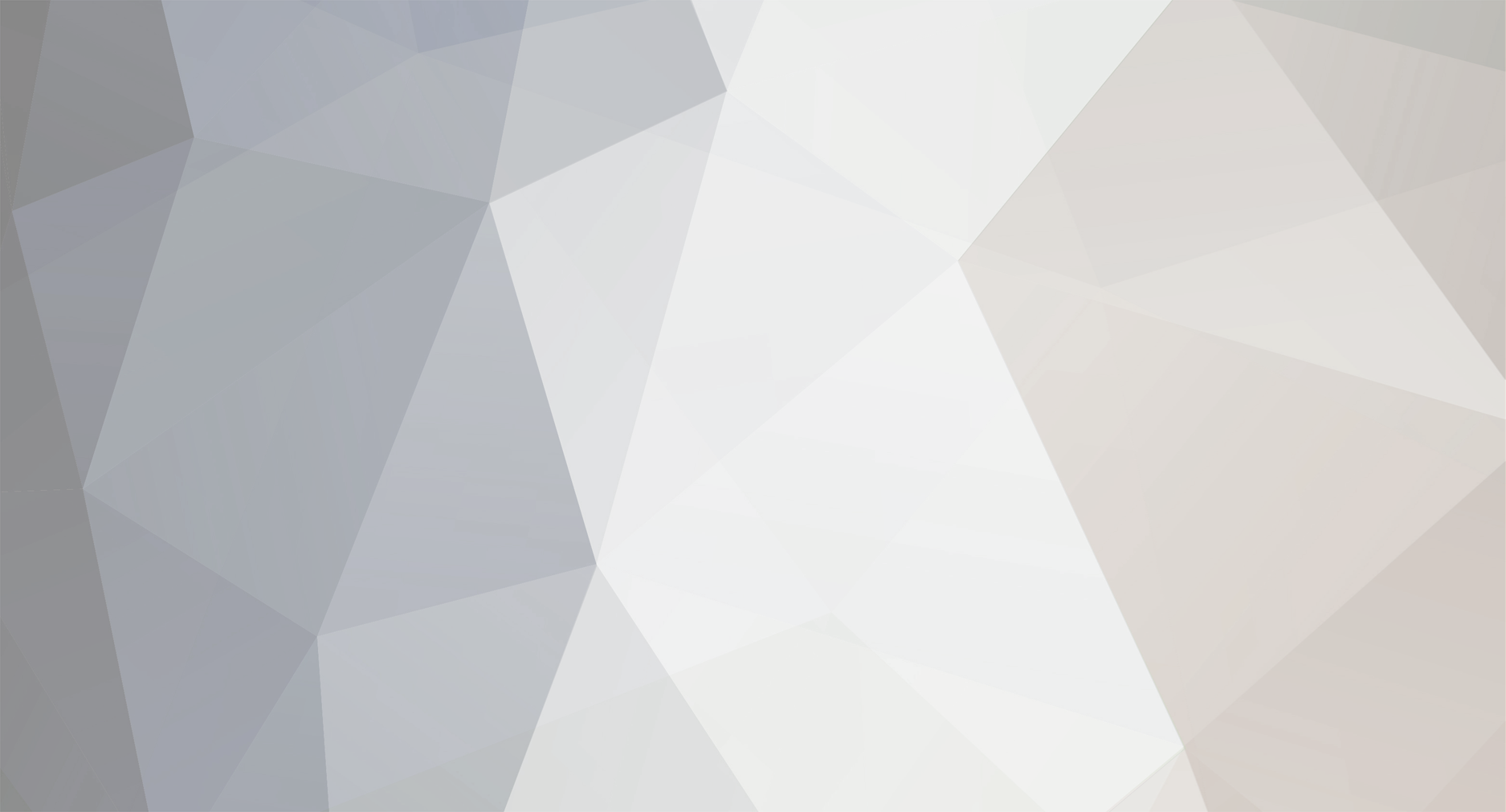
Steve Switaj
Basic Member-
Posts
141 -
Joined
-
Last visited
Everything posted by Steve Switaj
-
How Crystal Sync Motors work and modern sollutions
Steve Switaj replied to Tyler Fukuda's topic in General Discussion
This is fine. This is typical of the amount of flutter I would expect to see on an older camera. More modern cameras with a full resolution encoder on their motor and a tighter servo loop would have less flutter, but this is what every camera I used in the 90's looked like when you strobed it and and they were all just fine. Now you've got me curious about your technical details, are you using a brushed motor or a BLDC? Also, it sounds like you made your own speed sensor made of 4 magnets that pass in front of a hall sensor? Is that on the motor shaft? If so the Arri S has (IIRC) a 3x motor so that should give you 12 counts per frame, or a 288 Hz feedback signal, which should be plenty to close the servo loop. I have a Fries 65 on my bench right now that I'm working on rebuilding and it only has a 24 slot speed sensor (Though, when I rebuild a camera like this I usually integrate a modern 200 cycle optical encoder, which makes the servo loop waaay tighter). But yes, to answer your question, if you can get to the end of the roll and be on the right frame, it's a crystal motor. You don't need to be any tighter than that unless you are doing super long takes under some super-unusual discharge lighting or maybe doing 5 minute takes of an old CRT television. The original term 'crystal sync' meant that both the camera and audio recorder had an on-board reference and could work independently. Before that there was pilot tone, where the camera had a little tachmoter on the motor that generated a nominal 4800(?) Hz tone that was mechanically coupled to the speed of the camera. This tone was fed to the audio guy who recorded it as a separate track. This tone became, in effect, the perfs for the audio track. The camera might drift a bit, but so would the pilot tone, and they'd do it in sync. Later, in post where everything was held to 24 fps, the tape was played back with a player that kept so that the playback tone at 4800 hz regardless of what frequency it had originally been recorded at. If the camera was a bit slow, say only 23fps (or 4.2% slow), the pilot tone went to tape at 4600HZ. On playback back in the post house, the tape machine there would speed up the tape 4.2% to get the pilot tone back to 4800Hz, and the playback speed would magically match the film, now also running at 24fps. (there would be a slight pitch change, but unless you were doing music it was never enough to worry about) -
How Crystal Sync Motors work and modern sollutions
Steve Switaj replied to Tyler Fukuda's topic in General Discussion
Well, hypothetically, that's all it does take. Granted, it won't be all that elegant, but steppers are totally viable camera motors. Back in the day we used to use them on Mitchells at live action speeds all the time. I should note that as far as motors go, steppers do have an low upper speed limit related to drive voltage, but since you're talking about 1440 rpm you should be able to get that out of a smaller motor at reasonable battery voltage (say 24V). Unfortunately, steppers have a distinct noise while operating, a combination of the driver current switching and torque cogging. But if you're not shooting sync-sound, they work just fine. The best part is that steppers are not used closed-loop, which means no feedback or PLL. Instead, steppers are controlled by manipulating the current through two interleaved sets of motor windings. If you do this in the right pattern, you can get the motor to rotate in discrete steps with each change of drive current. As long as you stay below certain torque and speed limits, the motor will follow along with the drive pattern, which is a 4 step cycle (this is often electrically subdivided further in a process called microstepping for smoother motion). Better yet, most commercial stepper drivers handle all this internally, and you just have to supply two signals, 'direction' and a 'step' pulse, and the driver figures out the rest. Most commercial motors are wound to have 200 full steps, so if a microcontroller, say an Ardunio, can keep up with posting 4800 steps/sec, it can drive a camera at 24FPS (again, you can subdivide this into microsteps, but at 1440 rpm you're below the time constant of the motor and it really doesn't matter). Typically, someone programming this application will use one of the timers internal to the microcontroller to generate an interrupt at the right frequency, and the interrupt routine will generate a step signal for the driver electronics. Acceleration and deceleration phases manipulate the timer interval to ramp the motor up and down. Accuracy is limited to how accurately you can generate step pulses, which are derived from the timer, which is in turn derived from a crystal oscillator feeding the microcontroller (most Ardunio-like boards have a real oscillator because they need accurate timing for their UART ports). Some camera speeds will not evenly divide from a given oscillator, so sometimes you have to play with the timer interval for each cycle. Look up "Ardunio step motor shield". There are many manufacturers and they tend to have useful libraries for their boards. Even if you don't use them you can still examine the code for ideas (such as how to handle acceleration and deceleration) -
How Crystal Sync Motors work and modern sollutions
Steve Switaj replied to Tyler Fukuda's topic in General Discussion
By the way Tyler, here's some visual reference to what we've been talking about. This is an appnote for the ST L6234, a popular chip for driving BLDC motors. https://www.st.com/resource/en/application_note/an1088-l6234-three-phase-motor-driver-stmicroelectronics.pdf It dives pretty deep, but ignore all that for now and look at the figure 14 at the bottom of page 7. It illustrates a typical PLL application, like you'd find in an older camera. On the right side of the diagram is the motor. Attached to the motor is some device to sense speed. In this case it's a hall sensor, but in an older camera it would be a toothed wheel spinning in front of a magnetic pickup or a slotted disk spinning between a photo transistor and LED. The technology is not important. What's important is that this sensor makes a signal whose frequency is directly proportional to the motor speed. That signal is brought to the left hand side of the diagram where it is compared to a reference signal derived from a crystal oscillator and assumed to be accurate. The difference between these signals is the speed error. This error is applied as a correction to the amplifier circuit driving the motor, such that the motor speed is adjusted to match the reference speed. -
How Crystal Sync Motors work and modern sollutions
Steve Switaj replied to Tyler Fukuda's topic in General Discussion
I had meant to ask you about that. Do you actually close the speed loop with the hall feedback or is the motor torquey enough that you just feed it with the right drive frequency and use it as a synchronous motor, like a stepper? -
Before theater movies came on hard drives...
Steve Switaj replied to Daniel D. Teoli Jr.'s topic in Off Topic
One mile per hour, baby! -
How Crystal Sync Motors work and modern sollutions
Steve Switaj replied to Tyler Fukuda's topic in General Discussion
Also - What kind of camera are we talking about? -
How Crystal Sync Motors work and modern sollutions
Steve Switaj replied to Tyler Fukuda's topic in General Discussion
How much do you know about electronics? (Not meant to be a snarky answer, I'm trying to figure out how technical to be in response) -
Nolan to use new IMAX cameras on next film
Steve Switaj replied to Stephen Perera's topic in General Discussion
Well, yeah. I work in VFX and used Vista for 20 years, and I never saw it used outside of an acquisition format for effects work. Even if you wanted to use it as a production format, I'm not even sure what the post production stream would have looked like in the days before it was common to have a digital intermediate (conform the vista neg and strike a timed optical IP I guess? is that how they handled 3-perf? How do you do dailies when nobody can project it? I'm not an editorial guy.) In fact, I've been kind of shocked by the fact that vista made a resurgence in The Brutalist, although at least the advent of a full-digital post stream has made the format issue moot. But int he 90's, for effects, the advantages were obvious, in 1:85 you got 2.7 times the film area, which made a big difference since your image was going to degrade in post. if you were shooting anamorphic, you only got about 40% more surface area, but you got to use spherical lenses, which dramatically simplified things in the days when lens mapping kinda sucked. And all the while you used the same stock and labs as the main units, which helped a lot with logistics. But wow, the cameras were pretty primitive, especially getting into the very late 90's and beyond. There were about 6 or 7 "BoCams", which were conversions done by Greg Beaumont where he took the movements from ye olde elephant-ear Mitchells and put them in new spinning-mirror housings. They were pretty good cameras, about as close to 'workhorse' cameras as the format ever got, and those seven cameras were booked all the time. But they were kind of underpowerd and could have been more robust. They were basically the Arri-III of vista, they did the job but also screamed "1980!" The few 'lightweight' butterfly Mitchells were converted by Doug Fries to spinning-mirrors, and those were beefier than the BoCams, but even more dated. 'Lightweight' is a relative term, think 'small hippo'. Don't even get me started on the Technicolor conversions. On the few shows I used one it was really neat to play with a piece of history like that... but 'piece of history' is the operative term. We're talking a 100 lb camera with no reflex viewing. On the plus side, they were in no danger of getting knocked over by the pyro. There were a couple of machines from Geoff Williams which were more advanced. I used the W7 a lot. It was a beast of a camera and it could do something like 72FPS, which is a lot in 8-perf, but again, it was built with a triple dose of gravity. The only sync-sound camera I'm aware of is the W11, and I think only one exists. I've never played with it, and am told it performs really well, but it looks every bit as big, heavy, and cumbersome as the W7. See previous notes about gravity. These cameras all did the job, but they were horribly primitive compared to the cameras the main units were using. It didn't matter, because they were being tended by the VFX guys, but in general they were not received well by the 1st unit crews used to the 535 or Platinum, and all the accessories those cameras offered (like useful video taps, to start). Also, the demographic of the DP's was changing. The old guard that had started with Mitchells and was comfortable with a more primitive camera was aging out and being replaced with a younger cohort that grew up doing run-n-gun music videos. They liked tech, wanted familiarity, and were vocally suspicious of the olde iron. Something better (or at least something that seemed more familiar to the 1st unit) could have definitely found a home with the bigger VFX players that had their own camera departments, at least in small numbers. This is the market when the Rotavision cameras showed up in the mid 90's. It wasn't big, but it was big enough that it could have absorbed, say, ten or a dozen machines. I suspect that this is the market segment the (few) existing Rotavision cameras eventually served, VFX acquisition in foreign markets where you couldn't rent a BoCam. -
In the States, you can find 3/64" roll pins, which are 1.19mm https://www.mcmaster.com/products/pins/spring-pins~/diameter~3-64/ Don't know if they're available down under
-
Nolan to use new IMAX cameras on next film
Steve Switaj replied to Stephen Perera's topic in General Discussion
There was at least one of the Rotavision Vistas floating around LA in the early 90's. I was working at an F/X house in Burbank and the Rotavision rep brought one over for us to look at. This was 30 years ago, so the details are fuzzy, but if I recall correctly, it felt externally like a slightly fatter BL, but not enormously so. It was a lot thicker left-right, though. For loading, the top flipped open, like most Vista cameras. The film rolls sat vertically in the mag body, like a BL, but somewhere in the feed mechanism there was a turning loop that folded the film over 90 degrees to run through the movement horizontally. I think it might have been somewhere in the mag throat, because I don't recall a big loop in the body, like you'd have with the old technicolor conversions. I think the lenses were rehoused Canon still lenses, but like I said, 30 years ago, so... Anyhow, I do seem to remember that the camera had a follow focus motor built into the camera body that would engage the gear ring on the lens. There was a custom FiZ-like pendant for the AC and since the motor was on-board you always had remote follow focus available. This was actually a thoughtful feature in 1994, a time when Preston's FiZ-1 was the only real professional option and priced accordingly, which meant that us VFX guys usually did without. I think the camera had a rocky launch, though. I seem to recall hearing about one of their first US jobs being derailed by electronic issues over getting the many microcontrollers inside the camera playing together. In fairness, Rotavision was a small company and my suspicion is their US reps were just sales types and weren't technical enough to quickly respond to problems with their tech support 8 time zones away. Had their reps been better or their tech team been in LA it probably could have been ironed out quickly before the 'finicky camera' stories got legs. I've since been told that the teething problems were fixed and the cameras were used in Europe and, of course, in Australia, with solid service records. IIRC, Rotavison also tried to sell camera motors for Mitchells. -
I worked with a lot of this stuff back in the day, and most of the gear built after the early 90's (when digital electronics finally made it viable) used stepper motors, which were simply controlled to ramp up, run for a set number of steps, then ramp to a stop with the correct number of turns. There is usually a way to jog the motor slowly until you're at center-shutter-closed then zero out the count. As long as the accelerations are moderate and nothing mechanical slips, this is very reliable. Back before the steppers they usually used a geared-down synchronous AC motor, with a cam switch that would open after the right number of turns. You would close a switch that that paralleled the cam switch to start the motor, which would then turn the requisite number of times to shoot one or two frames, then the cam switch would open, stopping the motor. The motor would have to be timed to the camera when installed, that is, it would have to be installed such that it's stopped position was at center-shutter-closed. Assuming your animator friend is using some kind of video assist, they are probably familiar with DragonFrame, an extremely popular animation product. If they are, Dragon offers a couple of pretty easy ways to control step motors using an external Ardunio via their ARC Moco extension (conveniently already included in the base price). If you're doing animation, you kind of have to be picky about cameras. Many spinning-mirror cameras don't really seal out light all that well, and some tiny bit leaks around the shutter. For normal operation the film moves through the gate quickly and this is not an issue, but for animation and timelapse, where the film sits in the gate for a long period between exposures, you can have issues. You can use an external capping shutter, but then you can't see through the finder, so if you're doing serious animation or timelapse you want a focal-plane shutter. One of the go-to cameras for animation was the Mitchell standard rackover, which also comes in a 16mm version. These can usually be bought more cheaply than an S or M, because they are older and seen as an antique and less obviously a 'valuable' movie camera (Though, oddly, Mitchell standards were built into the very late 70's, long after the last Arri S or M rolled off the line) On the other hand, Will Vinten shot a whole lot of work back in the day on 16mm Bolex Rex's, equipped with step motors driven by Thing-M controllers. (Bolexes also having a focal-plane shutter)
-
I know this is a reference about Kamran not realizing the drive architecture was different between the 16BL and the 16S/M and we've gotten it all cleared up now, but I did want to offer up some technical notes for anyone out there who is contemplating building a crystal speed controller for an Arri 16BL, about how these cameras typically worked. I had one of these 35 years ago when I was new to the industry and pretty broke, and my friend also had one, and the Jensen crystal units were absurdly expensive, so I made my own crystal sync unit for them. It's actually a pretty easy task as long as the camera has the typical “regulated” DC motor (which most of them did) and as long as motor itself still works (eh...maybe?), because all the critical signals conveniently come out to one 12 pin Amphenol connector on the back of the camera (the connector itself is still even available new) The camera has a typical 12V brushed DC motor. The motor is connected to +V on the high side, the low side is switched to ground with a big TO-3 NPN power transistor, Base drive for this transistor is brought out to one of the pins on that external connector. The camera has a tachometer that generates an AC pilot tone when running, IIRC 4.8KHz. It's a reasonably robust signal if not loaded too much. This tach signal is also brought out to the external connector. There's some speed regulation circuitry in the camera that takes this tach signal and uses it to create a drive signal for the motor drive transistor. It's not really a PLL circuit the way we think of it nowadays, IIRC it's an analog circuit that integrates the tach signal and tries to drive it to match a voltage setpoint. There is no frequency reference in the sense that we'd use the term in a modern context, like a crystal oscillator, these cameras were good for, say, keeping between +/- 1FPS, but that was adequate for most purposes in the age of pilot tone. Here's the magic - the signal from this regulator circuit then comes out of the external connector, where it's looped back into the camera as the drive signal for that power transistor. The obvious intent was that a better, external, speed controller could simply break this loop and inject any signal it wanted into that drive transistor. Really, a pretty good and forward thinking plan from Arri from 1965. When the electronics go bad in these cameras it usually that regulator circuit drifting out of calibration. But that's OK, you can just ignore it, which is what I did. I built a circuit that took the tach output signal, and a crystal-derived 4.8K reference, and fed them into an old school PLL chip (probably a Philips 7046 family) which generated a PWM signal for the drive transistor. The circuit is really small. You can fit it easily into that L-shaped cavity in the back that used to house the now-obsolete magstripe circuitry, like Clive Tobin did. Most of these cameras came with a gearset for 24FPS, but some sold for European TV production have a 25FPS gearset. If that's the case you change your reference frequency. It worked really well, and that camera was a tank that made a super-stable picture. Even after I got an Aaton LTR I still used my 16BL for a decade of music video B-roll, since NTSC was 4:3 there was no downside to standard 16. I sold it in the late 90's, but I'd like to think that it's still out there somewhere and gets to run film once in a while ...
-
Matthew; Sorry I didn't see this earlier or I could have saved you a bit of trouble. Switchcraft still makes a 3 pin, male, right angle, chassis mount, XLR connector. It's their p/n W3M, and it's available for $15 https://www.mouser.com/ProductDetail/Switchcraft/W3M As you've discovered, the innards of these connectors are pretty interchangeable, if you need something other than 3 pins, you can buy the above part to get the right angle housing, and then by another standard cable-mount XLR male switchcraft plug, say, this 4 pin... https://www.mouser.com/ProductDetail/Switchcraft/A4M and swap out the contact blocks.
-
Static Electricity and Black & White Film
Steve Switaj replied to Tim Carroll's topic in General Discussion
Waaaaay back in college I earned beer money by shooting events for some of the local papers. It was all B&W still work, mostly B-level stuff that the staff photographers couldn't get to, stuff like local high school and college sports, often with a quick-turn darkroom session thrown in at the end of the day. We were in the northeast United States and it could get quite cold and dry in the winter. And of course, many sports are outside. On days like this if I was in a hurry rewinding the film (and it was easy to be in a hurry) , or I used the power rewind on my motor drives, I would often get little lightning bolts across my Tri-X. Also, for those who haven't seen it, inside an old 35mm still film cartridge, the end of the film was attached to the spool with an inch-long piece of paper tape. When I was in the darkroom I would always rip it off as quickly as possible because it would delight me by producing a visible green flash. It wasn't bright enough to fog bulk of the roll, but it did leave a pretty cool image of itself on the film right at the end. Didn't take much to amuse me back in the day, I guess. -
Arriflex SR2 Remote Trigger Options
Steve Switaj replied to Felix Finken's topic in Camera Assistant / DIT & Gear
Been a loooong time since I handled an SR-II, but does that camera have the B-family 11 pin accessory connector? If so, there's a run signal on that connector. According to my notes, the run signal is on pin 7, connect it to pin 11 (+12V) to run. -
> It states "Cannon" with an arrow pointing to the power input port. ITT/Cannon was the manufacturer. It's actually named after the guy who started the company in the 50's to make this style of connector. Switchcraft makes a modern version of this part, but all XLR connectors should be intermatable. Is there a run switch on the camera, or do you think it just runs when power is applied? Probably only two pins are used. You can figure out which pins are active with a multimeter, you'll probably see some winding resistance (probably a few ohms) between two of the three pins. If there's a run switch you'll have to close the switch. Polarity doesn't matter with an AC signal, assuming both sides are insulated from the metal shell (wasn't always the case with old power tools) . One trick for bringing up old AC equipment is to put it in series with a 100 watt tungsten bulb. That way if you have an issue the worst case current flow will be limited to 1 amp.
-
Yesterday i came across a documentary by the Museum of modern Art about their work with the earliest large-format movies made by American Mutoscope in the late 1890's. Mutoscope would eventually become Biograph, one of the most prolific producer of shorts and newsreels of the silent era, but in the beginning in 1895 they faced a weird problem. Founded by WK Dickson, the man who had invented most of Edison's early movie process, his American Mutoscope was ironically unable to use the existing 35mm perforated-film system he himself developed because Edison held the patents and refused to license it. So Dickson had to invent an entirely different system that used perfless 68mm film that was driven by friction. How they held the frame line, I don't know, but it worked well enough that they used it for several years, till the Edison patents faced legal challenges in 1902, when everyone, including AM&B, moved to the emerging 35 standard. The work was largely forgotten, but the Museum of Modern Art found 38 titles included with a large silent-era film library someone donated. The movies are amazing. The format is on 68mm film, and the images are huge at 51x46mm - about the size of a modern IMAX frame. Unique for the day, they were photographed at 30FPS Here's the whole doc... https://www.youtube.com/watch?v=BBNwiPgknn8 you can see a close-up of the actual film format on a light table at 3:22 Here's an - again, amazing - restoration of one of the typical shorts, "The Flying Train" from 1902. It's a 1:40 POV of traveling on the Wuppertal Suspension Railway, then inself cutting-edge technology that was only a year old. https://www.youtube.com/watch?v=2Ud1aZFE0fU As you watch it, again, bear in mind that it was shot in freakin' 1902 ! Alas, adopting the "standard" 35mm/4perf/24fps format after being able to do something like this was definitely a giant step backwards, but I can see where Biograph had to make its product compatible with the emerging theatrical standard (do I hear the echos of Laserdisc vs VHS rentals, anyone?). Anyhow, just for the sake of completeness, here's the wikipedia entry for Biograph. https://en.wikipedia.org/wiki/Biograph_Company
-
faulty 16mm scan_ camera or dev/scan issue!?
Steve Switaj replied to david jenewein's topic in General Discussion
This is a weird one. I don't think your light leak is happening at the turret or the gate, and I base that on how smooth and consistent the streak is on the second image. It crosses three frames and the two frame lines in between quite smoothly and is very even in density. This hints to me that the leak happened somewhere the film was in continuous motion. Around the gate the film is constantly speeding up and slowing down as each frame is exposed. leaks in this area tend to have a pattern that repeats with the frame spacing. I don't see any info on which model Bolex you're using, but if you're using an external mag, there could be a tiny leak where the body and mag join. The film moves at a smooth, continuous speed in that area. -
As someone who has handled a lot of weird cameras (I work in VFX) one of the things I love best about these forums is that no matter how far down the rabbit hole we go, there's always more rabbit hole to explore. - "Check out this obscure military format... " - "I'll see your weird format, and raise you a frame from 1897... " - "Hold on there Tex, you forgot about the big Russian machines... " - "Yeah, but look at this French guy who used paper negatives in 1888.... "
-
It all depends on how old you mean when you talk about "old 70mm film". As early as the mid 20's Fox Studios took the first real commercial stab at large format with a system they called Fox Grandeur. They had Mitchell make a handful of custom cameras that looked like expanded versions of their standard cameras. The film was 70 mm wide (yes, 70, not 65) and had perfs out along the edge. It was a 4 perf system, but the perfs were much larger than 35mm perfs. It was compatible with absolutely nothing else and died out after a few years. Skip forward to the mid 1950's for the "Widescreen Wars", an era where some of the larger studios tried proprietary large formats to differentiate their 'major event' films. This was the era of Cinerama and VistaVision, both attempts to improve the image but still use 35mm stock. A company named Todd/AO stepped into the fray with a 65/70mm format, called... Todd/AO. This was a system that used a 65mm camera negative with edge perfs identical to 35mm film. The image was 5 perfs high. Contact prints were struck on 70mm stock. The perf to perf spacing across the film was the same, but there was an additional 2.5mm of material on each edge outside the perfs. This was used for soundtrack. Todd/AO was originally shot at 30fps, and premiered on films such a Oklahoma, but the weird frame rate made it hard to sell 35mm prints for distribution in 'normal' theatres in secondary markets (because the projector gearing had to be changed), and eventually Todd/AO went to 24fps with everyone else. Eventually, Panavision adopted the same 65mm/5 perf negative to 70mm positive format for their large format systems and Arri eventualy followed with their 765 system (how many 765's were ever built? I've heard two?) However....... I would be remiss if I failed to mention that the US government had an entirely different large format film format of their own that matched nothing that anybody else ever used. If you handle a lot of old cameras you will occasionally see these weird old machines, usually in the form of high-speed instrumentation cameras from PhotoSonics. This was a *70mm* negative and there were two flavors, with perfs that could be either out on the edges like 'normal' film or closer to the center, like 70mm print film. (called type 1 and type 2, I don't know which is which) Frames were either 8 or 10 perfs high, so pretty square, for an instrumentation format instead of a theatrical format. The 'weird' film format is not as crazy as it sounds, 70mm with edge perfs is a standard format used by aerial survey cameras, which use long rolls of film, so the stock already existed when the cameras were developed.
-
So, is the deal that your power cable has two male 4 pin XLR connectors that both run individual cables into one (3pin?) Cannon connector that then mates to the camera? Do you have an ohmmeter of some sort? If so, open the backshell of the Cannon connector and see if the two (nominally 12 volt) XLR's are connected in series to make 24 volts at the camera pins. You can also open the XLR connectors by simply unscrewing the black cable boot back off the connector. With the boots and clamps loose, the XLR pin inserts will pull out from the back. Identify if pin 1 of one of the XLR's (call it XLR1) goes to whatever pin on the Cannon connector is ground. Identify if pin 4 of one of the other XLR (call it XLR2) goes to whatever pin on the Cannon connector is supposed to be +24. Does pin 4 of XLR1 connect directly to pin 1 of XLR2 without connecting to the camera? If so, then you have a cable set up to connect two 12 volt batteries in series to make 24v at the camera.
-
Don't know about the BL3, but the BL4 has two berg-chain type belts inside. The large main belt does most of the work, connecting the motor, sprocket, intermittent movement and mag drive. A smaller belt drives off the main belt, turning 90 degrees to drive the shutter. Here's a picture from Richard Bennett's website... https://cinemagear.com/blog/2024/08/16/arri-bl-4s-finally-on-the-bench/ Maybe you've lost your shutter drive belt?
-
I present the Hulcher 35 https://www.leitz-auction.com/en/Hulcher-35-Sequence-Camera-Model-112/AI-22-14420 Charles Hulcher was technician working for the NACA in the 50's when he developed a design for a still camera capable of taking quick bursts of photos. Hulcher eventually made a variety of models in 35 and 70mm, and they were quite popular with sports photographers well into the 90's, until they were eclipsed by digital cameras that could finally do more than a short burst https://www.theverge.com/2012/8/22/3260148/death-high-speed-film-camera-hulcher Depending on the model, some of the Hulchers had frame rates into the 50 fps range. I only once saw one up close, and never did quite understand how it worked. It was a 70mm version, the pulldown mechanism had a big swinging arm with a roller that would yank 8 perfs at a time through the gate, which apparently held the film there between pulldowns by friction alone (no need for register pins in a still camera) How did it get up to speed? Did the motor spin all the time and the mechanism clutch in and out? Was it driven by magic? Who knows? The Internet doesn't seem to have a lot to say. Ironically, the Hulcher in the first link I posted (mostly because it has nice clear pictures) seems to have the exact kind of sprocket drive we've been talking about. Ah yes, yet another obscure camera. My kind of thread.
-
>> I envision (driving the mag) cores to advance the film the distance between the film perforations Sadly, that's never going to work. Rolls of 35mm film are heavy, and have significant inertia. It's already a known problem with some cameras that the film gets sloppy slack when the camera is quickly tilted and the rolls in the mag want to work against the motion. Take a 200' short end, and palm it in your hand using your fingers to grip the outer edge. Now oscillate it back and forth an inch or so as quickly as you can. This gives you an idea of the inertia of even a small roll. You're going to have to fight all that 24 times a second, precisely moving it forward and getting it all settled down again in a 0.019 second window. And if you're doing it in the middle of a 1000' roll you're trying to do it using control points effectively 100's of feet away (you want to drive from the roll cores to position the film you're pulled onto the outer layer, but you're actually driving the entire stack of film via friction between layers, and those layers will slip) Then there's the physical properties of the film, like friction and stiction, which is going to vary by temperature, humidity, emulsion, hell, maybe the phase of the moon. Almost every camera I've ever seen has the film handling split into two parts for this reason, with an intermittent movement at the gate, and a continuous movement (some sprockets) a bit further back. The sprockets are there specifically to insulate the intermittent from the supply and takeup rolls, which operate at a constant speed. The intermittent, which has to have both speed and precision, is only handling a few inches of film at any given moment. The loops take advantage of the flexible nature of the film to bridge the difference between the two mechanisms >> Also for cost and size reasons the LCD shutter (which) exist and seemed to be at least feasible for what I envision. Oddly, even if you could make it all work otherwise, this would probably be the factor that killed you. Not because it's technically impossible - but because you will have to convince your DP's that is was OK photographically. A normal shutter is a physical thing. It's in the way, then it moves out of the way. When the film is being exposed there is no question the shutter is uninvolved in the image, at that moment it's just a lens, some empty space, and then the film. But an LCD shutter is an optical element that is in the light path at all times. Its sitting between the DP's favorite $20,000 lens and his film, and it's doing... something... to the image. Something that he won't be able to see till dailies tomorrow. Is it adding diffusion? Is it adding a color cast? Is there some reflection or flare? Is there a bit of dust on it - close to the film plane where it will leave a shadow? At the very least, we know it will be interacting with the lenses as an additional optical element, and, at this level of performance, even a perfect optical flat will have to be accounted for in the lens design, or you will see chromatic aberrations, especially with wide or fast lenses. This is why pellicle cameras never caught on outside some very narrow niches, even though they were very compact and quiet. This is why anyone who owns a reflex Bolex will see a notable difference between a “normal” Switar lens and an “RX” Switar, which is calculated with the optical properties of a reflex prism in the image path. Your camera will (effectively) be limited to using a list of 'approved' lenses or going out with a “buyer beware” disclaimer. And that will kill it commercially.
-
Well, assuming it is PosiDrive belt (which we don't know for sure, but it's a reasonable guess in a US-made camera from the 70's)... If it's 32 pitch belt, then there is a 'standard' 144 pin belt available. it would be 14.14" ( 359mm ) long, and is a stock item at SDP in the US for $27 https://shop.sdp-si.com/s7912y-c32af144.html Unfortunately, if it's a 20 pitch belt, 144 teeth is not a "standard' size. If it is 20p, then it would be 22.6" ( 574.5mm ) long Can you measure your belt (or at least get enough access to make a good guess)?