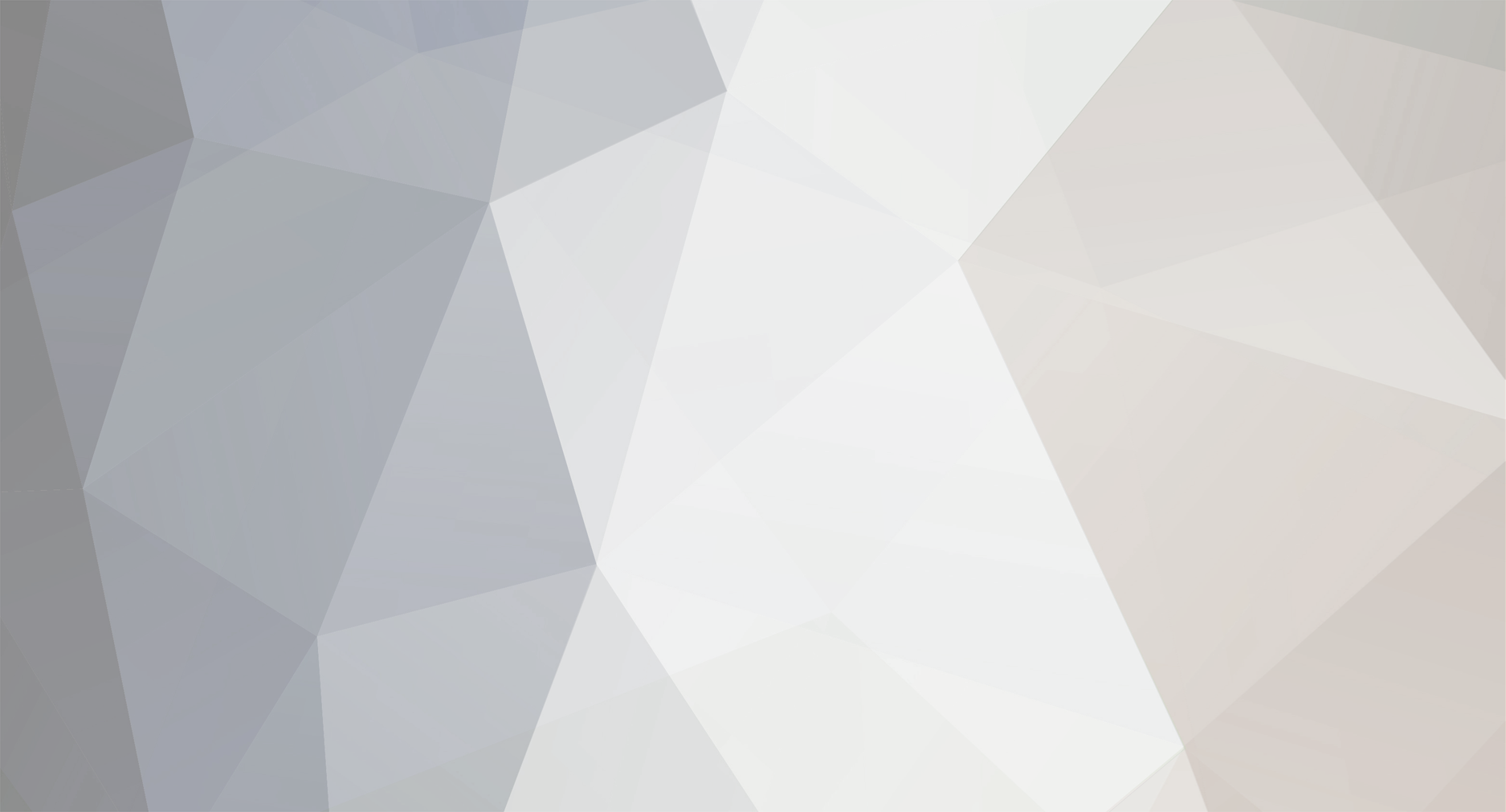
Charlie Peich
Basic Member-
Posts
278 -
Joined
-
Last visited
Everything posted by Charlie Peich
-
Zeiss SuperSpeed S35 Mk1 Bokeh Examples
Charlie Peich replied to Adam Brown's topic in Lenses & Lens Accessories
Adam, Check out Taxi Driver. Shot with Arri 35 BL and Zeiss lenses. Look at driving shots at :52 and at 1:08 in this trailer. It goes by quick. If you watch the complete film, you'll spot more, but you have to focus on the bokeh in the shots, not the story. LOL. Very subtle. http://www.imdb.com/...y/vi2571475481/ A DVD or Blu-ray would be the better way to see them. Great film! Charlie -
Better get a couple of 1000 ft or 1200ft (safer size to handle the 1000' roll) 35mm split reels. One of your rewinds should have a "tight wind" attachment on it and they should have drag adjustments. Winding the film too lose could cause "cinch marks" on the film before you expose it. Also, you don't want to put a loosely wound 400 ft roll in the camera, as it feeds out it could cause cinch marks when the film is pulled and tightens on the core, or torn sprockets when the lose, freely feeding film suddenly hits the proper tension applied by the feed spindle's clutch, especially if you're shooting high frame rates. Make sure to remove all the dust in the room you're doing this in. Charlie
-
Give Shurco Tool a call. Here's a list of Ground Glass Formats (courtesy of Stratton Camera) . They make GGs for Panavision, Mitchell and Arri. SHURCO TOOL COMPANY, INC. 744 EAST EDNA PLACE · COVINA, CALIFORNIA · 91723 (626) 966-8606 · FAX (626) 966-8608 E-MAIL shurcotool@aol.com
-
Greetings Erkan! I found a 1 sheet on the Uher Report - L in my files. It is dated 1967. I posted the front page below in low rez. The back side has a written description, specs and accessories. It would be better I send it to you in a higher rez scan as the type is very small. Do you want it? The Report-L was for radio stations and has no sync sound capabilities. I also found a couple of brochures for the Arrivox Tandberg if you would like them for your collection. I hope you weren't effected by the earth quakes. Regards, Charlie
-
Is this an Arri B-mount lens?
Charlie Peich replied to Veikko Niemi's topic in Lenses & Lens Accessories
Hello, It looks like it to me.......... not a Arri "factory" mount, but a copy. The Arri Bayonet and/or Arri B (the B for bayonet) -mount is the same. I think your question is, "Is this an Arri Standard mount or a Arri Bayonet / Arri B mount?" . Charlie -
Arri 16s 400ft torque motor conversion to 12 volt
Charlie Peich replied to Pete Von Tews's topic in ARRI
Flavio, The electronic components needed to reduce the 12 volts down to the 8 volts for the torque motor are: 1 - 5 watt 3 ohm wire wound ceramic resistor. Like this. This is for reducing the voltage. 2 - 103M ceramic disc capacitors. A capacitor marked 103M is a .01 uf +- 20%. I think the R stands for the rated voltage, and that would be 1000 volts. BUT, I'm not 100% sure on that. The ones in the photos below are 6mm in diameter. Someone else on the form may be able to interpret it, OR you could contact Clive Tobin and ask him. The capacitors are connected to the 2 brushes on the motor, then to ground. One capacitor per brush. They are there to reduce the electrical 'noise' given off due to the DC motor's commutators constantly making and breaking the circuit as they spin. If you viewed it while the motor was running, you would see small "sparks". This switching creates small electrical arcs which generate wideband RF. This puts "spikes" or "noise" in the otherwise clean DC current. This noise now entered in the current must have wreaked havoc on the electronics in Clive's terrific TXM-22 Crystal Motor, a brushless DC motor. Again, these capacitors suppress that noise so it doesn't interfere with the motor's electronics. I don't have a parts list for the torque motor or an electrical schematic for the wiring. Maybe Tim Carroll does, OR you could contact Mr. Tobin. The other thing you can do is, open the converted motor you have and copy what Mr.Tobin did. To do that, remove the 2 Lock Rings using external snap-ring pliers. Don't remove the large gear above the motor, that's the clutch. It's most like adjusted correctly now, but you may have to adjust it once you adapt the motor for 12 volts, or maybe you won't. Before you adjust it, make sure you have a full 400ft dummy load to run through the camera. Again, Tim Carroll may have some info or suggestions on adjusting it. Hey Tim, can you tell which direction the gears are set for? Forward or Reverse? LOL. Here's a close up of the electrical bits. That's about all I can add on this subject. Anyone else have any suggestions? Hey Tim, I've always handled my camera gear with care, I guess I have a light touch..... or I didn't work much... I can't remember which. Charlie -
Arri 16s 400ft torque motor conversion to 12 volt
Charlie Peich replied to Pete Von Tews's topic in ARRI
Hello again Flavio... Does the torque motor you have with the 12V TCS label look like this? If so, then you have a torque motor that has been converted to 12 volt operation by Tobin Cinema! You are good to go with the 12 volts to your camera, you don't have to make any conversions to the other magazine's torque motors. You do realize that ONE torque motor can be used on several 400 foot magazines? You don't have to have a torque motor on every mag, just take the motor off the spent mag, and put it on the next freshly loaded mag. Many kits would have 2 or 3 mags with one motor to be used between them. It was cheaper and it cut down the size and weight of the cases. However, if you are shooting fast and burning through 11 minuets of film and reload time is important to capture an uncontrollable event, it IS slightly faster reloading to have a motor on all the mags, one less step when changing the mags on the camera, and one less step when reloading the mags. Also, it's nice to have a back up torque motoer motor, but do you have a back-up camera drive motor? Have you checked the other motors to see if they have been converted? For your upcoming shoot, will you be loading 4 - 400ft loads at one time? Will you be shooting more that 1600 ft a day (44 minuets screen time)? Will you be doing 11 minuet takes? 3-5 minute takes? Will you have a loader to reload mags while you are shooting? Hand holding? 400 ft mags on the 16s add more weight and shakiness. A body brace would help. There are times when the 16s with 100 ft loads can be easier to use.. faster. But, it depends on what you are shooting. Charlie -
Hello again Flavio! The bellows matte box you'd want to find is the Universal Matte Box. I attached a couple of pages from the instruction booklet. This matte box will work down to the Zeiss small barreled 8mm lens, the original size, with 2 4X4 filters, Standard 16 only. It wont work for the Kinoptik 5.7. Do you have the Kinoptic metal shade for your 5.7? This is the only shade you can use, unless you make your own. No filters can be put in it. You would have to move up to the 6X6 MB-14 matte box in order to use filters in front of the lens and for the shade to clear the field of view for standard 16mm. You wouldn't necessarily need 6X6 filters, you could use smaller filters with the appropriate 6x6 step down filter tray. The MB-14 Wide Angle would be needed for Super 16. You could carefully tape a 4 1/2 inch round filter on the front without a holder, all kinds of risks to the filter involved. Kinoptic 5.7 or 9.8 Lenshade... (scanner art, some distortion) As for your 8 to 12 volt conversion on the mag torque motor, I had my motors converted by Clive Tobin. I don't think he is doing this any more, but maybe he will tell you what resistors you need and how to wire them in. I do know it's not just one resistor to drop the voltage from 12 volts to 8. Charlie
-
Flavio, Before Arri stopped making the 16s, they offered these "off the shelf" accessories to adapt the 16s to allow the use of the Follow Focus, the various sized Matte Boxes and lens supports they made that were being used on the 35mm cameras. It made it easier to use the newer and heavier long lenses and zoom lenses on the 16s. It breathed a little life into the 16s and brought it up to the current production methods, especially the use of the follow focus mechanism. You would need item 10 - "Adaptor plate" and item 11 - "Bridge plate BP-3 or BP-5". The BP-3 and BP-5 were for the 35-3 and BL-3, BL-4 cameras. These 2 accessories would line up or center all new generation Arri matte boxes, FFs and lens supports to the 16s' lens mount. This was for 15mm rods only. This also works for the 16M camera. Arri didn't make an adaptor to use the "Light weight support" (see the pic of the 16SR) system for the 16s that I'm aware of, you would need to make your own. By the time I discovered that Arri had made the Adaptor plate or riser plate, Arri had stopped making them, and I couldn't find that item anywhere in the States. Not many people or rental houses were aware such a thing existed, as the 16s had fallen way out of popularity by the 16SR. I did end up getting one as shown in the picture, and I was able to use my 16s with the 6X6 MB-14 matte box and FF-2, big lenses such as the Nikon 300mm T2 with 2x extender and Cooke 18-100 zoom. The assistants appreciated the FF-2 at least. However, this defeats run and gun hand holding with 100ft loads. The older 16s Universal matte box is fairly versatile. What lenses are you planing on using? Charlie Adaptor Plate / Riser Plate: Looks like a prototype Adaptor plate in this photo...........
-
Here you go Jacob, this is the "official" Moviscop user manual for free. As you will see, it was written for the advanced Movie Maker to use at home. Sadly, there isn't any repair or alignment info, or a parts list included. If anything went wrong, you sent it to an equipment repair house or distributor of editing equipment that dealt with Zeiss Ikon editing gear, or to Zeiss directly. There isn't much to go wrong with these viewers other than getting dust and hairs out of the prism mechanism. The plastic aperture plate would wear down, and that had to be replaced. This happened faster if you have the model that has the pressure pad as outlined on the last page of the manual. But, you really have to run a lot of film through it. I don't know where you can get parts in the States off hand, you might have to track them down in Germany. Look for film editing supply houses. Dust does accumulate on the prism and the lens located right below it, which really lowers the brightness and contrast of the image. Once you clean it you'll be amazed at the sharp image. If you understand the principles behind these viewers, are mechanically inclined and know how to clean optics, these aren't that difficult to take apart, clean and re-align. Charlie
-
Alex, Check out Clairmont Camera's Pinhole Lenses . Scroll down the page. You can put together something similar with, as Dan suggested, a port cap or with with available lens to-PL-adaptors. Charlie
-
yahoo Filmo fans group disapearred ?
Charlie Peich replied to Philippe Lignieres's topic in Bell + Howell
Some of the former bh_filmo70 members joined this new Yahoo group. -
Hello Karl! Actually it's the other way around. They are 2 different animals. The Harrison & Harrison Double Fogs were popular back in the '70s, especially in commercials, usually using the 1/8, 1/4, 1/2 and 1. Seldom used anything over the 1 for 16mm. The Regular Fogs put too much "halo" around the highlights, and you couldn't get them in lower strengths, 1/8, 1/4, /1/2. They acted totally different than the Doubles. Then that "look" fell out of favor. If you've never used them, I would do some testing to see how they act with today's film and transfers. Here is a description of the Regular Fogs vs the Double Fogs as written by Hank Harrison:
-
Hello Phil! Link to 16BL manual Good luck!
-
Flavio, 1st, your cables should be wired with the correct polarity to the camera. Looking at the back of the camera at the battery cable socket, the positive side is on the left, or the larger of the 2 pins. The Arri cable shows which side the positive is on. It's pretty simple. The way the cable is made for the Arri 16 S/B, there is no way to reverse the polarity when it's plugged in. What is important however is, the cable has to be wired to the correct pins in the connector on your battery. If all the above is proper, it won't matter if a Arri 8 volt "Variable Speed Motor" or Tobin 12 volt motor is used, the polarity is correct for both. Of the Arri 8 volt motors, only the WILD or Variable Speed Motor motor can be run on 12 volts. I have done that with mine. It's a simple, but tough motor without any sophisticated electronics to control the speed. You just rotate the rheostat on the back to set your frame rate while viewing the tachometer. When you shut the motor off, you may have to inch the the camera by hand to close the mirror shutter to view through the lens. Any of the other Arri 8 volt motors will not take the 12 volts, the popular Governor-controlled Motor that runs at 24 fps (there was a 16 fps version) is one that won't take 12 volts. From a 1969 instruction book: I was looking at a catalog for the earlier Arriflex 16 camera, not the 16 S/B, and the battery cable socket shown is different from the 16 S/B which I have. This view shows the camera without the cable lock as I show above. The polarity would still be the same. Apparently, the cable kept getting pulled out or falling out (if the pins weren't tight) while shooting, so Arri designed the cable lock. I'm not sure where in the serial numbers they added the lock, or if it was introduced with the S/B model. This could cause some confusion about cables. The pins need to be carefully separated periodically to insure a tight fit and good electrical contact. Too much pressure, or too big of a screwdriver, you'll break one side off. The Arri 35 camera motors had no cable lock, one just made sure the pins fit tightly. Is that the version you have? As I have no experience with that model, I'm not sure what Arri did to keep the polarity correct. It could have been done with 2 sizes of pins. I have a 35-2 A with the wild motor (part of camera collection and display only), and the pins are the same size. I don't have that much experience with the older models. The only thing that needs changing when using 12 volts and the Tobin motor is the 8 volt torque motor on the external magazine should you use one. Several voltage reducing resistors have to be installed. Tobin converted mine. It's not a simple in line voltage dropping resistor. At the end of Arri's run with the 16 S/B, Arri had converted the system to 12 volts. They offered a 12 volt Xtal motor, 12 volt Variable Speed and Governor Controlled motors, and sold the torque motors converted to 12 volts. Charlie
-
Hello flavio! Maybe I can help you with your power cable dilemma, or at least show you what you need. I have a 16S/B camera kit, with the "standard" or original Arri camera connectors. Here's some pics of what the camera end of the cable looks like: (This 1st series of pics is not an official Arri cable, but, I think, a Cine 60 version of the cable. Several U.S. companies were offering Arri S cables in the '70s) Note, the holes are different size for different size pins. This is to ensure the polarity is not reversed. This next view shows where the important grounding cable to the torque motor is inserted. The single wire had a small banana plug on each end. When using the 200ft or 400ft mag with the torque motor, Arri recommended that a jumper cable for the ground side be used to insure perfect operation of the torque motor. While the mag was grounded to the camera body, it wasn't always guarantied to have a good contact. In my experience, I kept everything clean and never had any problem when not using the jumper wire, but one was never sure. I also kept loosing the damn things. Here is what a new cable from Arri looks like. This is my spare that has never been used! The only thing I've done to this cable is to change the battery connector. This cable shows what the torque motor "jumper cable" looks like. (original Arri tape on the banana plug!) Connection at the torque motor Unless you modify your 16S body for another connector such as Du-all camera has done (you may have to e-mail them about a new camera connector modification), where does one find a original Arri connector? I would try Cine 60 and see if they have anything left. They may only offer it with a coiled cable, but you can always make an extension on the battery end. Other than that, I would look at ebay, or try some of the old rental houses in L.A., Alan Gordon, Birns & Sawyer etc. Another thing to look out for is the rubber connector that couples the motor to the drive shaft. If that is slipping, it won't matter what cable connector you have . Again, Du-all my have the correct fix. I know Tim Carroll on the forum here has some ideas, he's a craftsman with these cameras. Talk to him 1st! I have the Tobin TMX-22 Xtal motor for my camera. THAT is the only way to go today! Wish I had it back when I 1st bought my camera. The Arri S is a terrific little camera! Hope that helps, Charlie (I apologize for the cheesy arrows on the pics!)
-
Nikon Cine Nikkor Lenses
Charlie Peich replied to Michael Schroers's topic in Lenses & Lens Accessories
Micha, Take a look: Nikkor Cine Lenses More Nikkor Cine In a Alan Gordon Enterprises catalog from 1985, they list the lenses in C-mount only: 10mm f/1.8 $549 13mm f/1.8 $469 25mm f/1.4 $412 50mm f/1.8 $513 100mm f/2.8 $522 I don't see the lens listed in other major "professional" film suppliers, so, possibly AGE was the sole importer of the Cine lenses to the U.S. Charlie -
When did Colour Neg first become available in 16mm?
Charlie Peich replied to John Woods's topic in Film Stocks & Processing
1968 --- 7/5254 1976 --- 7/5247 This stock helped launched popularity of 16mm neg production and post production for printing. Kodak FIlm Chronology Charlie -
Jonathan... Here is the "official" Arri lubrication guide for the II-C. Use it in conjunction with the manual Rob linked.
-
Superior Bulk Film Company 8mm film tank
Charlie Peich replied to Toaristero Moumati's topic in Film Stocks & Processing
I think the tank you have is fixed for 16mm wide film. The regular 8mm film actually starts out as 16mm wide film, or as it was called "Double 8mm". It came in 25 foot length rolls, 16mm wide. After you ran it through the camera exposing 1/2 of the film or 1 side of the film, you flipped the roll over and ran it through the camera again to expose the other side of the film. When the film was processed, it was then slit in half to the 8mm width, then spliced together on a 50 ft reel. Check out this wiki explanation: http://en.wikipedia.org/wiki/8_mm_film Superior did have a super 8 version that was fixed at 8mm wide and could handle the 50 ft length. Here's a listing for the Super 8 version of what you have. It shows the Superior tank sold by a company called SOS in New York. Check the different dimensions between the 2 tanks. If you want to process Super 8 film, you'll need to get a tank that is set for that width, or is adjustable between 16mm and Super 8. I'm sure the one you have will not adjust down to 8mm width. The 8mm label on your tank is correct, as that tank is set for the double 8mm film (16mm wide) and holds the standard 25 foot reel. If the tank was for 16mm film, it would hold at least a 100ft spool and be able to take 100 ft of film. Hope that helps! Charlie -
Superior Bulk Film Company 8mm film tank
Charlie Peich replied to Toaristero Moumati's topic in Film Stocks & Processing
Hello Toaristero! Welcome to the forum. I copied a page from a Superior catalog from the late 50's early 60's that shows what I think is the tank you have, the "Powell Tank". Superior didn't date their catalogs, just used a number, so this is from Superior Cine Manual No. 58 (the 58 could have been the year). As I recall, Superior offered this tank for a long time. I have a couple of other catalogs that are newer, but can't locate them at this time. Sadly, there are no instructions for using this tank in the catalog. I do believe they offered a Super 8mm version in the late 60's. Love the statement: "Join the many thousands who are processing their own film". Hope that answers some of your questions. Greetings from Chicagoland! Charlie -
Who needs glasses to see 3D? Not this guy! Francois Vogel's figured out a way to remove those pesky spectacles from the equation, and he's ready to revolutionize the stereoscopic industry.
-
Mark, Are you printing your project, or going through a D.I. ? To back up what Francesco said, You'll need to change the G.G. and the Arri Glow mask from the N35 to the S-35 version. If the rental house set the camera to S-35, they SHOULD have changed the G.G. While looking through the finder, the G.G. identification ( depending on the format of the G.G. ) will show at the bottom of the frame. Example: T.V.Safe (S-35) will be printed on the G.G. , BUT, reference the Guide for the correct Arri markings. Arri Ground Glass Guide As for the "mask", for S-35 you want to use the "Universal" mask to take advantage of all the silver available. I use the ansi S-35 markings for the reasons Arri explained, use all the available silver. Charlie
-
70mm Projection...anyone with experience?
Charlie Peich replied to Brian Rose's topic in On Screen / Reviews & Observations
Brian, Check out this site, lots of pros there also. Film-Tech