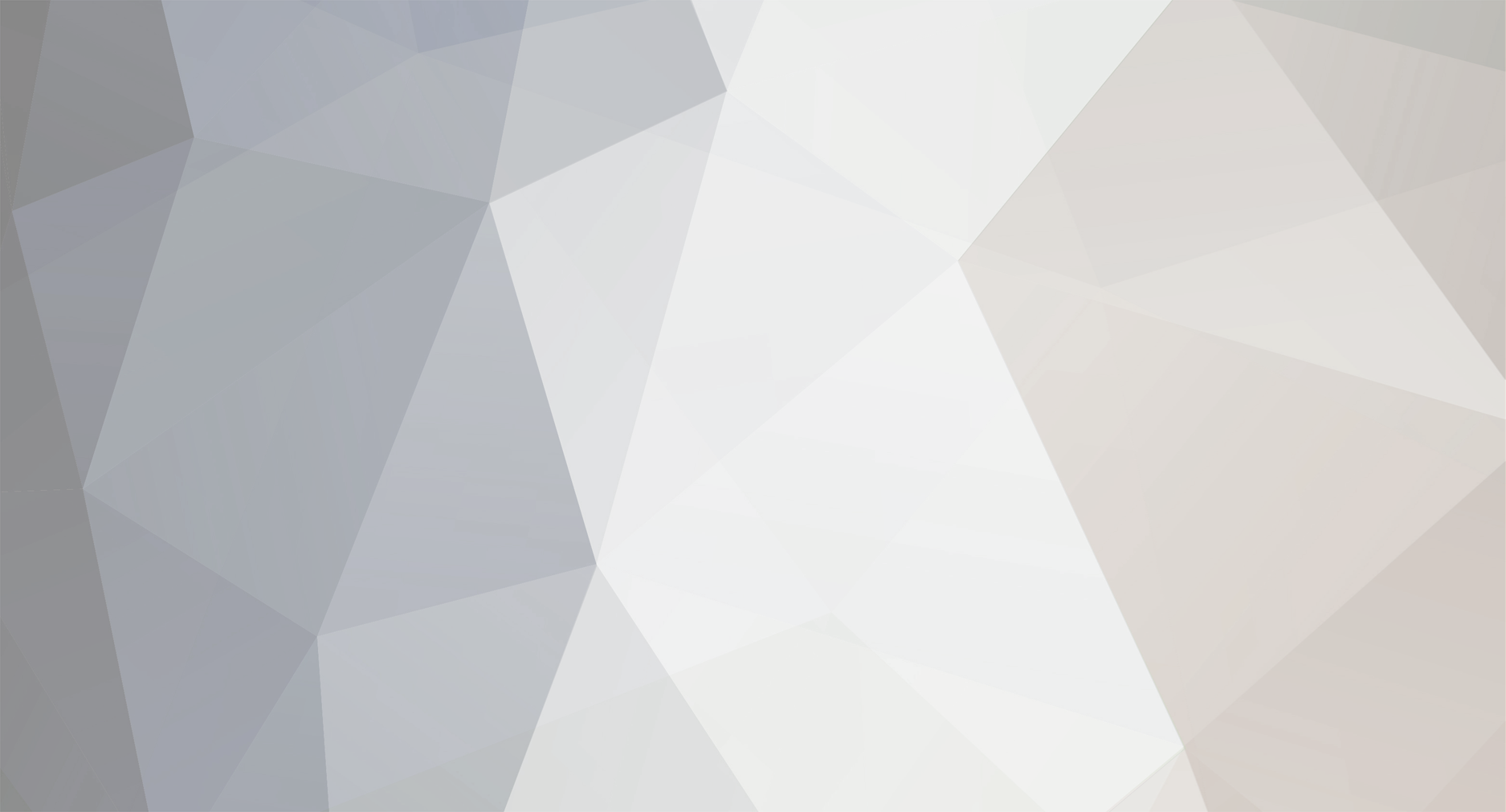
dan kessler
Basic Member-
Posts
225 -
Joined
-
Last visited
Profile Information
-
Occupation
Other
-
Location
los angeles
Recent Profile Visitors
5,812 profile views
-
Goodbye remjet, hello AHU?!
dan kessler replied to Joerg Polzfusz's topic in Film Stocks & Processing
On another thread you mentioned DLC coating as a viable solution. Have you not tried it? Does it work? -
That would be nice, but no, I just happen to have a 40 DP belt that I'm using for another project, which, coincidently, is another camera. 40 DP is one of several standard timing belt pitches that are readily available from suppliers. SDP has a huge selection, so you should have no problem getting what you need. You just need to specify the number of teeth and the width.
-
40 DP belts also available from Stock Drive Products www.sdp-si.com Holding one in my hand as we speak
-
Remembering brand name of a green tungsten head?
dan kessler replied to Max Field's topic in Lighting for Film & Video
Bardwell McAllister? Sometimes called keg lights -
Interestingly, just saw a black-and-white film noir, "Odds Against Tomorrow." Produced in 1959 by Harry Belafonte and directed by Robert Wise, who states that he used infrared film for the opening scene, where actor Robert Ryan is in an urban setting, walking towards camera. The characteristic infrared look is evident, with white, glowing skin and altered tones.
-
Kem - Bild flatbed for auction in New York
dan kessler replied to charles pappas's topic in Cine Marketplace
Don't see the picture head anywhere. Also unknown internal issues. -
The database doesn't appear to include 35mm.
-
Did anyone else on the forum notice or mention this? He died Jan. 6
-
Many reasons for the differences. Simon Wyss, who often posts here, is a great one for this kind of discussion. Meanwhile, here's another book for you: Principles of Cinematography, by Leslie J. Wheeler, 1969 Fountain Press Limited
-
Look at this crazy computer company!
dan kessler replied to Daniel D. Teoli Jr.'s topic in Off Topic
Try yahoo.com ? -
Looks exactly like the mushroom cloud from the Atomic Annie test in 1953, the one and only time a nuclear warhead was fired from an M65 cannon. The blast was recorded from approximately 6.5 miles away, with the cannon in the FG in the original footage. Definitely comped here. The explosive yield was around 15 kilotons, similar to the bomb that fell on Nagasaki.
-
Not only is the whole process astounding, but the tolerances of some of the components that had to be machined are mind-blowing. For example, those solid titanium bars in the coating machines. They're what -- 3 or 4 feet long, machined, ground and polished over their entire length to a tolerance of fifty millionths of an inch. In machinist's parlance, that's half a tenth, or half a ten-thousandth of an inch. Holding that over the entire length along with the smoothness tolerance in some of the world's toughest material will make your head explode. And they've got stacks of those things! I think of the shop and the people who made them and just absolutely cringe. Oh yeah, and then the coating machine is mounted on its own independent foundation that goes down to bedrock below the building. All just so we can shoot film.