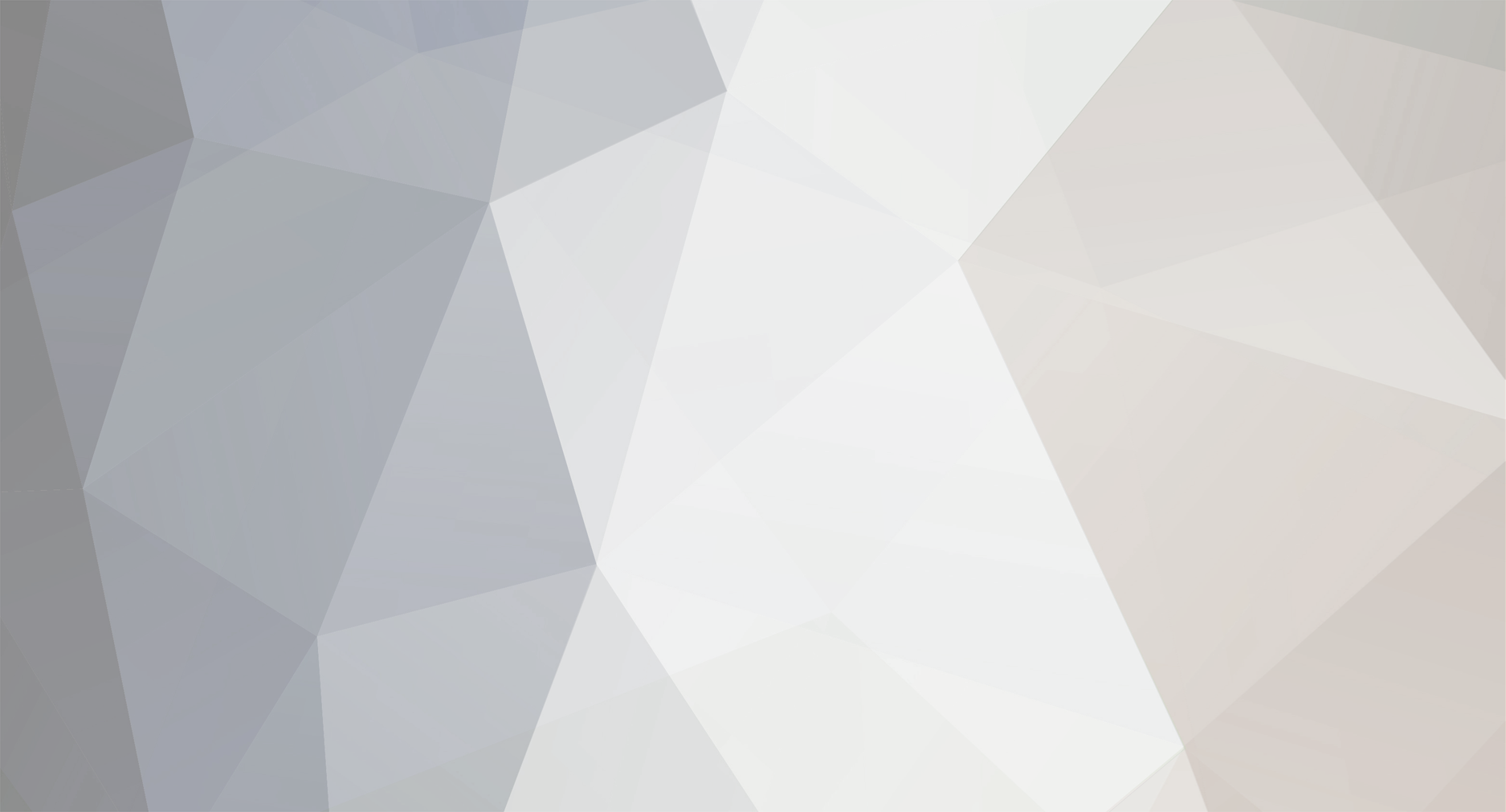
Brian Pritchard
Basic Member-
Posts
341 -
Joined
-
Last visited
Everything posted by Brian Pritchard
-
Thanks for the kind compliments. I am always happy to help, I have been in the motion picture business for 45 years so if I don't know the answer I can usually find someone who does. Brian
-
The numbers are obtained from a VCA, Video colour Analyser, and the numbers are fed to the printing machine by a punch tape, floppy disc or by a direct computer link. The three numbers send signals to the light valves in the lamp house telling them how much to open. You will find details of punch tapes and B&H lamp house on my website. http://www.brianpritchard.com/Model%20C.htm and http://www.brianpritchard.com/Punch%20Tape.htm I did post one of these links a week or so ago and apologise for doing it again. A well exposed negative should print at around 25 - 25 -25 although many labs have a setup that is slightly different from this. Brian
-
Film and Labs In Asia...
Brian Pritchard replied to Gary McClurg's topic in Film Stocks & Processing
If you check the Kodak web site http://www.kodak.com/US/en/motion/support/....4.27&lc=en they have a directory of film laboratories. It shows three labs in Thailand, only one of them processes 16mm. Brian -
Kodak stopped making nitrate film in 1951 but China and Russia continued to make nitrate until well into the 60's. Incidentally Russia sometimes cut 35mm nitrate down to 16mm so it is possible to come across 16mm nitrate. It is usually stated that 16mm is always safety. Brian
-
The Kodak formula R-9 for Bleach bath for B/W reversal is as follows: 1 litre of water to which add 9.5 grammes of Potassium Dichromate followed by 12 mL of Concentrated Sulphuric Acid. Brian
-
range of correction?
Brian Pritchard replied to Delorme Jean-Marie's topic in Film Stocks & Processing
I believe we are talking about different things here. If you increase printer exposure by 12 points as I have shown this doubles the amount of light which is the equivalent of one stop. If you are talking about increasing exposure on a colour neg by 1 stop you will increase the density of a point on the straight line portion of the curve by 0.6 X 0.3 = 1.8 which equals 7 printer points on the Model C scale (1.8/.025) so you would have to reduce the exposure on the printer by about 7 points to get the same density. Brian -
range of correction?
Brian Pritchard replied to Delorme Jean-Marie's topic in Film Stocks & Processing
1 printer point is 0.025 LogE - 12 printer points is 0.3 LogE (0.25 X 12 = 0.3) a change of 0.3 log E is a doubling or halving the amount of light which is 1 stop. The amount of density change will depend on the gamma of the stock being printed. 1 printer point changes an Eastman Colour print by a density of 0.7. Brian -
Unfortunately all the bleach formulae I can find that are suitable for reversal processing, contain Sulphuric Acid; the alternative to Potassium Permanganate is Sodium Dichromate but requires Concentrated Sulphuric Acid. I would be wary of using battery acid as you don't know whether there are any additives in it that might affect the film. It has been mentioned before and only recently, that you should take great care with concentrated Sulphuric Acid. Always wear gloves and goggles and NEVER add water to the acid always add acid to water and do it SLOWLY as the water can boil. If you are splashed with the acid soak the skin with water at once. Brian
-
range of correction?
Brian Pritchard replied to Delorme Jean-Marie's topic in Film Stocks & Processing
The usual method of grading is the Model C method. This uses RED, GREEN and BLUE light. You can have a maximum of 50 lights for each colour giving you 125,000 combinations. From 1 to 50 where 1 is the lowest light and 50 is the highest light. Each light has a value of 0.025Log E, 12 lights is the equivalent of doubling/halving the light or 1 camera stop. 1 printer point change in any colour is just visible to the trained graders eye. There are some diagrams and pictures on my website of the Model C lamp house http://www.brianpritchard.com/Model%20C.htm and there is also a diagram illustrating in which direction you have to change the lights to change the colour on the page about grading. http://www.brianpritchard.com/GRADING.htm When you are grading Colour Neg to Colour print you have to decrease the lights of the colour you want to increase. So if you want to make your print redder then you decrease the Red light value. I could email you some pictures showing the effect of 4 point printer changes if you are interested. Brian -
Cross processing ECN2 Negative in E6
Brian Pritchard replied to grant mcphee's topic in Film Stocks & Processing
Actually it is the emulsion that has the orange mask so removing the base wouldn't help! :rolleyes: Brian -
Home processing of b/w reversal film...
Brian Pritchard replied to Marc Roessler's topic in Film Stocks & Processing
Most of the silver halide that was originally in the film is either developed by the first developer and bleached or re-developed by the second developer, however a small quantity is left in the film which if it is not fixed out can leave a haziness in the film. Heavily re-exposing can also reduce the maximum density. These things only matter if you are trying to achieve the best possible results. Please take great care when using Concentrated Sulphuric Acid it is a very dangerous material NEVER add water to the acid and ALWAYS use gloves and goggles when pouring. Brian -
Don't forget also that an Interpos is a masked film so that it will give better colour reproduction than a print. Brian
-
You can calculate the gamma of the various Kodak film stocks from the graphs on their website of characteristic curves. For example http://www.kodak.com/US/en/motion/products...mp;lc=en#graphs gives you the curves for 5201. The left hand scale is density and the lower scale is Log Exposure. The density change over 1.0 Log E gives you the gamma. In the case of the red layer for 5201 the density change from Log E -1.00 to 0.00 is 0.5 to 1.10 approximately, giving a gamma of 1.10 - 0.5 = 0.6. These are general curves and do not apply to particular emulsions. Stock manufacturers use different ways to calculate the contrast of a film according to its purpose. Gamma is not usually used as it is just the slope of the straight line portion of the curve. It does give you an approximation of the contrast. Most film stocks fall into regular categories, camera stocks are around 0.6, intermediate films around 1.0, B/W Duplicating positive 1.6 and so on. If you push or pull process stocks you will change the gamma (contrast). Brian
-
Continuous processing machines for 16mm
Brian Pritchard replied to Richardson Leao's topic in Film Stocks & Processing
Over the years there have been many processing machine manufacturers, most have ceased business. Two of the major manufacturers from the UK are Calder Equipment and Photomec. Because machines are quite expensive £50,000 and upwards they are usually made to order and the customer's specification. The size of the machine depends on the process but mainly on the running speed. If you are running B/W Negative with a development time of 4 mins, a 1min rinse, a 6 min fix and a 6 min wash the wet area of the machine must hold 17mins of film. At 100 ft a min, an average sort of speed for a small lab machine, that is 1700 ft of film. So the size is determined by width of tanks and the required number of racks. A machine of this spec would be about 20 ft long by 8ft wide. Drying cabinets are usually quite big in order to dry the film at the right rate. Small machines are made. Both Calder and Photomec have made rewash machines which are about 10ft long by 6 ft wide. These can be modified to process B/W. I have seen machines as small as 6ft by 2ft wide using a mixture of water and methylated spirits in the final rinse to speed drying. I have also seen table top processors about 2 ft square. As I mentioned above these must run very slowly in order to get the correct development times. Quality is affected by using small machines because the quantity of chemicals, particularly the developer, is small and it gets exhausted quickly and it is difficult to get sufficient agitation to have even development. Brian -
Explaining the copy lights
Brian Pritchard replied to Max Hoever's topic in Film Stocks & Processing
I presume that you are interested in Grading and Printing Lights. I am sorry if I have misunderstood you. You can find some information on Grading on my website at http://www.brianpritchard.com/GRADING.htm. On that page there is a colour diagram that shows you what the effect of increasing the Red, Green and Blue lights for Colour Reversal grading and Neg to Pos grading. The Model C type lamp house which is the most common printing lamp house has three light valves which used to be mechanical and are now electronic. The white light from the lamp is split into red, green and blue light by dichroic mirrors and a light valve controls each colour before the three colours are recombined into the printing light. The valves have a range of 50 lights which can be raised or lowered by another 24 lights by means of trims. I could email you a picture of a lamp house if that would be helpful. Brian -
I agree with everything that Dominic says; also remember that for the last 60 years or so we have effectively used bleach bypass for sound tracks on colour film. The sound track area was re-developed to bring back the silver after bleaching. I have never come across any tarnishing of sound tracks. Brian
-
Actually 0.3 Log Exposure = doubling or halving of exposure which = 1 stop. (The log of 2 is 0.3010) Brian
-
The most important thing to remember is to allow the film time to warm up before opening the can after removing it from the freezer. If you open the can before it has warmed up you will get condensation on the film which will probably cause marking. If the can is unopened it will have been sealed by the manufacturer at the correct humidity, if it is an opened can try to make sure that when it is sealed up before freezing you do it at a low humidity. It is a good idea to put the taped can inside a plastic bag to stop it getting rusty. Brian
-
Apologies, I hit the send button too soon! The main problem is that B/W processes are not controlled the same way that colour processes are controlled. Each lab controls its process to its own standard using a developer formula that thy have modified. When features were being shot on B/W the cameraman would always do gamma tests with the lab of his choice so that they could both be sure that they were achieving the required gamma, usually 0.65. This would be followed by exposure tests. One of my first jobs in the Motion Picture Sales department of Kodak Ltd was to allocate batches of stock to productions when they had used up their current batch. This was to ensure that they received a batch that had similar gamma and speed to the one they had been using. Every batch was slightly different and might react slightly differently to the particular developer the lab was using. With colour stocks it is essential to make sure that each layer receives the correct development time to avoid crossed curves; pink highlights and green shadows for example. Kodak ensure that every process is as close to aim as possible by checking processes with interlab surveys. This did not happen with B/W processes; in addition there were B/W negative films made by at least half a dozen manufacturers which all reacted differently to the developer formula. Brian
-
B&W Reversal Processing.
Brian Pritchard replied to Stephen Smith's topic in Film Stocks & Processing
The edges of the film should be black; if they are not then your film could be fogged or it has had insufficient 2nd developing. I think that it is unlikely that you are giving insufficient re-exposure. It is possible to give too much re-exposure and I certainly would not re-expose in sunlight. Usually the 2nd developer is a fast working developer and unless there is a chemical problem I would suggest you might have a problem with your film being fogged before or during first development. Brian -
Kodak 7374 'Television Recording Film'
Brian Pritchard replied to Nick Mulder's topic in Film Stocks & Processing
I have a copy of the data sheet for this film: 'Eastman' Television recording Film 16mm coated on a grey base. It recommends developing in D76 at 68 degrees F: 5 mins will give a gamma of 0.88; 3 mins a gamma of 0.57. Developing in D16 at the same temperature will give a gamma of 1.47. It is sensitive to blue and ultra violet. It also says it can be used for making B/W release prints, having a speed between 5 and 10 times that of nomal print stock 7302. The datasheet is dated 1967. Brian -
I worked on the original neg of Knife in the Water about 15 years ago; I believe it was shot on Kodak 35mm negative film either Plus-X or Double-X. Unfortunately I do not remember which. If you have access to a 35mm print you might be able to see the original negative edge numbers which would tell you which stock had been used. We made a Fine Grain Duplicating Positive followed by a Duplicate Negative which was used for release printing. We only had the original negative for 3 weeks before it was returned to Poland. Brian
-
Coloured cores were used for many years but it was found that some of the coloured ones contributed to decomposition, both Nitrate and Vinegar Syndrome. There were some grey Ilford cores which actually decomposed themselves. I believe that the white cores used now, certainly by Kodak, are regarded as inert. Most film archives use only the white archival cores throwing away the coloured ones. Brian
-
What is the actual resolution of 35mm negative?
Brian Pritchard replied to Werner Klipsch's topic in Film Stocks & Processing
The usual way to measure the resolution of film and also film chains (printers, lens. projectors etc) is using MTF, modulation transfer function. You start with a pattern of sinewaves of increasing frequency with 100 % modulation, that is the black to white ratio. You then examine the pattern after, for example, photographing it with a camera, by using a micro densitometer and finding out the modulation for each frequency. As the resolution of the system drops the difference between black and white gets smaller until the pattern turns into just a grey area. You can plot modulation against frequency. Kodak film datasheets always include MTF curves. The system has the advantage that you can calculate the result when you have a chain. For example if your lens has an MTF of 50% at 200 cycles per mm and you use it to shoot on film which has an MTf of 25% at 200 cycles per mm the resultant image on the film would be 12.5% modulation. When you print your negative the MTF of the printer would come into play as would the MTF of the print film and then when you project the film the MTF of the projector/lens combination comes into the equation. At which point probably the MTF of our 200 cycles per mm pattern would have an MTF of 0%; you would not see the pattern. 5222 has an MTF of around 25% at 100 cycles per mm. One of the reasons for using MTF is that resolution varies with object contrast; 5222 has a resolution of 25 lines/mm at a contrast of 1.6 to 1 and a resolution of 80 lines per mm at a contrast of 1000:1. Brian