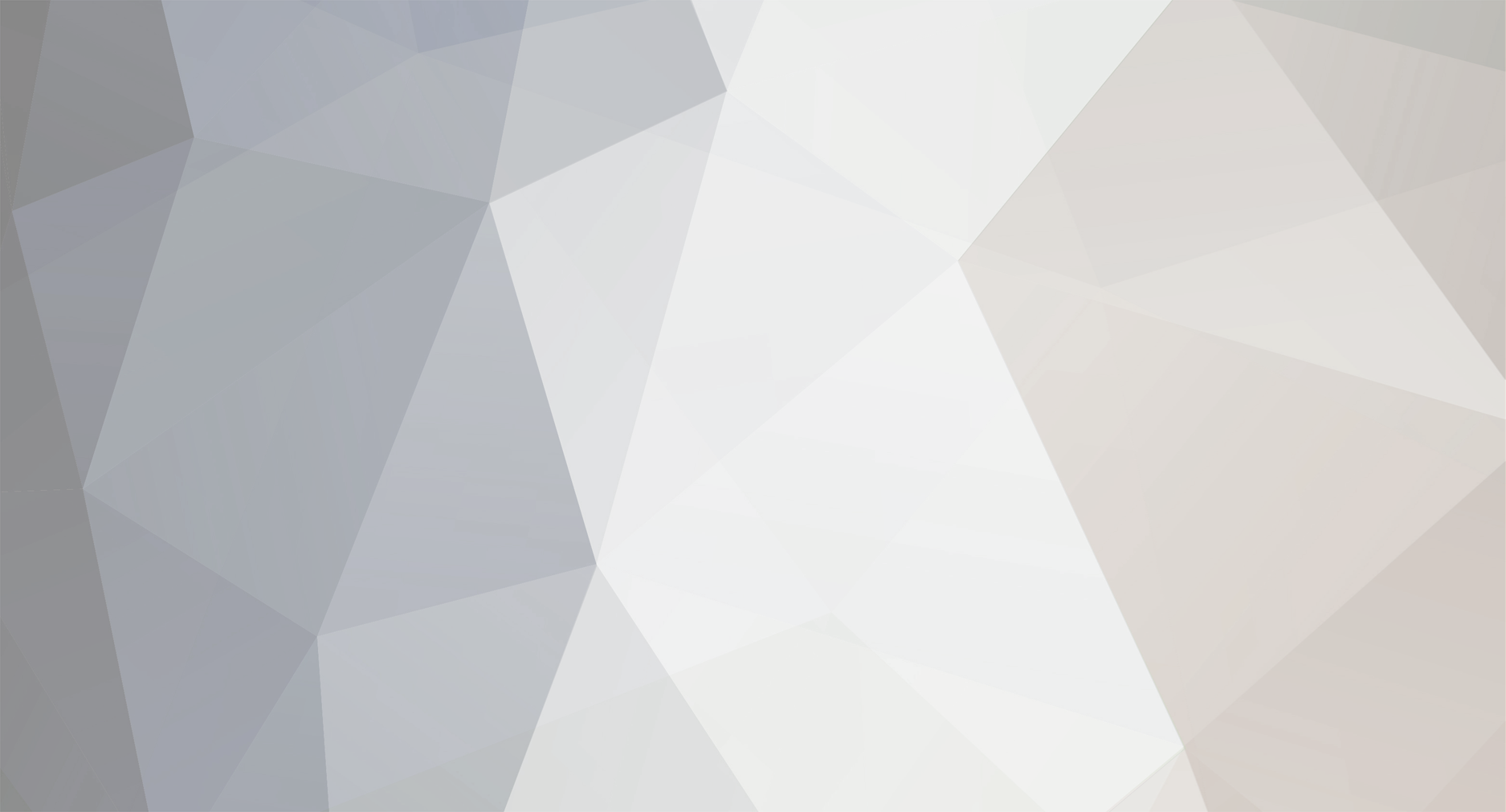
Charles MacDonald
Premium Member-
Posts
1,217 -
Joined
-
Last visited
About Charles MacDonald

Profile Information
-
Occupation
Other
-
Location
Stittsville Ontario Canada
-
Specialties
Real Photography. - I am an old A/V Geek at heart
Recent Profile Visitors
-
in the still Photography forums, many report that Kodak is only wanting to sell 35mm cine film to legitimate Movie productions these days.... B&h does have a small selection of 16mm Movie Negative and so is "handy" for 16mm filmmakers, but again if you have a major project you will do better by contacting Kodak.
-
Kodak Tri-x 7278 vs 7266
Charles MacDonald replied to Christian Flemm's topic in Film Stocks & Processing
I belive that the recommended process was changed to avoid a chemical that the EPA had some concerns about. Both Plus-X and Tri-X reversal got new versions, although the old versions, would work in the new process with some exposure adjustments. -
What kind of 8mm film cartridge is this?
Charles MacDonald replied to Daniel D. Teoli Jr.'s topic in Film Stocks & Processing
also used in Schools. as point of sale device and other. My high school back in the late 1960s had a set of front Projection versions which had cartriges made by the National Film board of Canada, which the students could use to measure some phisics experiments ( never came up in my classes so I only saw then from afar) as indicated by the label on the top one also used for Staff Training on new products. -
the Bolex lenses are only for a bolex. you should use a regular C-mount lens. B&H often shipped these with "Comat" lenses (Super Comat C-Mount Lens) you will need a viewfinder objective that matches the focal length of your lens. If you are lucky you will have a couple of the objectives in the turret and can pick a lens to suit. since the B&H Filmo oil is no longer made. Many folks will use a VERY SMALL drop of sewing machine oil. (This is what I use, but I am not sure of their is not a better product to use) I can't quickly find a good like to a 70DR user manual, although Archive dot org has a manual for an ealier version.
-
the time when Kodak was in an "Arms Race" with FujiFilm was when we saw the Vision Line quickly go to vision 2 and then Vision 3. Fuji backed away, and without the demand and competition, there is little incentive to re-work into a vision 4. Perhaps if Christopher Nolan were to get a contract to produce a series of 12 movies all on IMAX, that required some very high speed film, there MIGHT be an incentive to do some R&D. But as a strictly amateur photographer, I would LOVE to see someone make a 40ASA reversal film in both B&W and colour. Their are SO MANY nice super 8 cameras that will only work in their native mode with 40T film.
-
Kodak 16 mm edge code assistance
Charles MacDonald replied to David Tilotta's topic in Film Stocks & Processing
Often the two digit code has been assumed to be the Strip number cut from the master roll. (1 through 38 for 35 mm and 1 through 83 for 16 mm) Back before Key code, the strip number was sometimes indicated by a sticker on the can the film originally came in. -
it will work, But in your pre-planing figure out what sort of light you expect to have. All Sunny Days, you will have more control with 50D. Studio inside, that is where 500T will shine. Mostly outside well 200D might be what you need, with a few ND filters on hand to let you open the lens wwhere youwant the backgrounds to fall out of focus... and 200T will also work with the all important 85 filter. if you need to shoot in both places. some productions do just use the 500T with a set of the various 85N2, 85N3 filters as needed.
-
My 1924 Victor Ultra Cine. Battery Operated!
Charles MacDonald replied to Robert Murphy's topic in 16mm
if you want to USE this, you will find that Single perf film is Much easier to find, But you will have to check that the pulldown claw is on the correct side for single perf film. -
And if you read the fine print, most folks selling the magazines have a hefty deposit to get the magazines which have not been made for many many years to be returned to be refilled. I understand that FFP arranged to get some unperforated film from Kodak, and had it perforated 2R by a firm in Europe.
-
well, it LOOKS like a complete setup. the Optical sound Galvo is present. The nameplates on the amp are not readable to confirm that they amp matches the Camera. BUT the chances are reasonable that the setup Might be complete. expect that the Electronics Might need some tweaking, but in theory It should be able to record Optical sound. If Jack sees the post he may have other things to add.
-
when large quantities were needed, like to send out slides to every dealer of a product, preparing the slides using Motion Picture materials was also possible. there was also a Ektacolor Positive film for making slides from a "still" colour negative image. (still film and Movie film having different contrast ranges) other makers also had a duplicating reversal film like Ansco 5479. (don't know why I remember that one) in fact Kodak themselves would make duplicates using a Kodachrome duplicating material.
-
Using Kodak Film with a Fuji-Film Daylight Spool?
Charles MacDonald replied to Anthony Wilson's topic in Bolex
sounds like it is bent... fuji and Kodak, even old dupont, ansco and Ferrannia spools should all work fine as a takeup spool. of course FUJI spools are going to be collectors items now. -
Anybody selling Double Perf 16mm for D8?
Charles MacDonald replied to Andrew Glenn Miller's topic in 16mm
FPP has used a firm in Germany who has a large selection of perforating machines prepair both double perf 16mm as well as Double 8. (the two are different pitch) the video shows the process, although they would have had to do the actuall work in the dark... this page from another dealer has some details. http://www.toeppenfilm.com/about8mm.html