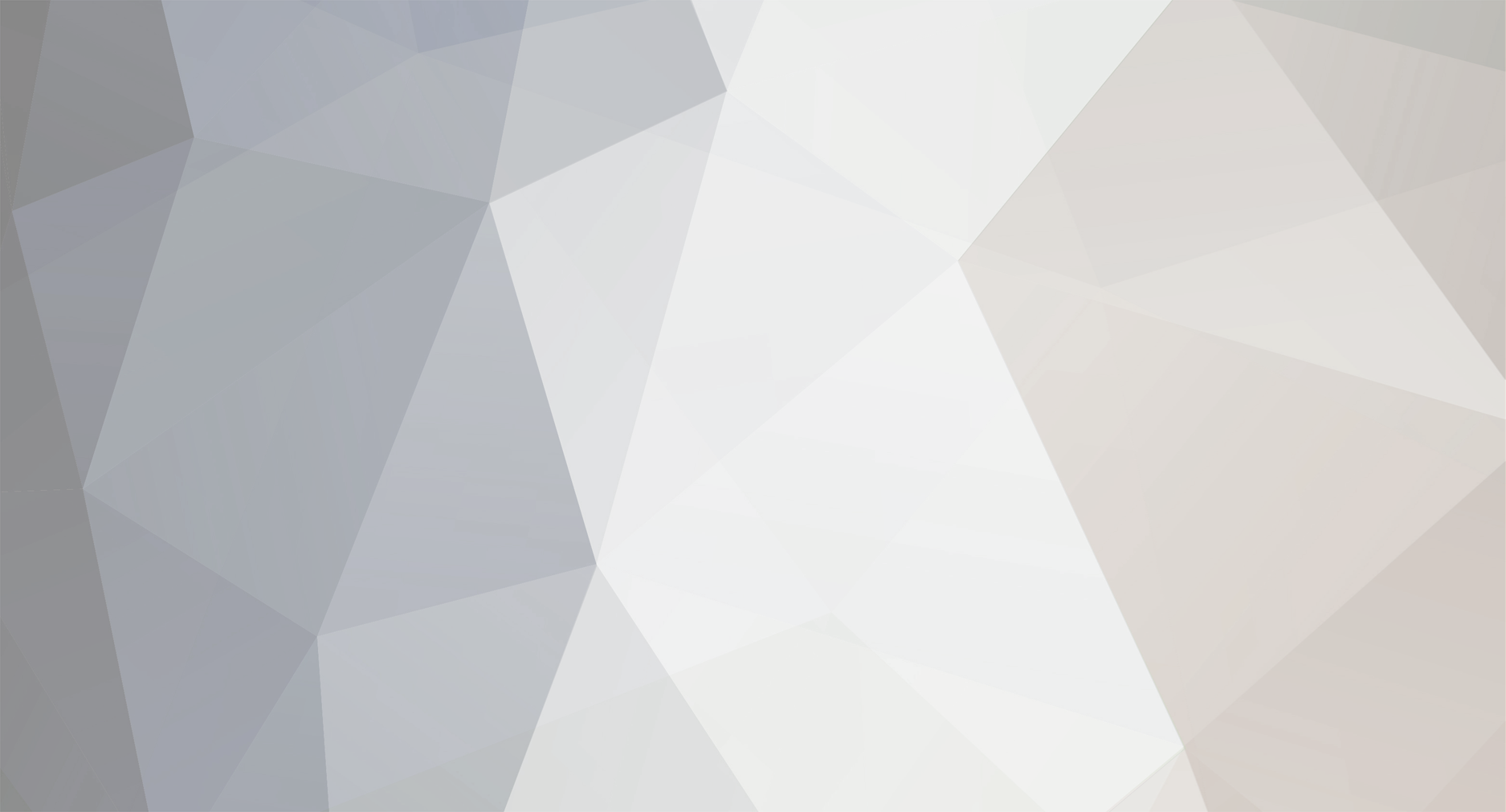
Robert Hart
Basic Member-
Posts
399 -
Joined
-
Last visited
Profile Information
-
Occupation
1st Assistant Camera
-
Location
Perth Australia
Recent Profile Visitors
12,828 profile views
-
Scott Stewart. Yes. The cameras with reflex viewfinders and angled spinning mirror shutters cannot be enhanced with a speedbooster suitable for the 16mm/Super16mm film area. When I converted a SI2K with a Speedbooster for the Blackmagic original cine camera, there was very little workspace between the rear element of the speedbooster optical cell and the inbuilt IR/anti-aliasing filter. Another option might be a groundglass relay system like Letus Extreme which can be tricked up to 2K resolution by careful alignment of the prism set to yield an almost 32mm wide frame with 35mm stills camera lenses. You lose contrast but the aesthetic is not entirely unpleasant. I tried a spinning groundglass system on a CP16R with a rough test. It is not well organised. The groundglass adapter in this instance only had an image frame 22mm wide hence less resolution from the 5micron groundglass texture. The letters DTC mean direct to camera without groundglass adaptor. What might be interesting would be to try a larger format focal reducer such as the arrangement made to convey medium format imaging to the RED DSMC cameras. From memory, these cameras had a fairly deep and confined throat from the lens mount to the sensor. The best bet is to live within the means of the available 16mm systems. Shoot slow almost grainless film using the fastest sharpest Super16mm lenses you can get your hands on. It can look sweet like 35mm film shot with a 35mm camera with lens iris at about f4. You have to live with the narrower field of view for the same shallow depth of field yielded by the same focal length.
-
Another possibility might be to make a custom support for the speedbooster's optical cell to fit within a film camera body with a separate lens mount in the front. The mirror shutter on some cameras is the deal killer. This was an approach I used when fitting a 0.71x speedbooster to a "Big" URSA camera. Fortunately the throat of the camera was threaded to accept an anti-reflection cone so it was fairly simple to make an internally and externally threaded cylindrical sleeve.
-
Best 16 mm Camera for shooting action shots outdoors
Robert Hart replied to George Hill's topic in General Discussion
If you intend using the Bolex for an action cam, be mindful that if it becomes self-agile and clocks you in the face, it will bleed you. If you take it up in an aircraft, attach a stout lanyard on it to pull it up short of stretching your pilot senseless if things get exciting. Be sure to tie the lanyard off to something above and behind you and of short length that it does not foul the controls. By the time you increase focal length to 25mm it will be shaky. You can grip it top and bottom, right palm upwards and beneath with fingers forward so you can work the run button which faces forward. You can shape your arms into a fairly effective faux-steadicam posture for handholding but this will require holding away shooting blind with a very wide lens. and a primitive wire gunsight style aiming device. Some folk have recommended the lenses with their own eyepiece. Be aware that they may shove your eye clear through the back of your skull if you run into something. -
The mystery has been solved. The film was titled "How Max Linder Travelled Around The World". It was filmed in 1910.
- 1 reply
-
- 1
-
-
For the sake of curiosity, here is a very short clip relating to scanning of one of two found reels of 28mm silent film from around about 1904. They were discovered on a rubbish tip in 1978. An attempt around about that time to view the film on 35mm equipment damaged the lead end of one of the rolls. The films were stored for some 30 years until I learned of them. The Retroscan Universal Mark 2 has rollers profiled for multiple film gauges and software presets for them as well. Following is a link to an earlier 2K scan of one of the reels. The film was substantially damaged and required all thermal splices to be repaired with fold patches over tears and scallops out of the edges. If anyone can identify the title of the film advice would be much appreciated so that we can give the film its correct attribution, appropriate safeguards and remove that watermark. All that is known is that it was by Pathe Freres.
- 1 reply
-
- 1
-
-
The new-old-stock Angenieux 17.5-75mm "compact" lenses which were sold by Whitehouse A/V out of inventory made for the CP GSMO do cover Super16mm. As Tyler points out, the older 12-75mm, 12-120mm and 10-150mm zooms do not. The long zooms vignette at the wide end and cinch in again at the corners between about 25mm and 35mm.
-
Long ago there was a rather primitive clockwork accessory which closed an iris. It was held immediately in front of the taking lens to generate a closing or opening soft vignette.
-
16mm film scanning - latest tech? information?
Robert Hart replied to Stephen Perera's topic in Film Stocks & Processing
Confirmation bias or buyer's remorse?? -
In shooting the close-ups with a wide lens with the camera closer to the actor, the sound guy has at least some chance of grabbing some decent intelligible dialogue. Too much dialogue these days sounds like it was delivered with the actor's face buried in his or her armpit.
-
faulty 16mm scan_ camera or dev/scan issue!?
Robert Hart replied to david jenewein's topic in General Discussion
There may be another remote possibility if the camera has been dismantled for repair. It has been a topic of past discussion. From vague memory, there are two seams where the castwork related to the pressure plate and gate fit into the case. I understand that the seams are covered with some sort of jointing material. My older H16 had a light leak which lit a streak onto the film between shots when the film was parked. The seams are exposed between the turret and the removable loading lid. -
faulty 16mm scan_ camera or dev/scan issue!?
Robert Hart replied to david jenewein's topic in General Discussion
Has the black bloop lamp enclosure on the bottom left near the turret been damaged and letting light in? It is possible if the optical viewfinder is not being used aftger set up on a locked off shot while the camera is running, for light to get in through the view pupil of the eyepiece and via the prism, laying a streak of light on the film? My memory is vague but I think there may be a selector lever on the top eyepiece relay tube to move a secondary mirror to exclude light if a human eyeball is not looking through the viewing pupil and thus blocking off any light from getting in. On a CP16R, there was an iris at the viewcup to stop light from getting in through an unattended eyepiece.. -
Another solution might be to optically copy to double 8 stock. That might get you frames 1 and 3 reproducing sequentially in the scanner set up for double 8 in one run then frames 2 and 4 reproducing sequentially in a second run. That would still leave you with the monkeypuzzle of how to reproduce all frames in a timeline in correct order. You might have to make do with frames 1 and 3 with playback speed correction from what would be a scan at half frame rate.- I think. The brain is beginning to fry in the effort of working this out. I don't know the Lasergraphics machine at all. It could probably be done on a Retroscan from a double 8 contact print made on a 16mm optical printer. Headache is looming from trying to imagine a way through this.
-
Something I had forgotten. The Cinema Products CP16R motion picture camera used another technology, a panel sliced off a piece of fine glass fibres adhered together. It had better viewability in lower light. At tighter lens apertures there were some chromatic artefacts which were of little consequence. A similar technology defined as "coherent fibre bundles" has been used instead of prisms or optics to flip an image upright for tube based night vision displays.
-
The facebook algorhythm takes one to all manner of places and this one popped up out of the blue. It is a piece by a young composer on the African continent. My first thought on hearing the clip play out was of a family friendly Hallmark film. As an underscore it is a good fit. The string players could tighten up a bit.