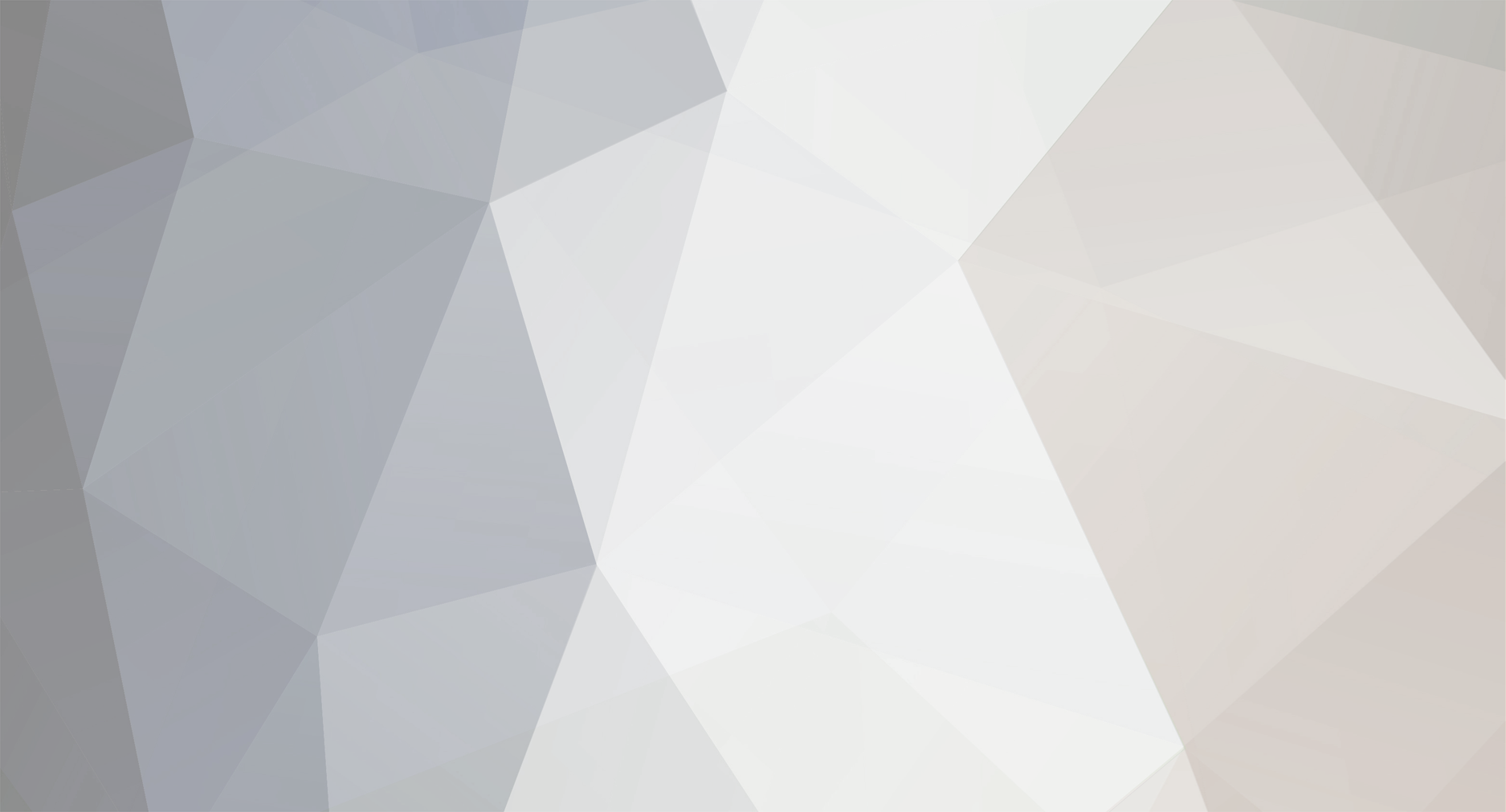
Steve Switaj
Basic Member-
Posts
141 -
Joined
-
Last visited
Everything posted by Steve Switaj
-
Arri 16SR - External variable speed control
Steve Switaj replied to Bernhard Kipperer's topic in 16mm
8 pin? Dunno about that one, but the Arri 11 pin is here https://flywom.com/support/support_files/Film camera accessory connectors.pdf -
Cinemax Macro C-802 Super-8 - Mercury battery
Steve Switaj replied to Mario Hatzopoulos's topic in General Discussion
Mercury batteries were popular in the 60's and 70's for photographic gear because they had a flat discharge curve and a long shelf life. So, basically, they provided a consistent voltage for a long time in intermittent use, and that's a good match for the demands of photo equipment. Though they were good at their job of being batteries, the downside was that oxides of mercury are very neurotoxic, and dumping all those batteries into landfills was... problematic. So... where do we go now? Well, first, there's no such thing as a 3.9v mercury battery. The basic chemistry of a mercury oxide battery provides a cell at about 1.35v, so as Joerg notes your battery is almost certainly 3 cells stacked in series in a common wrapper. It probably provided about 4.05v when new and unused, and settled in at about 3.9 v under it's rated load (little coin cells tend to have a pretty high internal resistance) Probably the best match for the voltage and discharge curve of mercury today is a zinc-air battery. These are the types of batteries you see sold for hearing aids. They have a little plastic tab on the top that you peel away to allow air into the battery. Oxygen in the air starts reacting with a zinc compound inside the battery and... well... it batts. They have an almost identical voltage, good power density, and a reasonably flat discharge curve, but they don't have anything like the lifespan of mercury. If you can get a good measurement of the battery size, you could probably improvise a holder for three cells. The thickness is the important part, you can always pad the diameter. Look here for common sizes... https://en.wikipedia.org/wiki/List_of_battery_sizes#Zinc_air_cells_(hearing_aid) Depending on how finicky your meter is, you might also be able to use three silver oxide cells. That would be a lot more convenient because silver oxide cells come in more sizes than zinc-air cells. Basic silver-oxide chemistry is about 1.5 volts/cell, though, so a stack of three is 4.5v. The extra voltage is unlikely to damage your equipment, any good engineer would build in a lot more margin than that, but depending on the circuit it may affect accuracy. Common sizes of silver oxide cells can be found here... https://en.wikipedia.org/wiki/List_of_battery_sizes#Silver_oxide_and_alkaline_cells -
Dom; What it the big blue camera?
-
-
There was one stab at making a modern sync sound VistaVision camera that I know of, built by an Australian company called Rotavison in the 90. It was a true fresh build, from the ground up. I played with one once, It seemed like a really solid system, but I never did see one “in the wild” so I don’t know if they ever sold any. It was really advanced, though, it did 72FPS and came with a selection of accessories that rivaled the contemporary 4-perf models. It used its own proprietary lenses, and included a drive mechanism in the body for remote focus and iris control. Like I said, I never saw one used, but considering the small fortune it must have cost to build up the prototypes with all their accessory systems, I hope they sold some somewhere
-
I spent 20 years shooting motion control and VFX and got very familiar with VistaVision. It was pretty popular from the late 80’s up to the mid 00’s. The same advantages that drove it in the 50’s were very applicable to its use in visual effects . Back in the day Vista had a logistical edge because unlike the 65mm, formats, labs in any big city could develop your dailies, and unlike early anamorphic lenses, the flat Vista lenses produced much more flattering results on actors at moderate and close distances. In the FX world of the 90’s You got a larger negative, but it still used 35mm film, which meant that you could use the same stock and labs as the rest of the units were using. Also the lenses were spherical. If you were working on an anamorphic show, you could have VFX plates with much less distortion. But since only one studio used it, there were very few VistaVision cameras ever produced, probably less than 20. The camera at the top of the page is one of Greg Beaumont’s VistaVision conversions. Greg was the in-house camera engineer up at ILM for many years (I think he’s still an active partner at 32ten). He built a couple of Vista cameras for ILM over the decades, but IIRC he had a side gig and built about a half-dozen of these “BoCams” on his own. They were used extensively in VFX work throughout the 80’a and 90’s Greg rehoused the original 1950's Mitchell movements in a new reflex body. The BoCams used Arri-III mags and were driven from below with what looked like a modified Cinema Electronics Arri-II base. They were good, simple cameras and ran well. If they had one weakness it was that the motor in the base seemed a little short on grunt sometimes, and without big batteries you could get into problems with rapid camera motion causing the film reels to drag inside the 1000’ mags which, in fairness, were probably not designed to run on their sides. Mitchell made a small handful of ‘real’ studio cameras, the “elephant ear” models you see in the old behind-the-scenes still from Hitchcock movies. They also built about 3 lightweight ‘butterfly’ models. Coming in at a svelte 17 lbs these were intended for MOS action shots. Rumor has it they were commissioned for the chariot races in Ben Hur. Additionally, Mitchell converted another handful of the old three-strip Technicolor cameras to shoot Vista, basically removing the complex technicolor movement and replacing it with an 8-perf unit. When I first heard of this it sounded crazy, but with only one strip of film to handle, the original boxes had plenty of space for the 90 degree turn, and all the other film-handling infrastructure was already done. I got to handle one of these Technicolor conversions at Bray studios in Ireland. It was BIG. I think very few of the original cameras survive. On the plus side, most of the small fleet got to shoot again in the 80’s and 90’s, but on the minus side, most of these cameras lost their original form, with the only movements being preserved and rehoused in “modern” bodies. Greg Beaumont did (I think) about 6 BoCams, while Doug Fries did two or three conversions. ( I got to rebuild the electronics on one of the Fries VistaVision cameras last year, I wrote up the story on Hackaday… https://hackaday.io/project/186456-vistavision-camera-electronics-rebuild ) ILM also did 2 or 3 reflex conversions they called VistaCams or something similar. I don’t know how efficient they were (they were some of the earliest conversions) but they were really cool since they had a neat fiberglass clamshell design to keep them small. ILM also famously modified a Nikon F3 with a registration pin in the gate and 30’ film back to shoot Vista-format plates inside small miniatures. Some of the other effects houses modified Stein cameras. The Stien cameras were really unique in that they were early stereo cameras from the late 20’s, and they used a unique 8-perf vertical pulldown that stacked two 4-perf frames on top of each other. If you turned that on it’s side… Vista. And then there was the W7. And I mean THE W7, since there was only one. It was built from scratch by Jeff Willliamson of Wilcam, for high-speed work and could crank at 100 FPS, so it worked on every single disaster FX film for two solid decades.
-
Rotary prism cameras in Openheimer
Steve Switaj replied to massimo losito's topic in General Discussion
If you ever get a chance, check out Trinity and Beyond: The Atomic Bomb Movie, by Pete Kuran. https://www.imdb.com/title/tt0114728/ I worked with Pete back in the late 90's, he used to own PMP, an effects stage up in the west end of the San Fernando Valley. One day in the late 90's I was shooting miniatures there and he walked out on the stage and started handing out DVD's of his pet project, which was finding and cleaning up archival footage of the atomic tests from the 50's and 60's. Turns out that Pete's dad was also a cameraman, and was involved in the national defense effort filming nuclear tests. It was apparently a big, organized thing that nobody talked about. The Department of Energy leveraged their proximity to Hollywood and maintained a technical facility up in the Cahuenga Pass and employed a small, secret group of working cameramen and technicians to staff it. Pete's dad was one of these guys. Pete says he remembers when he was a kid every once in a while his dad would mysteriously disappear for a couple of days without explanation to a "location project" he would never seem talk about. Pete always thought it was suspicious but only three decades later did he find out that Pop was driving up to Nevada to film big things going boom. Once Pete figured out the story it sparked his interest and he spent years digging around for the old footage of these tests and used downtime at his facility to clean up and remaster the film, eventually releasing it as two CD's He also dug up a lot of really interesting technical information - for example, he found out that Kodak manufactured special film for the bomb test that was kind of like color film, but it was actually three B&W layers that had wildly different ASA's - say 400, 20 and 1. The idea was that as one layer saturated, the next one would be reaching a good exposure window, and by printing it three times with different color filters to pull out the three layers of interest you could effectively get a B&W film with extreme dynamic range - useful for very bright events. -
Apparently, this lens was big with the stop-motion crowd in the 90's I worked on Coraline, and we received a lot of equipment from Nightmare Before Christmas and James and the Giant Peach, and the package included several of these lenses in the older 2-ring style. Apparently the older-school animation setups found them useful for their relatively close focus at telephoto lengths, which played well when compressing forced-perspective sets while still giving the animators some working room. By the time Coraline came around we didn't really use them any more. We were working in 3D, which eliminated forced perspective setups, and by that point we had too much camera motion that would have the game away anyhow. IIRC not a great lens wide open, but it cleaned up pretty well as you stopped it down.
-
I'm not familiar with the Arri S/B's. Where's the power connector? Is it a blind mate to that little metal pin at 7 o'clock on the motor face?
-
Buy some good screwdrivers before you start. You want the type gunsmiths use, with the ground, parallel sides. You can buy the kind with one handle and a set of 1/4" hex tip inserts to save some coin, but you want a set with a good variety of tip widths and thicknesses to choose from. If you use "normal" tapered screwdrivers from the home improvement store - even good ones - the blades will not fully fill the slots side-to-side and top-to-bottom and will concentrate force on 2 points at the top of the slot. Combined with the force need to dislodge some of the old fasteners, you *will* bung up these old, soft, slotted screws.
- 12 replies
-
- 2
-
-
- 16mm
- arriflex st
-
(and 2 more)
Tagged with:
-
By the way, that black thing the film runs through just before the first roller might be a timing light. A lot of these cameras were used for industrial measurement, so it was important to know how fast they were actually running (which was at best an educated guess). Many of them were equipped with a little neon bulb that would flash at a certain rate, say, 100 times a second, and put a steady timing pip on the edge of the film so you could measure exact event timing.
-
>> Well, I am afraid to tell you that... I don´t know what do you mean with framing camera. My WF 14 is basically this one: Cool! I have one of these in a box somewhere! Never did get to use it, sadly. Anyhow, there were a few different options for the drum cameras, they were available as "framing" cameras or "streak" cameras. Framing cameras... well, they basically make individual frames, like normal film cameras. They are for high speed cine work. Streak cameras, on the other hand, move the film continuously behind a thin slit. This is useful for certain technical applications where you're photographing linear motion. It's basically a long still photograph *of* time going by, but it won't make sense as a movie. One common example of streak photography is the photo finish camera at a horse race track. Check out this cool write up for more insight into how it works... https://www.donttakepictures.com/dtp-blog/2019/5/8/winning-by-a-nose-the-history-of-the-photo-finish Anyhow, you can easily tell what kind of camera you have if you take off the lens port and look inside while you turn the drive sprocket. If you see a prism spinning in there behind the lens, you have a framing camera. The prism is geared to the drive sprocket and turns in sync with it. Light going through a square prism displaces the image as the prism turns through an angle (you can see this effect looking through a thick sheet of glass). This "sweeps" the transmitted image vertically along the face of the film on the sprocket behind the prism. The image moves along at the same speed as the film on the drive sprocket, that way the image stays sharp(ish) and the film never has to stop. As far a focusing, when you look through the finder, yes, you may see an image even if you don't have focusing film in the camera. The lens is always making an image at the focal plane, even if there's nothing there to show it (an aerial image hanging in space). But you still want to use a piece of focusing film because it's impossible to tell where exactly the plane of focus is with any precision. The focusing film behaves like the ground glass in a view camera, acting as a placeholder for the exact plane the film is soon going to occupy. You want to be careful that you place the frosted side (and therefore your focal plane reference) facing outside on the drum, where the emulsion side of the film is going to be. As for framing... mine has a circular hole that shows most(ish) of the middle of the frame, but you don't really know where the exact frame lines are. At least you can find the center and this was probably plenty good enough for the original technical applications.
-
Beam Splitter on Aaton LTR 54 broke. What now?
Steve Switaj replied to Christopher Campa's topic in 16mm
Pro tip: Whenever you have to get a part custom made, always price out getting two, maybe three. The setup charges are often the largest cost of a custom piece. Once the setup is done having the 2nd or 3rd part run is usually much less expensive. Depending on the exact part, if you need it, there's a fair chance someone else needs one too, and by selling your spare you can effectively recoup some of the cost of the NRE. I'm always amazed when I do a custom electronics design and the client only asks for one. The NRE design cost itself is usually 80% of the bill, the actual fabrication ... is just a board. It's not unusual for me to quote something like "1 unit $2500. 2nd unit $1000, subsequent units $500 each" -
Shims for Cooke Varotal 20-100, T3.1
Steve Switaj replied to Deniz Cooper's topic in Lenses & Lens Accessories
Hi Guys; Fear not - You can easily do it yourself. It used to be that making shim sets was a pain because cutting the thin stock cleanly is pretty difficult without making a mess. But cheap laser cutters have changed all that. If you have enough skill to make a full sized pattern in a vector-graphics program, you can have your local laser engraving house cut out a dozen perfect shims from a sheet of plastic. I like the color-coded polyester stock that's used for "official" machinist shims. It's a known thickness and is as thermally and mechanically stable as you can reasonably expect from a thin film. It's available from .0005" to .030" (0.01 to .75mm) , so... something for everyone, basically. In the States, you can get it in 5" x 20" sheets, which is probably enough to make 7 or 8 if you space them well, available from McMaster-Carr for $4.26 ( https://www.mcmaster.com/shim-stock-rolls/color-coded-shim-stock-6/material~plastic/ ) or here's an assortment of 15 thickness for $44 https://www.mcmaster.com/9513K42/ In a pinch, you can try using some filter gel. Hate to admit it, but that has worked for me more than once. Some laser cutters can also cut thin sheets of stainless steel. Stainless foils can be found from about .001" and up ( https://www.mcmaster.com/metal-foil/stainless-steel/shape~foil/ ) If you prefer this option, try to find a commercial specialty graphics house, many of them will be familiar with using this material for masking friskets or paste stencils and have the tools at hand. -
Hi Guys; I'm rebuilding an old camera and need to find a couple of rolls of scrap 35 mm film for tuning the servos. I've managed to snap all my test rolls into little ten-foot pieces, and now I need some more. Maybe one or two rolls of, say, 250' plus. It's strictly for physical testing, emulsion is not important to me, the film can be flashed or outdated, just so long as it's in decent mechanical shape.
-
Holy crap! I never throw anything out! This is the second weird connector request that I've found in my stash this week! Two of them, this time. No, I'm not a hoarder.... I'm a .... motion control guy. Yeah, that's it! There's definitely a difference. For sure. DM me.
-
I don't know if this applies to the Cannon parts, but on most versions of the Switchcraft XLR connectors, the inner contact block is held into the connector body with a screw, usually on the latching side. On those connectors, if you have a connector you need to change but a backshell style you want to keep, you can simply find a generic 4 pin XLR and swap the contact block between backshells. Don't know if this is the case with the Cannon brand parts, they are not common on this side of the pond, but it might be worth pulling it off and taking a peek underneath.
-
ALCS Single-Speed Crystal Controller for CP16R
Steve Switaj replied to Aapo Lettinen's topic in Cinema Products
Aapo: I think I'd strongly suggest you use a smaller selector switch.. That long toggle seems awfully close to the exposed bottom edge right at the back, it feels like it's just crying out to get damaged from being pushed back on a shelf or dropped into a case at the end of the day. Maybe some kind of small rocker switch. -
Aaton LTR external frequency input (milliframe controllers etc)
Steve Switaj replied to Aapo Lettinen's topic in Aaton
Also, I found one of those weird, WPI 9-pin connectors made out of unobtanium in a box of... well.. weird connectors. If anybody has a need for it, they can have it for what I paid, which was probably about $30, plus postage to wherever it's going. DM me. -
Aaton LTR external frequency input (milliframe controllers etc)
Steve Switaj replied to Aapo Lettinen's topic in Aaton
Holy Crap, I apparently never throw anything out ! I had one of those "wait... I might have something.. " moments, and I dug around in some old project files, and in a folder marked "Aaton" I found a paper printout of part of an email conversation I had with Clive Tobin 21 freaking years ago about Aaton sync. To be an FX camera guy is to be a technical packrat. I don't know the exact question I was asking, but IIRC, I was in Australia working on the Matrix sequels and I wanted to use a couple of LTR's as 2nd-angle witness cameras for some effects we were shooting on VistaVision plates. I think. -
Making new Crystal Sync electronics for CP16R
Steve Switaj replied to Aapo Lettinen's topic in Cinema Products
3/3 The final user controls closely follow the pattern of those on the Arriflex 435 - I figured that any professional operator would be familiar with that. One thing that I felt was a big improvement was that I replaced the original 25-hole speed sensor disk with a modern 800 count quadrature encoder. Having 32 times more resolution dramatically improves speed control, but more importantly it allowed me to derive the signals I needed to update the accessory port from the original Fries type to an industry-standard 11-pin Arri port. This camera will be used in complicated VFX settings, so it has to interface with all the equipment that modern cameras are expected to work with. -
Making new Crystal Sync electronics for CP16R
Steve Switaj replied to Aapo Lettinen's topic in Cinema Products
2/3 A few years ago it coughed and sputtered out the magic smoke and decided it would run no more. It sat on a shelf for several years till the owner asked me if I could return it to operation. After about 30 minutes of tracing my way through the original circuits I realized that it wasn't going to make any sense trying to repair the mid-80's electronics. Fries had closed years ago and there was no information at all available, and even if there were, the design was built around old analog circuits and it didn't seem like a good basis for a camera controller in 2022. I figured simply rebuilding it from the bottom up was the best way forward. I designed two new boards for the camera. The first was the main control board, this included the user interface, external interface, and an LCD display. Oddly, the new boards kind of look older than the originals. The original boards used surface-mount chips but the new boards use through-hole chips so that anything programmed or exposed to an external interface could be socketed for easy replacement. Truth be told, I would have liked to use a better display. This old-school yellow/green LCD kinda screams “1990's vending machine” to me, but with supply chains being what they are, and this being a one-off, it didn't make sense spending the the time to do anything more complicated, especially since our user base only cares about the data, not the look. The electronics are otherwise straightforward. At the center is a PIC24EP family chip at 70MHz that coordinates everything. This chip has a built-in quadrature encoder interface and three PWM generators, so it makes motor control easy - once you decode the truly byzantine Microchip datasheet for these modules. There are 3 motor drivers, one each for the camera motor, takeup hub and supply hub (for backwinding). The motor drives are all unidirectional (the camera motor has a hardware reverse switch) so the 3 drivers are all 1-quadrant, simply a big MOSFET driving the low leg. The switching frequency is 20KHz to make it inaudible, which I soon realized was pointless since the camera sounds like a washing machine when it runs - it was obviously not designed for sync-sound work. The speed is variable from 1.000 to 36.000 FPS in .001fps intervals. The control system is a standard PID loop updated at 1KHz. Between the fact that a camera motor is commanded to run a constant speed, and the large rotating mass involved, the derivative term is basically useless, so after a little testing I just dropped it. -
Making new Crystal Sync electronics for CP16R
Steve Switaj replied to Aapo Lettinen's topic in Cinema Products
Hi Aapo; I've been following your cool CP-16 crystal sync project with great interest, and I wanted to share my own camera controller project. I'm kind of working at the other end of the scale, though. I got a project rebuilding the electronics for one of the old Fries VistaVision conversions. This thing is monstrous, It weighs in at 40 pounds without lens, mag, film or even finder. -
Hi guys; I was cleaning up and came across a small box of follow focus bits. I have no use for them, I think they came along with an auction lot a few years ago. If they are useful to anyone out there, you can have them for the price of the postage. 1 cable - Lemo 3 pin FG1 to Lemo 2 pin B1 (Panavision run to Panavision accessory?) 1 cable - Lemo 2 pin B1 to Lemo 2 pin B1 (Some kind of Panavision accessory power?) 1 Bracket - probably a Preston Hand Unit I/II to microforce I/II 1 set of 5 follow focus marking rings, flat, 2.58" ID, 4" OD 1 set of 5 follow Focus marking rings, flat w/ metal on the reverse (for magnetic mount?), 1.2" ID, 3.6" OD, marked "Cine-Pro" DM me if you're interested