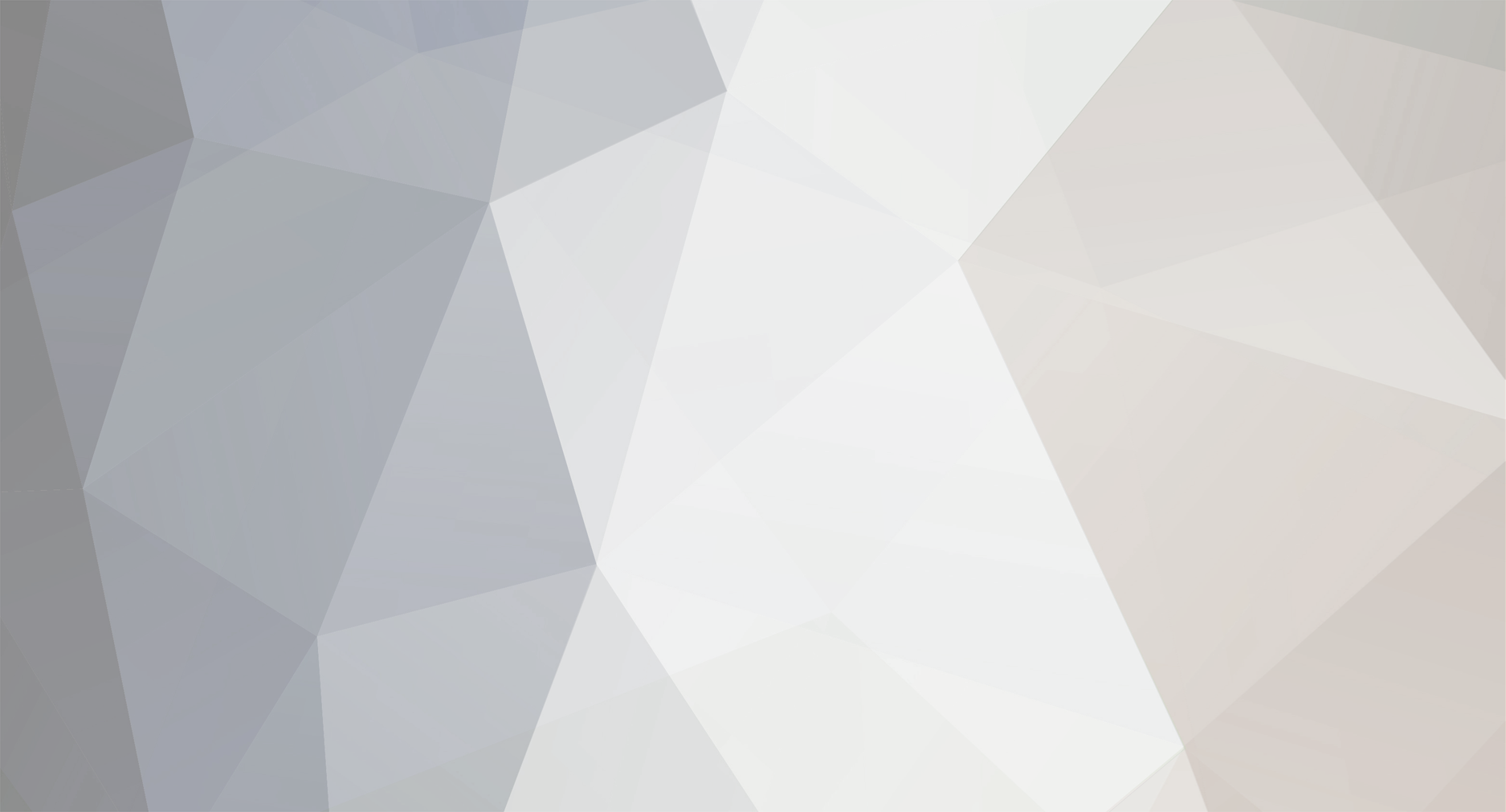
Dirk DeJonghe
Basic Member-
Posts
701 -
Joined
-
Last visited
Everything posted by Dirk DeJonghe
-
I don't see why the Vision 3 intermediate film could not be used on traditional IP/DN work. Don't do much IP/DN work these days but I was able to use the same recorder calibration as for 5242 so the contrast matches exactly. It is slightly faster with better whites. The Fuji RDI is specially designed for the Arrilaser because it has a non-standard green spectral sensitivity, Fuji still has the 4503 for traditional IP/DN and non-Arrilaser recorders. Kodak choose to go with one stock for both.
-
25 year old 7291 16mm - Verdict?
Dirk DeJonghe replied to Phil Thompson's topic in Film Stocks & Processing
Even if stored in a freezer all that time, it will have very high fog level due to cosmic radiation. Extremely unlikely to be still useable. -
Shipping unprocessed stock: X-ray concerns?
Dirk DeJonghe replied to Michael Mann's topic in Film Stocks & Processing
As a lab we receive exposed films from all over the world; There has never been a problem when a courier service such as DHL, UPS or FEDEX was used (after proper contact with the shipper clearly explaining the risk of x-raying unprocessed film). Some productions sent negatives from Djibouti, Hawaii, South America, Canada, North Africa, Japan, etc. Never a problem with these shipments; On the other hand, I have seen dozens of x-ray-damaged rolls that had been put in checked luggage, even if wrapped in leadfoil. Very unsafe; avoid at all cost. Hand luggage is a smaller but still existing risk. Processing locally is the best compromise, certainly if you are in a country with competent labs. I had a case recently with film processed in Israel, after investigation it turned out that the x-ray fogging was done before exposure, don't bring your raw stock in your checked luggage, buy it locally or arrange for safe shipping. -
RAW to screen after CC and oversharpen the image
Dirk DeJonghe replied to Markus Rave's topic in Post Production
Oversharpening is a common beginner's mistake, cannot be easily undone later. I would suggest you ask for a print of 30 secs to 1 minute of typical shots before committing the entire film. Depending on the filmrecorder, additional sharpening may be automatically added (unwanted). We commonly do short filmouts after every day of grading on a feature film, selecting some of the most difficult shots of the day. This way there are no surprises at the end, and everybody knows what we are getting. -
I think this method would defeat the purpose of maintaining the highest resolution since the telecine would first have to stretch the image in order to fit 1.37 to a 1.77 area. Squeezing it back to 1.37 later in post is not going to be a zero loss operation. I would suggest offlining it first and then scanning selects 2048x1556 on a real scanner, even a telecine direct to hard disk as DPX files would be better.
-
Shipping unprocessed stock: X-ray concerns?
Dirk DeJonghe replied to Michael Mann's topic in Film Stocks & Processing
The streaking showing on the vimeo clip is due to a maladjusted shutter in the camera, the film is being moved while the shutter is still open and exposing the film. This has no relationship to x-ray fogging. -
We are not in the UK but two hours from London by Eurostar. We do process and transfer to ProresHD HQ every day, direct to hard drive. Send us a sample and we can transfer to DVD or FTP.
-
I think the mechanical risk for the negative (properly spliced) on a properly operated 2K film scanner is less than on a wet gate contact printer or a optical blow up printer. Scanning 2K from S16 gives very acceptable results, degrain if necessary, A proper IP/DN blow up starts with a 35mm Interpositive blow up and a step-optical 1:1 DN. This will now cost you more than the DI route. We still do both the traditional blow up and the DI but since two years traditional is only requested for reprints, not for new productions. A direct-to-positive blow-up is very good quality but limited in the number of prints you can make and even the slightest effect such as a title is a hassle. No reason to scan from anything else but the original negative.
-
3D in process of going back from whence it came
Dirk DeJonghe replied to Phil Rhodes's topic in General Discussion
I can see it coming: "Watch this film is real 2D, no headaches!" -
Get a copy of 'The Negative' by Ansel Adams. You also need a spotmeter. I have several clients who were 'Video' DoP and who discovered 'Film' this way and they all liked it very much. If you can find a lab that will process and print ECN2 or B&W in short lengths you can leave out the home processing Ansel Adams describes. In Motion Picture work assume to have a fixed steady processing with fixed gamma instead of adjusting the gamma shot per shot as Ansel Adams would do with sheet film.
-
Agfa sold off their consumer products division to a German company called Agfaphoto, which went bust soon after. They only do B2B products now such as very advanced medical equipment, they are looking to apply their film-coating expertise to such new markets as low cost flexible solar panels etc, etc. Some of the major markets such as the US seem to have the pressure from the 'majors' to order one particular type of print stock and the labs have to use what the 'majors' dictate, regardless of price and quality. Stanley Kubrick for one always specified Agfa print stock. For a lab it is best to have as few print stocks as possible, every different stock requires calibration of picture and sound exposures, more short ends etc. By the time the calibrations are done for a new stock type, several thousand feet may have been used.
-
Our default print stock is Agfa CP30. When a customer asks for a particular print stock, we always try to do a blind test, using whatever stock he prefers, and Agfa CP30. Nine times out of ten he prefers the Agfa stock in a blind test. CP30 sits halfway between Vision and Premier in saturation and contrast, is more stable in the red channel during printing and has nice clean neutral shadows. The stock is specifically designed to work with Intermediate negatives. I like the combination of Fuji Eterna Intermediate negative and CP30 for my DI work. On my Truelight calibration it shows up as a straight line (combo recoreder and Intermediate neg). Agfa (a Belgian company by the way) still makes Color Print and Sound recording B&W stock for MP use; they still make color negative stock but only for aerial use.
-
Fuji Vivid 160t performance printed w/ no DI
Dirk DeJonghe replied to Gene Fojtik's topic in Film Stocks & Processing
Both Vivid 160 and 500 look very saturated and contrasty with deep blacks when properly exposed and printed. Both stocks don't support underexposure as well as the Eterna stocks. Underexposing and printing at lower lights will make the picture fall apart with muddy shadows and more grain. -
Generally speaking, manufacturers try to match the contrast of different speed stocks in the same film family. For example you can intercut Vision 3 7219 and Vision 2 7201 easily. On the other hand both Kodak and Fuji have 'outsider stocks for special tastes' like the Fuji Vivid family with extra contrast and saturation and the Kodak Vision Expression with intentionally lower contrast and saturation. Kodak has currently three different 500 speed stocks: the 'normal' 5219, the 'lower contrast and desaturated' 5229 and the 'snappier' 5260. So the conclusion is that variations in contrast are due to market demand and perceived taste of the times rather than film speed.
-
Sound negative stocks (both Kodak and Agfa) are processed in normal positive developer (higher contrast than negative developer). They can be run together with normal B&W positives but may need special processing times to achieve the aim density/gamma; Are processed in B&W negative developer: normal camera negatives, intermediate negative (5234), interpositive (5366). We run a combination processing machine with dual developer tanks, one for negative, one for positive, all the other steps are common. For similar size, B&W machines are much slower than color machines due to the much longer washing times and lower temperatures. If you would fill a color machine with B&W chemicals, it would be very inefficient, the machine would have to be slowed down to achieve the required washing times. Also B&W is a low temperature process at 21°C and you would need cooling to counteract the heating of the pumps. We used parts from an older color machine to build this B&W machine but an extra water chiller was needed with heat exchangers on the three main solutions. Also a good sensitometer and knowledge to use it is required in order to do proper B&W.
-
First, in the 20ies, there was black and white positive print film, containing lots of silver. The first soundheads for projectors had a cell sensitive to infrared because the silver in the film would stop the infrared light real well. No redevelopment of the sound track area was needed. Even today, B&W prints are still made the same way with a silver track. With Technicolor prints, the raw print stock was B&W sensitive and first the sound track was exposed then processed in convertional B&W process, dried and then CMY dye-track printed on pin-registered belts. Technicolor prints had a silver track even before the dyes were applied. With colour positive (ECP) there was a problem: after bleaching and fixing none of the silver remains in the emulsion and the infra-red sensitive cell in the projector would have a very bad S/N ratio. To solve this problem, a sound redeveloper (hydroquinonein a thick paste) was applied after the bleach but before the second fixing bath. This would prevent silver being removed by the second fixer but only in the soundtrack area. With the advent of newer 'red light' soundheads a switch was made to eliminate the soundtrack redevelopment since the projector cell would work well with just dye-track instead of silver-track. The new soundheads are backwards compatible and still read the old silver-tracks just fine. The elimination of the hydroquinone and wash water to remove the soundtrack paste from the film before it enters the second fixer is substantial and a very big ecological step. Between the silver-track and the final cyan dye-track there was an interim measure, the magenta track, with track application, intended to be readable on both old and new soundheads. The new cyan track is not readable on old soundheads. Since all 35mm projectors are supposed to have the new 'red' soundhead now, there is no reason to run the soundtrack application any more, except for 16mm as I noted before.
-
The track on positive prints used to be a silver track where a sound developer application was needed after the first fixer to retain silver in the emulsion. The silver was needed to excite the infra-red sensitive photocell as used in the older style soundhead as installed in the projector since the 1920ies. About 5 years ago the switch was made to equip projectors with modern soundheads with red LEDs as light source. Silver tracks were no longer needed, the new 'cyan tracks' did not need any additional processing steps and a lot of wash water could be saved as well. Currently, on 35mm cyan dye tracks are the only game in town, on 16mm silver tracks with applicator are still used but becoming very rare.
-
With the slow method you will also have the latent image fading to contend with, count about 1.5 printer points per 24 hours of aging, not necessarily the same in all layers. The end of your roll will be noticeably lighter than the beginning of your roll.
-
You can order print stock with 'positive' = KS or 'negative'= BH perforations from Kodak and Agfa and I suppose Fuji too. I can record to positive stock on my Lasergraphics P3 CRT recorder. This is why I ordered short pitch BH standard perforations for the print stock. It runs through the projector just fine, with just a little bit more noise. It takes about one hour to record one minute of film. I am sure you will get a picture if you put enough light on the film, but to get a really good picture that matches or exceeds anything else on the market, you will have a long road ahead, CRT machines have evolved over many years, I started with a Solitaire Cine3FLX 15 years ago and the difference with a modern CRT such as the P3 is dramatic. Cinevator uses a Arri-like film movement and a DLP-type image source. The machine also costs 1million Euros plus annual maintenance fees.
-
There is one very big advantage to polyester stock: fifty years from now, or fivehundred, it will still be there and not decomposed like acetate base with vinegar syndrome. I have a contract to do restorations for our national television network and some of the images and sounds (on acetate sepmag) aer degraded beyond recovery because of vinegar syndrome. Usually the images are in better shape than the acetate sepmag, even if they were kept in the same can. Another point: my negative cutter is pregnant, and she doesn't want to touch Kodak film cement since day one of her pregnancy. Kodak film cement contains dioxane and other stuff. It is used in minute quantities, but since it is written on the tin, she will be on 'sick' leave for about one year. Very expensive cement if you ask me.
-
As noted before, all prints stocks are now polyester except for B&W which can be acetate or polyester. For a workprint it makes no difference since you want to make single sided tape splices in the first instance, so you can easily undo your splice without losing frames. Also your magnetic sound stock needs to be spliced with diagonal tape splices on the back side only. The negative conforming needs to be done with cement splices, no tapes allowed there. Ultrasonic cleaning will soften the tape adhesive.
-
tonal range of b&w stocks: reversal vs neg.
Dirk DeJonghe replied to chris hoag's topic in Film Stocks & Processing
This discussion is a bit pointless. What will be the final output of the film? A telecine cannot recover the deepest blacks you can get on high contrast reversal film. Even a scanner will be problematic. A low contrast negative can be printed on various positive stocks and the positive stocks can be processed to different gammas. There are lots of decisions to be made here and it would be wise to consult both lab and postproduction people with experience in B&W. -
The current internegative stock, 7272 is really designed to work with low contrast originals such as 7252 ECO. This combination gives a nice contrast. If you use a projection-contrast original you will have better results with camera negative pulled one stop to reduce contrast. Both 7201 and 7212 work fine.
-
Shooting On Older Film Stock Question
Dirk DeJonghe replied to Stephen Tringali's topic in Film Stocks & Processing
Overexposing B&W negative is good advice because the stocks are rated a bit too optimistic by the manufacturers (not so with color negative). +2/3 will be about right to get the proper normal exposure on 7231 and 7222. On the other hand overexposing more than that will increase the grain in the filmstock and make it more difficult for the telecine to get the light through and this will increase noise. So, overexposing black and white negative is not a good idea. B&W negative grain increases with overexposure, the opposite of what happens with color negative.