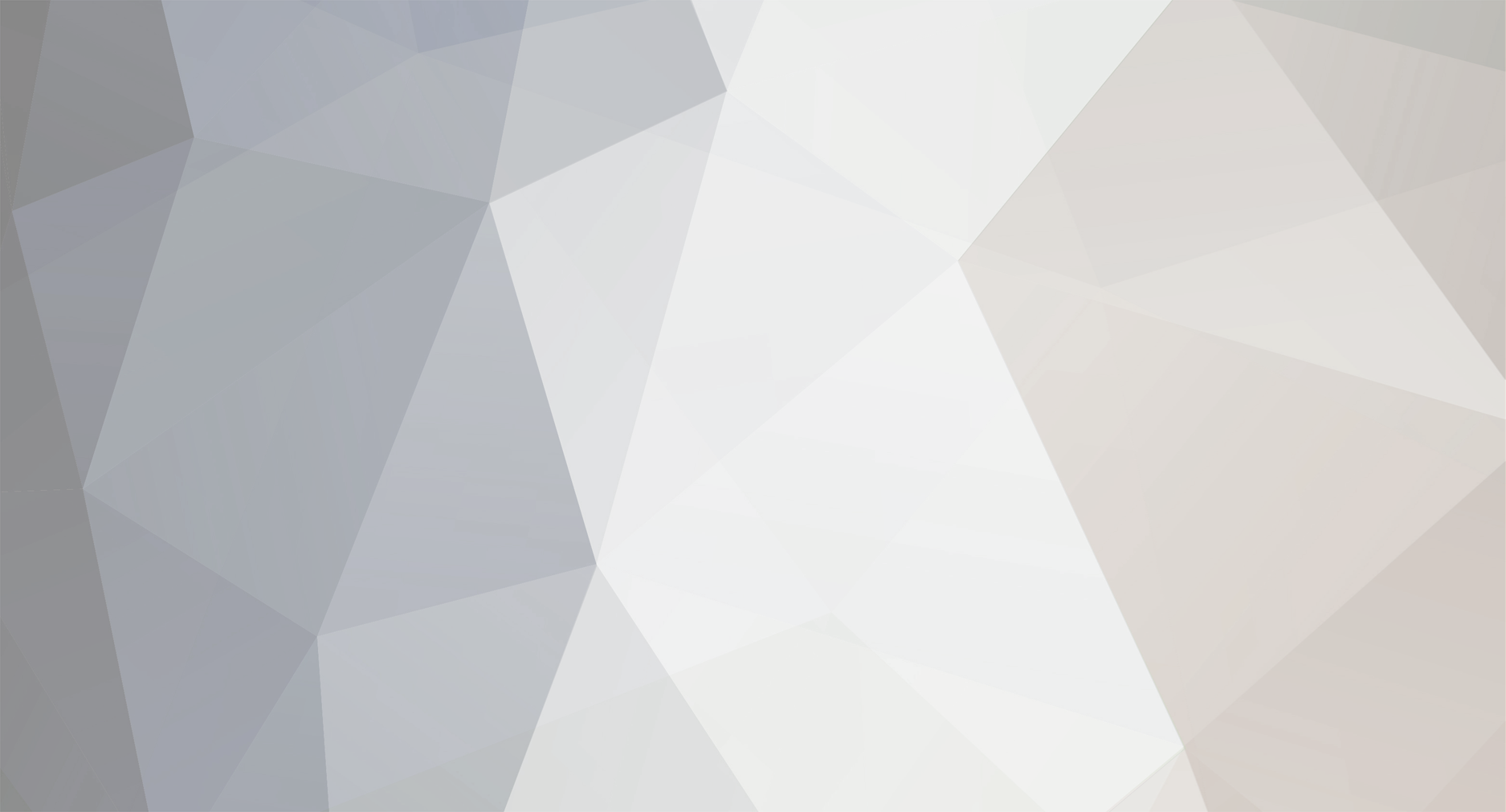
Dirk DeJonghe
Basic Member-
Posts
740 -
Joined
-
Last visited
Everything posted by Dirk DeJonghe
-
It is not common at all; you need a very decent budget to do that. Of course you only apply this to the final edit. If you live in the US, you may have watched this years SuperBowl. The CocaCola commercial 'America is Beautiful' (60 and 90" versions ) was shot on Alexa, digital DPX files were transfered to 35mm 500T 5219 stock (using only Super16 area) and then rescanned back to 10bit LOG DPX files that were sent back to the US by FTP. There is a version on Youtube but without the added film grain because Youtube compression doesn't handle this grain very well. The intention was to create a 'home-movie look'. Our client was very pleased.
-
Additional lengths with Orwo film, any experiences?
Dirk DeJonghe replied to Simon Wyss's topic in Film Stocks & Processing
The Kodak daylight 100ft spools hold 33 meters or 109 ft. Some clever people load their spools in a changing bag and can use all of it; 400ft reels hold 125 meters. -
Preservation for 8K Televisions?
Dirk DeJonghe replied to Jordan Newell White's topic in Post Production
A few years ago I attended a seminar on archiving etc at the Cinematek Brussels. A German professor of the Fraunhofer Institute spoke about resolution from a biometric point of view. He said: If you are seated in the best seats in a theatre where you can see the entire screen comfortably without panning your head, and if you have perfect vision (only a few percent of the population), then anything above 3K is no longer detectable by the perfect human eyesight. Imax is great for documentaries and some selected scenes in fiction. I saw one fiction in Imax by Jean-Jacques Annaud about Aeropostale (I think) and the visual information was too much to follow the plot. In a restaurant scene for example the viewer starts reading the menu on the table instead of watching the actors. -
Shooting 500T Film w/ Scoopic Maximum ASA of 380
Dirk DeJonghe replied to Joe Coleman's topic in Film Stocks & Processing
You will be fine, 7219 has considerable exposure latitude and most people treat it as 320 anyway (2/3 stop over). You will need an ND6 filter combined with an 85 if shooting outdoors with plenty of light.- 4 replies
-
- Canon Scoopic
- 16mm
-
(and 2 more)
Tagged with:
-
Nowadays most people use negative stock (colour or B&W). It can be transfered to digital HD format with very good results. Reversal film is only suitable for direct projection, but has much less exposure latitude. Also, you can still make very good projection prints from negatives, while making prints from reversal requires an expensive internegative since no reversal print film is available any more.
-
Will digital ever be as good as film
Dirk DeJonghe replied to Edward Butt's topic in General Discussion
When an Japanese engineer talks about improvements of his camera, he says it has 'improved clarity' compared to the previous model. Very rarely have I had fiction customer DOPs ask for more 'clarity', usually they talk about 'mood, tone it down, etc'. In the hands of a capable DOP, film is becoming what a fine oil painting has become, a unique art of expression. I now handle more artists films than commercial fiction films and they all 'create' something rather than 'capture'. -
If you look at a piece of film in its natural undeveloped state, you will notice that it is curling slightly, emulsion in. This is also the way the Aaton camera supports the film, The pressure plate on the base side of the film is slightly concave. This means that the emulsion is not really touching the camera aperture. Have a closer look at a metal tape measure and you will understand this natural curl also helps steadiness in the gate. This also produces less 'hair-in-the-gate' and less emulsion scratches because there is some air between the camera aperture and the film emulsion.
-
Mark, Triacetate base certainly shrinks, even more when stored at room temperature. Look up 'vinegar syndrome' and you will understand. I still don't think it is a good idea to run this film.
- 11 replies
-
- 16mm film
- panchromatic
-
(and 2 more)
Tagged with:
-
Any competent B&W lab should be able to process it in D-96. I would suggest you expose at 64 ISO, the film is going to be very fogged by gamma rays because of age. I wouldn't waste any money on it and buy some fresh stock.
- 11 replies
-
- 1
-
-
- 16mm film
- panchromatic
-
(and 2 more)
Tagged with:
-
Interesting label: it was made after the foundation of the German DDR (East Germany) and before the old Agfa in Wolfen changed its name to ORWO (Original Wolfen, the pre-war Agfa factory was located in Wolfen). Googling a bit should reveal its age. VEB means Volks Eigenes Betrieb, only used in DDR probably. Film can has some historic value, film will be heavily fogged by now, probably 60 years old or more.
- 11 replies
-
- 1
-
-
- 16mm film
- panchromatic
-
(and 2 more)
Tagged with:
-
'Paris, Texas' Cinematography
Dirk DeJonghe replied to James Malamatinas's topic in On Screen / Reviews & Observations
You were probably watching a DVD/Bluray? Anyway, in those days there were no Digital Intermediates, only normal Intermediates and Kodak Premier print stock was not yet invented. I don't know if Fuji Intermediate was already available then but a decade ago it was and if you made an interpositive onto Fuji Intermediate and the duplicate negative onto Kodak Intermediate, you got an extra saturated look. Back then DoPs would do lots of test with emulsions, make-up, lenses, filters etc to achieve the look they wanted. -
Go from Paris to Israel and back, 100% sure to have X-ray damage on your film if in checked luggage. I have seen it several times from several different customers. Zero problems with Fedex, UPS etc. They use their own freighter aircraft.
-
Don't put it in checked luggage.
-
I think he means 16-2R, perforated two edges, not 2 perf pulldown. I would add that the optical performance of most lenses goes down when stopped down more than T11, so in good conditions it is best to avoid 250D unless you carry ND filters. Heavy ND filters on the other hand make the viewfinder very dark, especially on Bolex-type cameras.
-
Tape splices (double sided) are OK for a limited number of passes in the contact printer wetgate. With more than three passes, the tape will start to stretch and you may have larger jumps at each splice, if even more passes the tape adhesive may become dissolved and the splice may open with possible damaged film. Scanners and optical printers with pin-registered gates are also problematical, if these printers get out of step with the perforations, they start to make new perforations at random, not usually in the right position. Workprints that are now 99% polyester are best spliced with tape, if you insist on splicing negative, it would be best to learn cement splices. I recommend the Hammann film cleaver/joiner for good clean splices. Do a couple hundred splices on practice stock beforehand.
-
Ektachrome/ECO to CRI green fade
Dirk DeJonghe replied to Joe Rubin's topic in Film Stocks & Processing
I could be that the formaldehyde was left out in the final stabilizer bath. Formaldehyde is not required in the ECN stabilizer but is required in ECO/ME4/VNF1/CRI processes. Some labs have been known to use common ECN stabilizer for all. Of course, you don't see the effect until many years later. Are you sure they are CRI (Color Reversal Intermediate) and not reversal dupes. CRI was used to make a new negative from a negative in one single step using special masked Ektachrome stock.- 3 replies
-
- CRI
- Ektachrome
-
(and 2 more)
Tagged with:
-
If you take off the motor, you will see what I mean.
-
In the days when the ACL was used professionally, it was well known that the flicker was caused mostly by a worn rubber connecting shock absorber between the motor and the mechanism. With age, this disk will get softer and the holes will grow larger. Replacing this shock absorber will solve many problems.
-
Optical film recorder or optical camera. Records incoming audio to optical negative on B&W sound negative film. Can be mono, Dolby analog (SR), Dolby Digital (SRD) and DTS; and Sony SDDS on 35mm, on 16mm mono only.
-
These tape splicers are strictly for workprint NOT for negative that is to be printed or scanned. Telecine would be OK with tape splices. We would need some more details on how you want to handle/finish the 16mm film in order to give best advice.