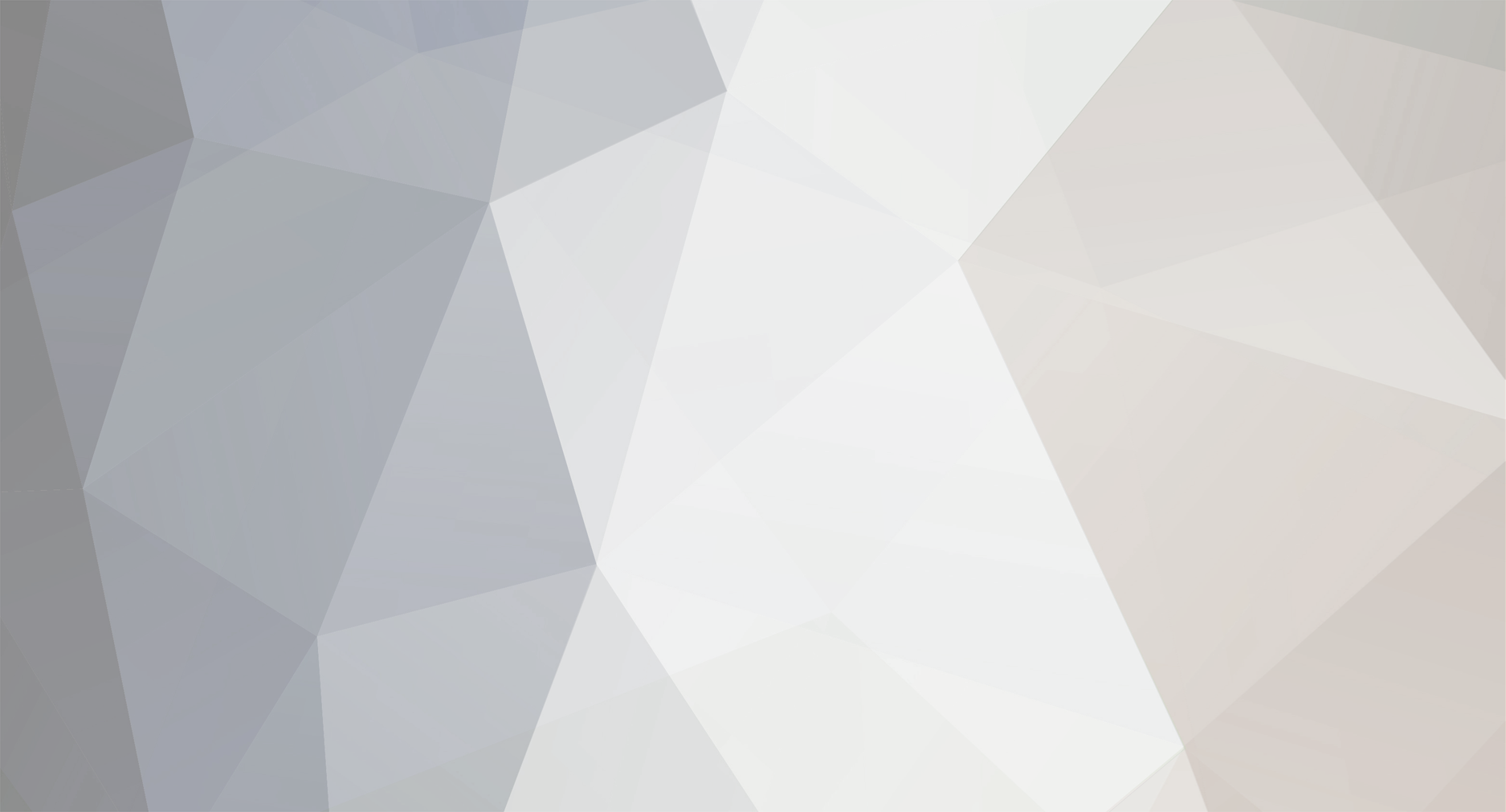
Clive Tobin
Basic Member-
Posts
402 -
Joined
-
Last visited
Everything posted by Clive Tobin
-
Hi, Sorry I can not give much encouragement on making more Arri S motors. We are making up a batch of 25 TXM-20Ba crystal motors for Du-All Camera. These fit the Rex-4, -5, -SB -SBM and similar spring wound Bolex cameras. When these are done we might make a smaller batch of the TTL time lapse motors for the same cameras. There won't be 25 owing the problems in getting more parts. None of these models are listed on the website any more. However if you go to the Instruction Manuals tab, you can read the instructions and get an idea of the capabilities. Cheers, Clive Tobin http://www.TobinCinemaSystems.com
-
Thanks for your interest. The last 25 took a long time to sell, so there is no chance we would make 100 of them, and only an extremely remote chance we would make any at all. Sorry but we are keeping pretty much fully occupied making our telecine equipment. We are finally (after maybe 6 months) finishing a batch of 25 TXM-20Ba crystal motors for Bolex for Du-All Camera. We are considering making up a smaller batch of our TTL time lapse motors for Bolex eventually.
-
New Tobin Telecines with Emulsion Side Scanning
Clive Tobin replied to Clive Tobin's topic in Post Production
Oops! This didn't get worded quite right. I meant to say that the Mainstream and True Speed models offer emulsion side scanning with base side scanning as an option, but the 3CCD Ultimate model is still base side scan. Sorry. -
Tobin Cinema Systems Inc. announces eight new models of telecine with emulsion side scanning as standard.* These include the newly named Mainstream, True Speed and Ultimate 3CCD models as well as the previously announced My Own Telecine units for the film hobbyist or small organization. Accepted formats include Super-8, Regular-8 and Dual-8 in most. Since we have heard little in the way of any actual rather than theoretical problem with the previous base side scanning, six of the models are still available with this orientation. We might mention here that in the well proven Elmo Transvideo machines, as well as in all 35mm theatrical projection, and projection of all 16mm prints contact printed directly from original film, the base side is towards the projection lens. The True Speed and Ultimate models offer exact 18.000 and 24.000 speeds, the same as the amateur filming rates. 18 and 24 are flickerless in NTSC, and 18 is flickerless in the PAL versions. True Speed operation has taken TCS some 25 years to develop, on and off. Running film at the right speed in the first place looks smoother than other methods where a computer inserts additional frames at intervals, causing jerky movement. Output signals on all are Y/C S-Video and Composite Video. On the Ultimate models, Component Video outputs are an option. On all models, you can connect directly to a MiniDV, DVD or VHS (etc.) recorder with no dependency on a computer or needing extra-slow running. Our simplified and perfected optical system has only a 1:1 macro lens between the film and the CCD. Eliminating the excessive and bulky optical components of old style "film chain" arrangements gives quality, with the 1CCD models, that is equal to or better than the quality with other 3CCD setups. By eliminating the projection lens, condenser lens, field lens, mirror, zoom lens and low-cost close-up lens this arrangement likewise eliminates the geometric distortion, color fringing, loss of sharpness, reflection of room lights, vibration and unstable position of other systems. * Technically you could say there are 16 models if you include both NTSC and PAL versions! These models can be seen on the TCS website at http://www.tobincinemasystems.com .
-
Blowout Sale on Arri S & M TM-23 Motors
Clive Tobin replied to Clive Tobin's topic in Cine Marketplace
Thanks! The blowout sale is now over however since there are now just a few left. We are however reverting to the old $375 price instead of $425. -
It has been years since I lived in Seattle, but the last I heard, Boeing had closed its surplus walk-in store and they were changing to just internet sales only. That would be no fun. It is much better to quickly browse through stuff to find things you didn't know you needed, and handle and smell the merchandise. I bet their sales are way down.
-
Not all double perf stock is alike. Some high speed cameras require stock with 2R-3000 (long pitch) perforations instead of the more common 2R-2994 short pitch film that is normal for making contact prints from it. Film prints are made with the original and print stock wrapped together around a rotating 40 tooth sprocket with the light coming from inside. Obviously the two films are riding on a different diameter so they shouldn't be the same perforation pitch. The correct pitch differential gives the best print quality. Irrelevant senior rambling: Someone at Boeing probably got a big bonus once for suggesting that they film everything with long pitch film even if it was going to be printed. Supposedly this was a cost saving in not having dual inventory. This likely led to all of their prints being somewhat unsharp and unsteady compared to how they could have been. You'd think that selling multi-million-buck gadgets would make them want to get their film prints as good as possible.
-
Also, I don't know if anyone mentioned this yet, but a "100 foot" spool of film actually has about 109 feet on it for loading and unloading in subdued light. So you can't get 4 full normal camera spools from a 400 foot core load.
-
Sorry our limited run of crystal motors is sold out. I do have a blowout sale however on the TM-23 variable motors for $249.99 as mentioned on the Arri sub-group.
-
The 5 stops that I am talking about in the instruction manual is the difference between shooting with the TTL time lapse motor, versus normal filming at 24 FPS which is effectively about 1/80 second. The instructions are furnished with each new TTL motor, and they are also posted on the website at http://www.tobincinemasystems.com/page30.html . The 3/8 second (or about 32/80 second) is ideal for stop motion work as it makes your 100 watt bulb equivalent to 3200 watts. The relatively slow motor speed enables the motor to stop quickly enough using dynamic (electrical) braking instead of a mechanical stop, so the TTL motor should work reliably for a very long time.
-
Hi, You may recall that owing to increased manufacturing costs we had to raise the price of the Tobin TM-23 variable speed motors for Arriflex S and M cameras from $375 to $425. Unfortunately I don't think we have sold any at the new price. To get our inventory down to an acceptable level we are now having a blowout inventory reduction recession depression bailout real estate collapse society collapse sale at only $249.99 to anyone in any quantity. This is less than the previous dealer price. When these are gone I think I can guarantee we will never make any more motors for Arri cameras, as they are not selling well and we are swamped with orders for our TVT telecine machines. We are already sold out of our TXM-22A crystal motors. You can buy directly from us, or I also have them listed on Ebay as Item 130263699526. We can take your credit card directly or Paypal. Shipping is extra. The catalog page is at http://www.tobincinemasystems.com/page61.html .
-
Thanks for your support. Owing to popular request here and elsewhere, we have made up another batch of the TXM-24 crystal control box for Bolex EBM, ESM and EL models. Included speeds are 24 and 25 FPS. The catalog page is here: http://www.tobincinemasystems.com/page61.html and as usual the instruction manual can be previewed also.
-
No, you are confused. As I said, this is specific to an HFC 2000' rewind crank, not to a camera. The HFC has an odd ratio, I calculated it once but forget, something like 4-1/7 to 1 or thereabouts. The Bolex 8-frame shaft moves 8 frames per turn, if you are going through the sprockets, and there are 40 frames per foot, so this would need 545 turns to crank through 109 feet. This is a lot more cranking than using a rewind.
-
If there are no sides it is probably on a core instead. If you are careful and have rewinds in the dark, you can wind it on to a reel or spool, and then wind it back again on to the final spool, to be oriented the right way round to fit the camera. If it is really 200 feet you will have to divide it between two 100' spools. If you are not experienced with handling core loads you should likely use a split reel, to stop the film roll from spilling, and also to convert from the 1" inside diameter of the core to the 5/16" diameter rewind shaft. A camera spool normally holds 109 feet, to give an extra 6 feet for loading and 3 for unloading. So one spool might wind up being full length and the other not. If using an HFC geared rewind, 109' corresponds to about 46-1/2 turns of the crank handle. While rewinding, you will of course be subjecting the film to possible static marks, picking up dust which will photograph on the film or maybe lodge as hairs in the camera gate, and fogging if the room is not totally dark. Empty camera spools can generally be had at no charge from your friendly local film lab. Check for bent flanges so the film doesn't catch and cause a film jam. Cheers,
-
We have made a number of crystal motors for Bolex over the years. They occasionally come up on Ebay. The TXM-22A crystal motor for Arri 16-S/M is back in stock and there is some chance we may resume making one or two of the motors for Bolex. The most likely to be re-animated (?) by Tobin Cinema Systems are the TXM-20Ba for cameras with the 1:1 shaft, and the TXM-26B for older pre-1966 cameras without the 1:1 shaft such as the original Reflex, Rex-1, Rex-2 and Rex-3. We also made a plug-in crystal for Bolexes with a built-in motor, such as the EL and EBM, and the ESM motor, but there doesn't seem to be much interest in these.
-
We have the latest batch of TXM-22A crystal motors for Arri 16-S and 16-M coming off the assembly line now, 5 are done now and the other 20 will follow soon. If you would still like one let me know, we can probably ship tomorrow. I am letting this group know first, before updating my web site. clive@webband.com www.tobincinemasystems.com
-
The latest batch is now starting to come off the assembly line. There are 5 finished right now and the other 20 should be done testing in a few days. So now is the time for everyone who said they would buy one to put their money where their, er, keyboard is. ;-) I am giving readers of this group the first crack at them, before updating the web site. Get 'em while they're hot.
-
Before the days of multitrack, everything was based around 35mm magnetic film. (Or 16mm for nontheatrical work.) The field audio was done on a Nagra recorder with Neopilot sync, using 3M Scotch 1/4" tape typically at 7-1/2 IPS but some people used 3-3/4 or 15 speeds. A visible and audible clapstick at the beginning of each shot enabled picture and sound to be lined up later in precise sync. Selected takes were resolved (transferred in sync) to 35mm "edit stripe" magnetic film. Music and effects were recorded "wild" (nonsync) on any handy 1/4" recorder and also copied to edit stripe. The 35mm edit stripe transfers were then edited into multiple rolls. One for actor A, one for actor B, one for actor C, one for crowd noise, one for sound effects, one for music, etc. An edit sync mark on the head of each enabled them to remain in perfect sync, owing to the sprocket holes and interlocked machines. The production reels were each normally 1000 feet or about 10 minutes running time. In many cases the workprint and dialog rolls were synced up with each other and serial ink edge numbered with matching numbers, in yellow or black ink, so in editing the sync could be maintained, and re-established if lost. The 35mm rolls were interlocked on multiple dubbers, perhaps a dozen or maybe more at the highest end mixing studios. These and the master recorder could all roll forward or backwards in sync with the projected edited work print. Typical equipment brands were Magnatech, RCA, Westrex and possibly others. The magnetic film was mostly 3M but other makes were also used. The sound mixer would preview the reel and play with the gain and equalization of each individual roll. When he and the director were pretty satisfied, they would actually record the master mix on 35mm fullcoat. In case something needed redoing, such as missing a manual volume change point, they could roll back to the point of the error and replace that part of the mix with an improved version. The master mix was mono, but on 3 tracks of the fullcoat. One for dialog, one for music, one for effects. For a foreign dubbed version, a 3-track copy of the mix could be sent overseas and they could use the existing music and effects tracks but come up with a local dialog version. The 3 tracks of the master mix were combined at equal volume levels to a 35mm optical sound negative, also mono. Preferred equipment brands were RCA and Westrex. The optical sound stock was usually Eastman Kodak but some people liked Agfa-Gevaert. The master mix had a self-adhesive "sync beep" applied to coincide with the "2" frame or else "picture start" on the countdown leader. The optical sound negative and edited picture negative are then both printed to color positive stock to make a composite print for projection. The sync pop is lined up with the appropriate frame of the picture negative countdown leader for printing, then advanced 20/21 frames to agree with the standard picture & sound head separation in the projector. The sound track area only is "applicated" in processing with a viscous redeveloper, to restore silver to improve the volume and signal to noise ratio when projected. This is my recollection of the process c.1970 but your mileage may vary.
-
Searching Crystal Motor for Arri 16ST for rent in Germany
Clive Tobin replied to Marc Roessler's topic in 16mm
On our 12 volt conversions, we put in a resistor and one or two capacitors according to motor vintage, and a transient voltage protector diode. Otherwise the torque motor and its blue arcing brushes put out too much static which can upset a crystal motor or even cause damage. Speaking of our Arri 16-S / 16-M crystal motors, the resurrected TXM-22A might be available in about a month. We have the internal motors and circuit boards now, and the metal parts are being done at the machine shop. -
Thanks, I know Ken well and he used to do our worm gear replacements.
-
These are the basic material for making the optical & magnetic sound version of our TVT-16 telecine equipment. These have a special sound drum, sound drum mount, switching, cams, etc. compared to the optical-only version that is in plentiful supply here. None of these parts are available any more. The heads are special and microscopic in size to fit inside the sound drum. Anyone know why B&H never sold these models in the USA? They gave up on 16mm magnetic sound domestically when they discontinued the old model 302 / 8302.
-
I have a continuing need for Bell & Howell 1693, 1694, 1698 projectors. These are optical-magnetic models of the TQIII (TQ3) series that evidently were only made for export and not sold in the USA. We don't use the original motor, lamp, lens, transformer, most circuit boards or worm gear so these can be bad or missing. A functional mag head and preamp would be nice.
-
Lots of H-16 non-reflex cameras are perfectly happy with single perf film. The beginning serial number that was factory set up for single perf is mentioned on a sidebar in my Identifying Your Bolex articles on my website: http://www.tobincinemasystems.com/page75.html
-
It has been a while since I have seen one, but as I recall the H8 eye level finder has double the magnification, and half the field of view, of the H16 one. So you would only be able to focus on the center part of the frame.
-
Shooting 4-6 fps? Possible with a intervolometer?
Clive Tobin replied to Norbert Shieh's topic in Bolex
So, instead of ancient 1970s technology it is based on ancient 1960s stepping motor technology that we evaluated and rejected for several reasons? Stepping motors by definition turn with small but violent steps, instead of turning smoothly. This is easily detected by your ear as a buzzing noise. This has the following drawbacks: 1. Constant flutter in the driving speed can be hard on the camera's gears. This has been demonstrated in the Arri 16-BL cameras when using the old governor motor. While not a stepping motor, it has the same "hitting" effect on the drive train, as it is constantly alternating between over and under speed at a high rate. It is known among repairmen that a 16-BL that has been used for a long time with the old governor motor is no longer able to take flickerless footage even when using a new type motor, owing to wear on the mirror shutter gear. This is an expensive repair. 2. The considerable vibration from the stepping motor can shake the camera and cause unsharp or unsteady pictures. 3. A stepping motor is an open-loop device instead of a closed loop servo. That is, the control electronics has no way of knowing if the stepping motor is actually doing what it is told to do. There is no simple means of providing an out of sync warning light. If the load is higher than anticipated, or the battery voltage is low, the stepping motor rotor will just sit there and vibrate instead of rotating as expected. Our smoothly turning motors can be seen on the website.