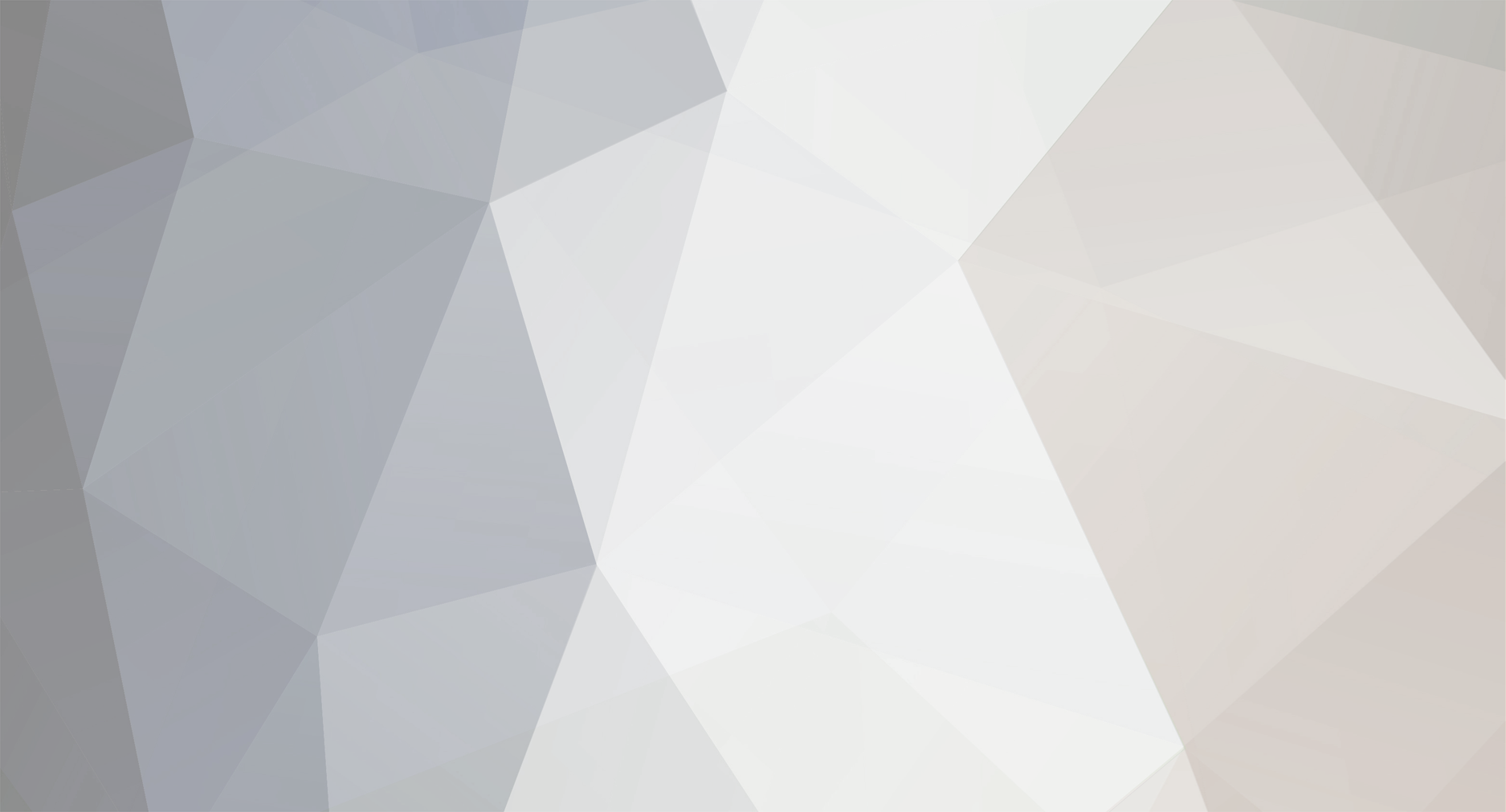
Robert Lewis
Basic Member-
Posts
187 -
Joined
-
Last visited
Everything posted by Robert Lewis
-
I have been thinking about buying an Aaton A Minima as a camera light enough to take abroad on holidays, etc, instead of the much heavier Aaton LTR54 I have. That said I am concerned about the discontinuation by Kodak of the special spools with flanges and cores which I understand were developed jointly with Aaton and which are said to be patented by Kodak. Kodak advise that their spools should only be used a few times, and so there seems to be an risk of obsolescence which, if there is no way around it, could mean that the A Minima will shortly become useless. I know that film stock can be reversed so it is presently possible to buy stock, reverse the winding to "A" (emulsion outward) as long as one has spools and cores, but if spools and/or cores really do cease to be available, even that would not be possible. Or would it? Having looked very closely at photographs, some good and some not so good, it does seem to me that it might be that the standard 16mm two inch cores might be useable but without the flanges which the Kodak spools and flanges used to come with, if the flanges were originally used in order to provide for "daylight" loading and the cores will fit the camera drives. It seems to me, but only with the benefit of photographs, that the first type of core used by Kodak is almost identical to the present day standard 2 inch core modified to accept the flanges. I am wondering if any owner of an A Minima has any experience in using standard cores in their camera - whether firstly the core itself will fit, and secondly whether there is any problem as a result of there being no flanges. This, of course, the arrangement used in other 16mm Aaton cameras and the Arriflex SR family. Any help on this point would be most helpful and appreciated.
-
No.w.here film lab - sad news from east london
Robert Lewis replied to Geoff Howell's topic in Film Stocks & Processing
Until almost 12 months ago I used to have all of my 16mm B&W Negative film (mainly 7222) processed and printed at NO.W.HERE in East London, but they decided not to continue to undertake this work as a service. I understand that attempts were made to establish a group of users as a "cooperative" and I tried quite hard to persuade them to make some provision for those of us who do not live in London and could not, except at considerable cost and perhaps involving an overnight stay in London, participate in a "self help" group. I am not sure, therefore, whether any processing of 16mm b&w is presently being undertaken at NO.W.HERE's premises in Bethnal Green. For this reason, I have not been using film for the best part of a year. I think I would have known if the service had resumed. Nonetheless, whilst I very much hope that their present difficulties are overcome, I have, of course, looked for alternative facilities, and considered using colour filmstock in future since generally it seems to be easier to get colour processed and printed than b&w stock. However, I recently discovered "Film in Process" (filminprocess.com). They are based at the University of East London. Film in Process is a small artist run business providing a 16mm B&W processing and printing service and was set up by Bea Haut and Karel Doing in 2015. These names will be familier to those who have used NO.W.HERE in the past, and I presently have a film with them for processing and printing. I thought I should pass this information on - helping those who need B & W Negative processing and printing, and hopefully helping to support Bea Haut and Karel Doing and "Film in Process". -
Arri Standard / Bayonet mount lenses
Robert Lewis replied to Jay Young's topic in Lenses & Lens Accessories
Looking at the pictures of the lenses offered on ebay, I am reminded that one needs to be very careful with the use of older Schneider Kreuznach lenses fitted with Arri Standard mounts. Those which can be used on 35mm cameras generally (the lenses with hardly any protusion beyond the rear of the mount) can, I believe, be used without any difficulty on any 16mm camera using an Arri standard mount, although they will not strictly reproduce the stated focal length of the lens in question. Those with the small diameter protrusion are true 16mm lenses and can be used on a 16mm camera, but it is a good idea to check the clearance of the lens in relation to a mirror shutter (as on an Arri SR camera) to make sure that the rotating mirror will not collide with the rear of the lens when fitted. The third type of lens, that is to say those with two stage protrusions, have to be handled with particular care when used on cameras fitted with a mirror shutter. My understanding is that they will not be a problem on, say, Arri S type cameras, but they too should be checked carefully. However there might well be a problem with Arri SR cameras on which the distance between the mirror and the rear of the mount was reduced. On these, my understanding is that there is a real risk of collision and damage to the mirror shutter. Just thought I should mention this. I am not sure whether this is relevant to CP-16 cameras, as I have no experience with that particular make of camera. -
Arri Standard / Bayonet mount lenses
Robert Lewis replied to Jay Young's topic in Lenses & Lens Accessories
Miguel ... That really is a very generous offer, but I was able to use the refund from the dealer to put towards a more expensive replacement 25mm lens. I am sure that your lens would be far more beneficial to a student in cinemaphotography, perhaps one on a tight budget. My contribution to this topic was merely intended to urge caution when purchasing old lenses. I do agree with your comments on the image quality they produce. It is an unfortunate fact of life that if things go wrong and a fault develops it is unlikely that parts will be available to effect a repair. That said, I would not wish it to be thought that I was criticising either the lens,or Schneider Kreuznach and the dealer acted most honourably. Being a realist, I understand that manufacturers cannot be expected to maintain stocks of spare parts for 40 or 50 year old lenses. Best regards, and once again thank you for your generous offer. -
Arri Standard / Bayonet mount lenses
Robert Lewis replied to Jay Young's topic in Lenses & Lens Accessories
One word of caution if I might be permitted to offer it. I recently bought a Schneider Kreutznach 25mm lense, and on delivery it appeared to be in very nice condition. I was very pleased. Unfortunately, however, on being used, it developed a fault. The tiny rivets holding the aperture blades in position (or rather I think one of them) failed with the result that when the aperture was set, a couple of blades collided with each other and were distorted. I was hopeful that I could get the lens repaired, but I learnt that there are simply no spares for these lenses and there was nothing to be done. Fortunately, I had purchased the lens from a dealer who tried unsuccessfuly to get it repaired and they immediately refunded the purchase price. I believe that Schneider Kreuznach lenses are very good lenses, but the lower priced ones are quite old. Lenses can and do develop problems, so just be aware that there may be no spare parts available for them. I attach a picture of what happened to the lens I had. -
Bolex H16EL MKIII Troubelshooting PLZ
Robert Lewis replied to Muhammad Usman Khaild's topic in Bolex
Hello again. I am not a technician, and so I am not able to advise you how you should go about sorting out the problem you have with your camera. What I do say is that the camera has complex electronics within it, and I think we have now established that there may well be a connection between the failure of the camera to start running properly and the fact that the exposure button is not operating correctly. Without any hestitation I would strongly advise you not to try to repair the camera yourself. What I suggest you do is to contact Bolex directly in Switzerland or perhaps an engineer in the USA who is experienced specifically in dealing with Bolex cameras and the EL Mark III in particular. You need to explain what is happening and in particular tell them that the exposure button is not operating correctly. You can email Marc Ueter at Bolex (email: sales@bolex.ch) and he will be able to advise you. I am sorry that I am not able to help you further, but I wish you success.- 9 replies
-
- repair
- troubleshooting
-
(and 2 more)
Tagged with:
-
Bolex H16EL MKIII Troubelshooting PLZ
Robert Lewis replied to Muhammad Usman Khaild's topic in Bolex
Hello. First of all, it is a Mark III camera you have. I have one of these cameras and you can establish this by looking at the ASA setting dial. It goes as high as ASA1600 on the Mark III and it is the only model which can be set to this. As I understand it what you are saying is that when you try to start the camera rolling, you get a "clunck" sound and the camera motor turns slightly and then stops. I appreciate that you have rebuilt the battery, and in the ordinary course of events I would say that I suspect that despite this it might be that for some reason the battery is not holding enough charge. The "clunck" sound and partial movement is indicative that there is insufficient power. I suggest, therefore, that you double check that the battery is holding the correct voltage and amperage. You can do this by by checking it with a meter. If a check indicates that the battery is fine, you can check that the camera is receiving the correct amount of power in order to operate by pressing the tiny white button on the rear of the camera. The "battery check" red light should illuminate and then immediately go off. The two red lights you see in the viewfinder should not be on until you press the exposure check button which is located on the top of the camera just above the lens. Normally the lights should stay on for a short period only whilst you are setting the exposure on the lens and then the button should be released automatically and the lights should go out. The fact that you say these lights are on when you try to start the camera suggests that there is a problem in this area. Is the exposure check button stuck down, or are you able to press it down and see it rise again after a short interval? It should not be stuck down and if it is, it may be that this is connected with what you are experiencing. It might just be that the exposure check button has been pressed down but there is insufficient power in the battery to trigger the automatic release of the button. I suggest you check these points before doing anything else. Best of luck.- 9 replies
-
- repair
- troubleshooting
-
(and 2 more)
Tagged with:
-
REQ: Bolex H16EL Service Repair Manual.
Robert Lewis replied to Muhammad Usman Khaild's topic in Bolex
It appears to be a Mark III EL camera that you have and so I think you do not have to open up the base in order to get at the fuse. Just below the three connection plugs shown in your picture there is a fuse cap in the side of the base.You access the fuse by removing this cap. That having been said, I would have thought that the fuse is OK because you say you are getting the appropriate result when you press the battery check button on the back of the camera. It is possible that if you are not using a battery which is in good condition, the battery might be holding enough charge to allow you to get a positive reading when you press the test button, but not enough to get the camera to run. Before going further, therefore, I suggest that you check the condition of your battery and make sure that it is holding a good charge. The fact that you are getting a "clunk" sound when you try to operate the camera suggests that the fuse is OK and that it may just be that the battery is the problem. Try this. -
Am i Missing any film buying options in the UK?
Robert Lewis replied to Gareth North's topic in Film Stocks & Processing
You can also order ORWO stock (both UN54 and 74) through FilmoTec's British Agent, Tom Samuels. His email address for enquiries and orders is "tomsamuels@ntlworld.com". He is a most helpful and charming man to talk with, and orders are handled most efficiently. -
Apologies to all.....I am not sure how the 'Smiley' got into my posting above. It should have been a '(b)'.
-
Peter .... I am not sure that it is correct to say that "The perforation pitch was always short pitch 2994". I think it is now clear that Filmotec produced some 16mm UN54 stock which was perforated at .3000 pitch. That much is clear because (a) Filmotec themselves said so and also said that they had sold some of it to a retailer in Germany and by that means it had got into the supply chain, and (b) 16mm UN54 stock is still offered for sale in Germany which is perforated at .3000 pitch. It might well be correct to say that the Company's standard pitch was and is .2994, the same as Kodak Eastman 7222 and other 16mm stocks, but any confusion there is about the actual pitch was, I think, inadvertently brought about by Filmotec stating in an email some seven months ago that their standard pitch is .2996. That, as I said in my last posting was corrected in an email yesterday, when it was said that a review of emails had revealed that a mistake had been made when it was stated that the pitch is .2996. I actually found myself using shooting some 16mm UN54 perforated at both .2994 and .3000.The can in which stock perforated at .3000 pitch didn't actually state the pitch, but I didn't have a difficulty with either. At the time, though, I did think that the stock which had been perforated at pitch .3000 was a little noisier than normal as it passed through my Aaton and Arriflex SRII cameras. It certainly didn't cause any jam. However, some on this Forum have reported camera jamming. Whether that is related to pitch or to some other issue, I know not. Hopefully all is now well, and all we have to do is to make sure that when purchasing stock we buy stock which is pitched at .2994, as you say. Best regards.
-
In my posting dated 3 June 2013, I reported that in an exchange of emails with Filmotec I had been informed that the standard perforation pitch of 16mm UN54 filmstock is .2996. I said that I had sought to establish that ".2996" was correct and was not a typographical error, and had been assured that it was correct. I have today received a further email from Filmotec stating that on checking emails from last year (2013) it has been found that a mistake had, in fact been made, and that the perforation pitch should have been expressed as ".2994". I have to say that when I did my comparisons (referred to in earlier postings) I had concluded that the stock supplied directly from Filmotec was perforated at a pitch of .2994 (the same as Kodak Eastman 7222 stock), but felt that I could not do other than accept the statement made by Filmotec that it was perforated at a pitch of ".2996". So there we have it. The standard perforation pitch of 16mm ORWO UN54 is .2994. Now we can get on with buying and shooting UN54 comforted by the knowledge that it is perforated at a pitch of ".2994".
-
I have tried to understand the thinking and apparent enthusiasm for this, but I struggle. I find myself not able to get away from the thought that it is rather like designing a horse and cart and fitting the most modern and powerful engine into it so that it whilst it looks like a horse and cart it is really a car which happens to look like a horse and cart. What is the sense behind it? Bolex is an icon of cinephotography, and I cannot imagine many, if any, Bolex enthusiasts are going to be impressed with or buy this camera because whilst it "borrows" a name which is really only known for its association with film, it appears to have no substantial manufacturing connection with this Company and does not work with film. I think this, in turn, raises the question as to why this topic should be listed under the Forum "Cameras Systems and Formats - 16mm"? It is a camera, a system and a format, but it is not 16mm as that term is generally understood. Are those who are wishing to buy a video camera really going to buy this camera because it looks a little like a Super8 camera or despite the fact that it does? I have some doubts.
-
I have a Bolex SBM, and when I looked at your picture of the filter, it appeared a little strange to me. I therefore checked my camera and compared it with yours. If you look closely at your photograph of the filter, there appears to be a gap above the filter. One can see through this gap. On my camera, the gap is closed by a plate and one cannot see what is behind the plate. It occurs to me that if one can see through that gap then it is possible that light is able to get through it too. Behind the gap lies the prism and if light is able to get to the prism it seems to me possible that it is able to get into the top of the prism and thence to the rear face of the prism. Behind the prism is the shutter. Now, if light is contuously getting to the shutter, it is possibe that it is somehow getting to the edges of your film. The pressure pad pressing the film against the gate might be preventing the light affecting most of the picture area, but on the edges of the film, the pressure pad might not be quite achieving that. I also took a look at pictures of the mount area of an SBM camera which appears in Andrew Alden's book "Bolex Bible" (well worth getting if you do not already have a copy), and the gap to which I refer above appears to be blocked as it is on my camera. I hope this helpful, and apologies in advance if I am wrong.
-
I guess that one's opinion on the respective qualities of digital recording as opposed to true "filming" are best described as "subjective", since there is no "standard" by which the two can be judged. Having watched the final four Poirot stories, which it has been pointed out, were were recorded digitally, unlike the those which preceded them, I have to say that as a viewer I think the imagery of the final four lacked something. In my view the earlier filmed stories were visually much better. What this demonstrates, I suggest, is, apart from the subjective nature of the consideration of the imagery, that as things stand at the present time digital recording of imagery as opposed recording on film is very much a case of both having their respective place. It is because I think this that I record both digital and film imagery, and do so because I believe that both have their place. I can't say that I have seen all of the productions mentioned by Mr Deep, but those that seen I have have registered with me as being excellent. I am therefore delighted that the BBC have finally been persuaded of the error of their ways.
-
New option for a film lab in the UK!
Robert Lewis replied to Freya Black's topic in Film Stocks & Processing
Unfortunately this is not such good news. I managed to speak with somebody at Cinelab London (as Bucks Labs are now called) only to learn that they are not really adding to services available in the UK. They will be processing film and transferring to digital, but importantly they will not be printing. I suspect like others, I had hoped to hear that we were about to have a reversal of the trend to desert those of us who require a print service. -
Indeed Dirk!
-
Hello Brian, It was good to talk with you also. I know Tom, and you are right when you say he is most helpful and, indeed, as are you. It is always a great pleasure to talk with both of you. The information that Filmotec perforate their 16mm film at the pitch of .2996 came directly from the Company in an email, and at first I thought it might be a typographical error. However I did go back to them on the point, and they confirmed the pitch is .2996. Tom also told me in a conversation with him that that was Filmotec's standard. So I think that the information is pretty sound. That having been said, it seems to me that the difference between .2994 and .2996 is so tiny that it is within what one might say is an acceptable tolerance....what is it 2 ten-thousandths of an inch? I find it difficult to believe that with a material such as film it is possible to be certain that all 16mm filmstocks are accurate to the fourth decimal point. Certainly, my experience with using film perforated at the pitch of .3000 was limited to a feeling that it was going through the camera a little more noisier than filmstock said to be perforated at the rate of .2994. I do find it difficult to imagine that two ten-thousandths of an inch is going to result in even that. However, we shall see. All of this, I believe, demonstrates that one can talk about these things with Filmotec and that they are open to dialogue. This, I believe is to their credit. Finally, I have tried to ascertain what level of tolerance in perforation pitch Aaton and Arriflex allowed for in their respective camera specifications, but I have not been successful in finding this information. It would be intersting to know whether either of them did actually allow a tolerance or whether they designed to an intolerant standard..
-
Mark. As indicated in an earlier posting, I have been in communication directly with Filmotec who have, I feel, been most helpful. I have earlier given information about the edge markings in the two rolls of UN54 with which I have some experience. The one carried complete edge markings commencing with the current standard marking system showing it was OU02 (ORWO UN54). The second carried little information except that it was ORWO UN54. Filmotec informed me that the film marked OU02 is standard factory produced UN54 and have further informed me that it is produced to their standard perforation pitch of 2996. The film marked only ORWO UN54 was part of a special run and the perforation pitch of that was 3000. I was also informed that this was sold only in Germany and France. My experience of using the roll marked ORWO UN54 in an Arriflex SRII, which I found to be perforated at a pitch of 3000, was that it seemed to be just a little noisier when going through the camera. It didn't jam. I didn't notice anything unusual when I used the roll marked OU02. I appreciate that Filmotec have indicated that they produce their standard 16mm stock with a perforation pitch of 2996 rather than 2994, but I believe that this is such a tiny difference that it should cause no difficulty at all. I am therefore satisfied with the information provided by Filmotec to the point that I have now ordered some further stock. I hope this is helpful.
-
Further to my earlier posting, at the time of posting I had looked at only one roll of UN54 which I had had processed as negative, and it was the most recent roll I had shot. This had been supplied by a retailer and not directly from the factory. In point of fact, I had earlier used a roll which had been obtained directly from the factory, and so I checked the perforation pitch on that roll. I found that the perforation pitch of that roll was the same as Kodak 7222. I have since checked the edge markings of the two ORWO stocks and they differed. The roll from the factory quoted the international code for ORWO UN54 which is OU02, whilst the roll suppled by the retailer quoted simply ORWO UN54. That led me to contact Filmotec to enquire whether this was significant, and I have now heard from them to the effect that they completed a special run of UN54, the perforation pitch of which was R3000 (and not R2994), and had made some of this available to a retailer who had, in turn, sold it on to purchasers without showing on the label that the perforation pitch was R3000. So there we appear to have it. Some UN54 which is perforated at R3000 appears to got into the supply chain , and the roll I originally checked was some of that special run referred to. Hopefully all is now well.
-
Many thanks Dom.
-
Thanks very much for your response Will. Our colleague member Dom Jaeger (Australia) has very kindly offered to let me have one of these rings, and I am now just waiting for it arrive. Needless to say, I most grateful to Dom and very pleased to be able to acknowledge his generosity and help.
-
I have to say that my very recent experience with Les Bosher was outstanding. I live in the UK, some 120 miles from Les' workshop. I needed the mount changing on a Zeiss 10-100mm 3.1 lens from an Arri standard to an Arri Bayonet. I called him and arranged to go and see him two days later. He changed the mount immediately, checked over the lens, collimated it, and generously offered me a cup of tea! I was on my way home within 90 minutes. What more could one wish for?
-
As I said in an earlier posting, I found that ORWO UN54 went through my Aaton LTR54 and my Arriflex SRII without jamming, although I did feel the cameras were more noisy than normal. Having regard to the greater difficulty experienced by others, I decided to undertake a simple visual comparison of ORWO UN54 stock with Kodak 7222 stock. I laid a short length of ORWO stock over a similar length of 7222 and carefully lined up the perforations and then viewed the stocks through a magnifying glass. I found that there appeared to be no difference between the two stocks in relation to the gauge. Similarly, the positioning of the perforations in relation to the gauge of the stocks and the size and shape of the perforations appeared to be the same. However, I was very surprised to find that the distance between the perforations differed. By carefully positioning a single perforation on the two stocks, one precisely over the other, and then viewing subequent perforations, I found that that subsequent perforations went progressively out of kilter and over a very short length were completely out of step with each other. I then compared two lengths of each of the two stocks just to check whether my simple check was reliable. Each of the two stocks showed precise matching as one might expect. So this would appear to show that there is a difference in the distance between the perforations of the Kodak and ORWO stocks rather than a difference in gauge, which might explain why others have found that their cameras run for a short time and then jam when using ORWO UN54 stock Has anybody else undertaken a similar simple comparison and if so, with what results?
-
It is an interesting point Dirk makes about lubrication. I have used ORWO UN54 in both an Aaton LTR54 and in an Arriflex SRII. I didn't have any problem in either camera, but I did just get the feeling that in both cameras there was a little more noise than with 7222. Perhaps somewhat unusually, as a mere amateur, I film at 18fps, and I am wondering whether filming speed is relevant. If Dirk is correct with his point on lubrication, I am wondering if it could be that cameras are better able to handle non-lubicated film at lower speeds than at higher speeds and in my case they are just handling it at 18 fps and might not if I filmed at, say, 24fps. That having been said, in the light of other postings suggesting that there are problems with the perforation pitch of ORWO stock, I had a look at the pitch which ORWO use with UN54 and I note that this is said to be R2994. This is the same pitch as Kodak say they use on 7222. Interesting, or what?