appear alive" — so I wouldn't bet too much that the cap is to blame. Germanium transistors do not like vibration/concussions. Might well be that one of them died. They are around 60 years old after all... -
Sorry, I had no intention to let you look bad! I apologise for how I articulated my post. At no times I wanted to be rude or let you look bad. I did not know that you intend to etch these boards on your own. I probably did not read that part. I do that with prototypes too, but usually not for production versions — dual layer edging DIY is hard, and JLCPCB takes $2 for 5 small 2-layer boards, so I usually go the china route. Just so you know, my last two JLCPCB orders (in COVID times) made it without problems to here (Germany, via DHL Express), while some Aliexpress orders are indeed still waiting. So I hear you on the board complexity ? I guess that's also why you are not considering SMT over THT to keep the size to a minimum?
-
Is there a demand for custom sync sound motors?
Friedemann Wachsmuth replied to Aapo Lettinen's topic in General Discussion
Wow, OC30 is one old germanium transistor! I am still not sure what you meant with "bridging". What Mode was your Multimeter set to when you measured, I guess on the two legs of that capacitor? I wouldn't be too sure that schematic you found is the same in your camera, but it is neither impossible. - If your cap is dead, like shortened, measuring over it in any mode should not make a difference. - If your cap is not dead, but lacks capacity (dried out), and your multimeter was in continuity mode, your brief "bridging" might have "simulated" what the cap was intended to do: Create a pulse (to get the motor going). Can you reproduce to start the dead motor with your "bridging" trick? And again, what is your multimeter set to? -
Is there a demand for custom sync sound motors?
Friedemann Wachsmuth replied to Aapo Lettinen's topic in General Discussion
Hard to say without seeing more of the schematics. It's a bit too big for a snubber. When you said "bypass", do you mean bridging it or taking it out?